were any big radials reliable
Join Date: Apr 2002
Location: over here
Posts: 472
Likes: 0
Received 0 Likes
on
0 Posts
A friend of mine showed me this yesterday...
YouTube - Bristol Hercules sleeve valve radial animation
and we're still looking for a pair of Hercules Mark XVII's, if anybody trips over a couple on their travels!
YouTube - Bristol Hercules sleeve valve radial animation
and we're still looking for a pair of Hercules Mark XVII's, if anybody trips over a couple on their travels!
Join Date: Feb 2005
Location: flyover country USA
Age: 82
Posts: 4,579
Likes: 0
Received 0 Likes
on
0 Posts
Brian:

To be fair, many/most jets had teething troubles too. The inaugural PAA 747 flight JFK-LHR had JT9D hot starts from tailwind during lightup. The CF6-50 had compressor fires (abradeable epoxy LPC shrouds, titanium case,...). Did the RB ever lose its combustor foghorn during startup? Some problems were alleviated by procedural changes, most were finally resolved by improved engineering.

To be fair, many/most jets had teething troubles too. The inaugural PAA 747 flight JFK-LHR had JT9D hot starts from tailwind during lightup. The CF6-50 had compressor fires (abradeable epoxy LPC shrouds, titanium case,...). Did the RB ever lose its combustor foghorn during startup? Some problems were alleviated by procedural changes, most were finally resolved by improved engineering.
Join Date: Jan 2008
Location: Frome - where we do as Fromans do.
Age: 68
Posts: 57
Likes: 0
Received 0 Likes
on
0 Posts
From LeadSled...
The story of the R-2800 is very interesting, in the development/early production days, there were severe harmonic vibration problems, but some very smart people got to the bottom of the problems --- and the engine in service developed the good reputation mentioned here. For anybody of an engineering bent, the development story, and harmonics never observed before, and their cure, is a fascinating story.
The story of the R-2800 is very interesting, in the development/early production days, there were severe harmonic vibration problems, but some very smart people got to the bottom of the problems --- and the engine in service developed the good reputation mentioned here. For anybody of an engineering bent, the development story, and harmonics never observed before, and their cure, is a fascinating story.
The story is here... a great read for those interested in the technicalities;
http://www.enginehistory.org/NoShort...Crankshaft.pdf
Thanks JG, a good read.
Just happened to find this on another forum as well.
YouTube - Pratt & Whitney R-4360 Wasp Major Cutaway
I never really got to operate any radials - apart from a Alvis Leonides in a Scottish Aviation Twin Pioneer a couple of times - and have spent most of my time on turbines. I still treated turbines with kid gloves; I'd warm them carefully and let them cool down as much as possible before shutdown. I'd also make power changes as slowly as possible to slow the temperature cycles.
Just happened to find this on another forum as well.
YouTube - Pratt & Whitney R-4360 Wasp Major Cutaway
I never really got to operate any radials - apart from a Alvis Leonides in a Scottish Aviation Twin Pioneer a couple of times - and have spent most of my time on turbines. I still treated turbines with kid gloves; I'd warm them carefully and let them cool down as much as possible before shutdown. I'd also make power changes as slowly as possible to slow the temperature cycles.
short flights long nights
I am amased to read all this...my life is "auto start on...fuel control switch on...FADEC take over..."

The first aircraft start-up I ever recollect seeing, as a schoolkid, was a Dan-Air Airspeed Ambassador, with Bristol Centaurus radials, at Liverpool airport, starting up after an overnight stay.
The huge clouds of smoke (someone once wrote that it was LVPs for five minutes after an Ambassador started up) came from a basic design concept of a radial. The crankshaft is in the centre, with cylinders radiating all around. The crankshaft is as oil-tight as can be achieved with something which needs to flex, and handle thermal expansion, in other words not perfect. So as the aircraft stands and cools down oil inevitably creeps down from the centre into the lower cylinders. The Centaurus was a sleeve-valve engine, and I am not sure if it had piston rings, but seemed more prone than most to this oil seepage. When you started up the oil was just burned off as the cylinders ignited, and this was the source of the smoke.
Oil consumption was apparently extraordinary compared to nowadays, lubricating oil was delivered in bulk bowsers. 56 gallon tanks on each engine on some types, and consumption that worked up to 5 gallons per hour, when it was time for an overhaul. Aircraft could be limited by lubricating oil range as much as fuel range. If you think about it, 56 gallons x 4 engines, and at 10 lbs per gallon (not sure) that is one ton of lube. And by the time you got from Shannon to Gander most of that would be gone.
The last radial startup I saw was the DC-6 which came into London City for the airshow some 18 months ago, handled by guys who sometimes post on here. Nothing of the spectacle has been lost over the years !
The huge clouds of smoke (someone once wrote that it was LVPs for five minutes after an Ambassador started up) came from a basic design concept of a radial. The crankshaft is in the centre, with cylinders radiating all around. The crankshaft is as oil-tight as can be achieved with something which needs to flex, and handle thermal expansion, in other words not perfect. So as the aircraft stands and cools down oil inevitably creeps down from the centre into the lower cylinders. The Centaurus was a sleeve-valve engine, and I am not sure if it had piston rings, but seemed more prone than most to this oil seepage. When you started up the oil was just burned off as the cylinders ignited, and this was the source of the smoke.
Oil consumption was apparently extraordinary compared to nowadays, lubricating oil was delivered in bulk bowsers. 56 gallon tanks on each engine on some types, and consumption that worked up to 5 gallons per hour, when it was time for an overhaul. Aircraft could be limited by lubricating oil range as much as fuel range. If you think about it, 56 gallons x 4 engines, and at 10 lbs per gallon (not sure) that is one ton of lube. And by the time you got from Shannon to Gander most of that would be gone.
The last radial startup I saw was the DC-6 which came into London City for the airshow some 18