Shuttle fuel burn
Join Date: Sep 2007
Location: USA
Posts: 601
Likes: 0
Received 0 Likes
on
0 Posts
NASA performed studies of a fully re-usable system just prior to the Shuttle program start. And much later on studied a Liquid Fly Back Booster (LFBB) concept that would replace the SRBs.
As for reducing $/lb launch costs, it will be interesting to see how effective the StratoLaunch system works out.
As for reducing $/lb launch costs, it will be interesting to see how effective the StratoLaunch system works out.
This is not quite like it seems because of the v^2 term. Mach 7 is only 7.8% of orbital kinetic energy.
It seems to me the words often attribute to Ed Henneman are very applicable here. Simplicate and add lightness.
Rockets seem to accomplish that.
Rockets seem to accomplish that.
Lots of people thought Musk was nuts when he proposed to use a powered descent and landing to recover his first stage - but he's close to making it work and is on record as stating that, once perfected, it'll reduce orbital costs by at least an order of magnitude (and Space X is already one of the cheapest per pound). Yes, it adds cost, weight, and complexity, but he's a pretty sharp guy, with some pretty sharp people working for him and if can successfully undercut the competition by an order of magnitude on costs, all the others are going to be in a mad scramble to avoid being completely left out.
As long as we persist in throwing away most of our launch vehicles after a single use, space is going to remain prohibitively expensive. Of course, if we persist in leaving thousands of pieces of used rockets and other debris up there, low earth orbit may well become unusable in another 20 years or so...
Join Date: Sep 2007
Location: USA
Posts: 601
Likes: 0
Received 0 Likes
on
0 Posts
While I agree that Mr. Musk is bright guy, and SpaceX has made progress in reducing the $/lb of commercial launch costs, your claim that SpaceX will lower the $/lb of commercial launches by "an order of magnitude" is not realistic. According to the SpaceX website, the $/lb price of an LEO Falcon 9 is over $2K, not including other costs such as insurance, etc.
Commercial space launch is a business, and launch services are priced based on what customers are willing to pay versus the competition.To propose that SpaceX would offer launches at 1/10 the price of their competitors ignores basic market economics.
Commercial space launch is a business, and launch services are priced based on what customers are willing to pay versus the competition.To propose that SpaceX would offer launches at 1/10 the price of their competitors ignores basic market economics.
Join Date: Jun 2014
Location: Village of Santo Poco
Posts: 876
Likes: 0
Received 0 Likes
on
0 Posts
A cheap and simple 1916 biplane may be more suitable for, say, cropdusting and barnstorming than a complex and expensive 2016 airliner, however.
In other words, to Caesar that which is Caesar's and to Bubba Ray that which is Bubba Ray's.
In other words, to Caesar that which is Caesar's and to Bubba Ray that which is Bubba Ray's.
Join Date: Jul 2001
Location: Nashville
Posts: 72
Likes: 0
Received 0 Likes
on
0 Posts
Originally Posted by riff_raff
"...your claim that SpaceX will lower the $/lb of commercial launches by "an order of magnitude" is not realistic. According to the SpaceX website, the $/lb price of an LEO Falcon 9 is over $2K, not including other costs such as insurance, etc...."
Falcon Heavy | SpaceX
This is important because any alternative launcher, whether existing or planned, expendable, reusable, air breathing, etc, must compete with that number. That is already cheaper by an order of magnitude than the space shuttle was. Compared to the Delta IV Heavy ($5,908 per lb to LEO), it is 7.76 times cheaper.
While I agree that Mr. Musk is bright guy, and SpaceX has made progress in reducing the $/lb of commercial launch costs, your claim that SpaceX will lower the $/lb of commercial launches by "an order of magnitude" is not realistic
Join Date: Jul 2001
Location: Nashville
Posts: 72
Likes: 0
Received 0 Likes
on
0 Posts
Originally Posted by tdracer
"...An air breathing launch vehicle that could carry an orbiter to ~120,000 ft./Mach 7 (or better) would mean the orbiter wouldn't need to be huge to carry the fuel to get into orbit.""
Originally Posted by joema
"...because of the v^2 term. Mach 7 is only 7.8% of orbital kinetic energy..."
Originally Posted by tdracer
"Wrong, quite wrong. Rockets engines are effectively constant thrust devices, not constant power. Discounting aerodynamic drag, it takes exactly the same amount of thrust to accelerate a given mass from zero to 10,000 ft./sec. as it does to accelerate from 10,000 to 20,000 ft./sec."
Since the development cost of similar aerospace vehicles tends to scale upward with gross mass, It is conceivable a TSTO design with a Mach 7 booster would cost more than one with a Mach 12 booster. This can be non-intuitive, but some relevant data and research are in this graph, taken from "Propulsion and Staging Considerations for an Orbital Sortie Vehicle (Stengel, 1987):
https://joema.smugmug.com/Aerospace/...6t/i-nKLmZSR/O
Original paper (PDF): http://www.princeton.edu/~stengel/Prop.pdf
A reusable air-breathing first stage does seem compelling and has been discussed and studied many times. The problem is it requires a very large, very heavy, very complex hypersonic airbreathing launch vehicle, whether that is Mach 7 or Mach 12. Maybe a lower, more achievable staging velocity is the answer, providing a lighter, less expensive launcher?
E.g, assume launch vehicle is twice the gross weight of an XB-70 (about 1 million lbs), and can reach Mach 5 @ 120,000 ft. Mach 5 is a good number because it is (barely) within ramjet limits so avoids the uncertainty, development risk and extra mass of scramjets.
Assume it can carry twice the XB-70 external payload, about 100,000 lbs. Given a Mach 5 running start, could a 100,000 lb winged manned orbiter reach orbit with any useful payload?
The X-15A-2 had a mass ratio of about 0.72. We'll assume technical progress improves this to 0.8. The XLR-99 engine had an ISP of about 256 sec. Assume ISP improves to about 314 sec. Rough guess at exhaust velocity: 3000 m/sec. Using the rocket equation, this gives:
delta V = Ve * ln (full mass/dry mass)
delta V = 3000 m/sec * ln (45000 kg / 9000 kg)
delta V = 4828 m/sec (10,800 mph)
This would give a final delta V (launch ship + drop ship) of roughly 6,528 meters/sec, far short of 8,000 m/sec orbital velocity.
Thus it appears a winged, manned orbiter could not reach orbit -- even with zero payload -- if boosted to Mach 5 by a ramjet-powered XB-70 successor with double the payload capacity.
Air-breathing winged launchers and winged orbiters look cool, and have long been romanticised. However in the real world they don't work that well. This was discussed by Henry Spencer in the article "Rockets, not air-breathing planes, will be tomorrow's spaceships":
https://www.newscientist.com/blogs/s...hing-plan.html
As I stated, because KE=1/2*m*v^2, it takes tremendous kinetic energy to reach orbit. A Mach 7 reusable booster is easier to design but it makes the orbiter much heavier. This is because the remaining delta-V is a squared term, hence energy required falls disproportionately on the orbiter.
I won't bother with the rest of your analysis because it's based on a flawed assumption.
Commercial space launch is a business, and launch services are priced based on what customers are willing to pay versus the competition.To propose that SpaceX would offer launches at 1/10 the price of their competitors ignores basic market economics.
About this claim with respect to return to launch pad
once perfected, it'll reduce orbital costs by at least an order of magnitude
Given that the 2nd stage would have to start its recovery maneouver at around Mach 25, the weight of thermal protection alone will eat directly into the revenue payload. I don't have the maths for it but my gut feel is that it would net an *increase* in $/lb to orbit.
But... if (big if) the cost of the launching h/w is proportional to the engines, then: 1st stage=9 Merlins; 2nd stage=1 Merlin. A divide by 10, right here.
Perhaps the claim wasn't that far fetched, if we allow a few qualifiers.
One argument weighting against the "reusables" is that such approach cuts into production rate and thus raises the cost of the few launchers that are being build (reduced economies of scale, etc.). Being valuable means that the launch will now include loss insurance. Also, being more valuable, there will be an incentive to make them more wear and random failure proof, farther eating into our mass. All such insidious practicalities will erode the final $/lb.
Personally, I can't wait until they announce that they are flying a refurbished stage and tell us what it took.
Join Date: Jan 2007
Location: Under a rock
Posts: 33
Likes: 0
Received 0 Likes
on
0 Posts
3D printing though is really changing the economics for building many of these unique and complicated parts versus when the space shuttles were flying.
Join Date: Jul 2001
Location: Nashville
Posts: 72
Likes: 0
Received 0 Likes
on
0 Posts
Originally Posted by tdracer
"An air breathing launch vehicle that could carry an orbiter to ~120,000 ft./Mach 7 (or better) would mean the orbiter wouldn't need to be huge to carry the fuel to get into orbit."
Originally Posted by joema
...because KE=1/2*m*v^2, it takes tremendous kinetic energy to reach orbit. A Mach 7 reusable booster is easier to design but it makes the orbiter much heavier. This is because the remaining delta-V is a squared term, hence energy required falls disproportionately on the orbiter.
Originally Posted by tdracer
...Wrong, quite wrong. Rockets engines are effectively constant thrust devices, not constant power....No, you're missing basic physics. Acceleration is directly proportional to force, and in this case force and thrust are the same thing...I won't bother with the rest of your analysis because it's based on a flawed assumption.
Another example is the Space Shuttle, which at SRB sep is at Mach 4.5 and 150,000 ft. About 77% of ET propellent is remaining, so the remaining stack is about 2.2 million pounds. Mach 4.5 is a good number because it's achievable with ramjet propulsion at much lower cost and technical risk than scramjets.
A hypothetical air-breathing first stage which injected the shuttle orbiter plus ET to Mach 4.5 at 150,000 ft. would reduce the required ET propellant by 23%. The remaining orbiter stack would still be a gigantic vehicle weighing 2.2 million lbs. Why? Because of the remaining tremendous kinetic energy required to reach orbit.
So these examples illustrate the difficulty of an air-breathing first stage. One key reason is the highly non-linear affect of the kinetic energy V^2 term. Boosting to Mach 4.5 or Mach 7 doesn't help that much, yet would require a titanically expensive and complex winged air-breathing booster.
The non-linear effect of how kinetic energy affects this can be easily seen in the near-vertical curve on the left side of the staging velocity chart: https://joema.smugmug.com/Aerospace/...6t/i-nKLmZSR/O
This also explains why subsonic air launch has almost no benefit to orbiter mass. This was discussed in the AIAA paper "A Study of Air Launch Methods for RLVs
(Sarigul-Klijn, et al, 2001): http://tinyurl.com/z7zstrm
""Surprisingly, a typical straight and level subsonic horizontal air launch such as used by the X-15 research rocketplane does not result in any significant changes in the delta V requirement as compared to a baseline vertical surface launch."
There are groups still working on air-breathing SSTO and TSTO launchers such as Skylon and Bristol. I wish them well but I doubt they will be successful. Even if they were successful, they would still have to compete with SpaceX price/performance, while amortizing the huge development cost of airbreathing hypersonic vehicles:
Skylon: Reaction Engines Ltd - Space Access: SKYLON
Bristol SpaceBus: Spacebus | Bristol Spaceplanes
Air-breathing SSTO is not dumb -- the brilliant designer Tony duPont conceived the original NASP design and it first appeared possible. However DARPA recently re-evaluated this in light of technical growth and believes it is still not possible: http://www.nytimes.com/2014/10/21/sc...ress.html?_r=0
NASP and follow-on research indicates scramjets and the associated penalties of multiple propulsion systems, active cooling, etc, cannot remotely reach orbit and are not good candidates for a 1st stage reusable launcher. It now appears the main application for hypersonic airbreathing propulsion is military -- long-range hypervelocity missiles.
However a reusable non-airbreathing 1st stage is possible for smaller payloads - the XS-1 is a good example: US Military Awards New Contracts for XS-1 Space Plane
The problem is even with the projected reuse savings of that booster, their payload cost per lb is already higher than SpaceX on the Falcon Heavy ($1,000 vs $770). It may have other advantages such as quick reaction and flexibility.
Join Date: Sep 2007
Location: USA
Posts: 601
Likes: 0
Received 0 Likes
on
0 Posts
Right, you are. But let's stick to the launch costs; not the launch price tag. The cost is very much a component of engineering and hence more interesting in Tech Log.
From what I have seen there is not enough difference in the technology or design of the current SpaceX Falcon 9 booster and other existing boosters to justify the claims of massive reductions in launch costs. The current expendable Falcon 9 uses fairly conventional materials and design. The only major difference seems to be that SpaceX employs a more efficient manufacturing process.
Can someone provide an explanation of why a launch on an expendable SpaceX Falcon 9 vehicle could be so much cheaper than other similar launchers?
Join Date: Jul 2001
Location: Nashville
Posts: 72
Likes: 0
Received 0 Likes
on
0 Posts
Originally Posted by riff_raff
"From what I have seen there is not enough difference in the technology or design of the current SpaceX Falcon 9 booster and other existing boosters to justify the claims of massive reductions in launch costs. The current expendable Falcon 9 uses fairly conventional materials and design. The only major difference seems to be that SpaceX employs a more efficient manufacturing process....Can someone provide an explanation of why a launch on an expendable SpaceX Falcon 9 vehicle could be so much cheaper than other similar launchers?"
Apparently the main answers are SpaceX launchers were designed from scratch with cost reduction as a primary goal, they do most things in house rather than subcontract, and their business organization is very lean. Here are some articles discussing it:
Air & Space: "Is SpaceX Changing the Rocket Equation?" History, Travel, Arts, Science, People, Places | Air & Space Magazine
Motherboard: "How Elon Musk Willed SpaceX Into Making the Cheapest Rockets Ever Created" How Elon Musk Willed SpaceX Into Making the Cheapest Rockets Ever Created | Motherboard
Join Date: Jun 2009
Location: Canada
Posts: 464
Likes: 0
Received 0 Likes
on
0 Posts
And reusability will massively reduce costs, if they can reuse a stage a few times with minimal refurbishment. If returning the first stage to the launch site cuts 1/3 off the payload, and you can reuse it only twice more without replacing or overhauling the engines, you've nearly halved the cost in $/lb to orbit.
Shuttle Roll Manoeuvre
Does anyone know why they didn't reorient the shuttle on the launch pad, instead of performing the roll manoeuvre?
Join Date: Mar 2015
Location: XFW, Germany
Posts: 128
Likes: 0
Received 0 Likes
on
0 Posts
I would say that this explains it a bit with the bottom line: historical deps

Join Date: Sep 2007
Location: USA
Posts: 601
Likes: 0
Received 0 Likes
on
0 Posts
Because it's designed to be cheap, rather than efficient.
You bring up a very interesting point regarding the trade off between cost and efficiency. Long before Elon Musk and SpaceX came along, there was a very bright entrepreneur named Andy Beal. Beal Aerospace's goal was building a heavy launch vehicle that would drastically reduce the $/lb cost of commercial launches. But rather than pursuing a reuseable design, his approach was to make the vehicle as simple and inexpensive to produce as possible. Of course the trade off was reduced performance.
The BA-2 heavy launcher used a single massive peroxide/kerosene engine for each of the first two stages. The engines were pressure fed from the propellant tanks and did not require turbo pumps. The composite propellant tanks were pressurized using helium. The engines used un-cooled (ablative) nozzles. Beal actually made quite a bit of progress with his limited resources. To give you an idea of the size of the engines, here's an image of the second stage engine being test fired:
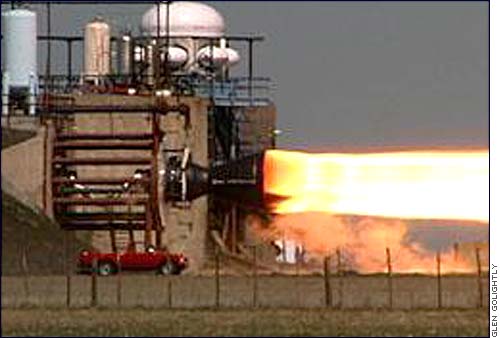
Join Date: Jul 2001
Location: Nashville
Posts: 72
Likes: 0
Received 0 Likes
on
0 Posts
When you consider the limited tools NASA had to work with, the shuttle was one of the greatest aerospace achievements in history. Besides all the issues with structures, dynamics and propulsion on ascent, no winged hypersonic vehicle (manned or unmanned) had ever reentered from orbit. There was very little data.
When the shuttle was designed in the mid-1970s, CFD was incredibly primitive, and hypersonic wind tunnels extremely limited. Yet the shuttle successfully flew a manned mission on the first flight.
Decades later, one reason (of many) NASP failed was continuing limitations in CFD and hypersonic wind tunnels. Unfortunately this is still a problem today, despite the much faster computers. This is due to limitations in CFD models and the fact that most demanding CFD problems are four dimensional. Every factor of two improvement in grid resolution requires a computational speed increase of 16 times. This is why hypersonic test vehicles like the X-43 and X-51 are so vital: even today, CFD cannot comprehensively simulate the required flow characteristics, and hypersonic wind tunnels are too limited in speed, duration and data quality.
This history is detailed in the book "Facing the Heat Barrier: A History of Hypersonics", which is available on line in PDF format:
Part 1: history.nasa.gov/sp4232-part1.pdf
Part 2: history.nasa.gov/sp4232-part2.pdf
Part 3: history.nasa.gov/sp4232-part3.pdf
SpaceX is doing a lot of leading edge work in CFD. Here is an interesting article with some links to some simulations:
Rockets Shake And Rattle, So SpaceX Rolls Homegrown CFD
When the shuttle was designed in the mid-1970s, CFD was incredibly primitive, and hypersonic wind tunnels extremely limited. Yet the shuttle successfully flew a manned mission on the first flight.
Decades later, one reason (of many) NASP failed was continuing limitations in CFD and hypersonic wind tunnels. Unfortunately this is still a problem today, despite the much faster computers. This is due to limitations in CFD models and the fact that most demanding CFD problems are four dimensional. Every factor of two improvement in grid resolution requires a computational speed increase of 16 times. This is why hypersonic test vehicles like the X-43 and X-51 are so vital: even today, CFD cannot comprehensively simulate the required flow characteristics, and hypersonic wind tunnels are too limited in speed, duration and data quality.
This history is detailed in the book "Facing the Heat Barrier: A History of Hypersonics", which is available on line in PDF format:
Part 1: history.nasa.gov/sp4232-part1.pdf
Part 2: history.nasa.gov/sp4232-part2.pdf
Part 3: history.nasa.gov/sp4232-part3.pdf
SpaceX is doing a lot of leading edge work in CFD. Here is an interesting article with some links to some simulations:
Rockets Shake And Rattle, So SpaceX Rolls Homegrown CFD
Join Date: Sep 2007
Location: USA
Posts: 601
Likes: 0
Received 0 Likes
on
0 Posts
Indeed, one of the biggest engineering challenges facing the shuttle designers was aero compression heating on the structures. However, they did benefit from related work done on the X-15 program.
Even SpaceX has wisely adopted technology developed by their competitors. They are using a material (Al-Li alloy) and construction method (friction stir welding) developed for the Delta IV common booster core, to reduce cost and improve reliability on their Falcon 9 vehicle.
Lastly, it was nice to see Blue Origin successfully land their booster a second time. They have had no problems with their landing gear, so maybe the mechanical systems engineering group at SpaceX could ask them for advice.
Even SpaceX has wisely adopted technology developed by their competitors. They are using a material (Al-Li alloy) and construction method (friction stir welding) developed for the Delta IV common booster core, to reduce cost and improve reliability on their Falcon 9 vehicle.
Lastly, it was nice to see Blue Origin successfully land their booster a second time. They have had no problems with their landing gear, so maybe the mechanical systems engineering group at SpaceX could ask them for advice.
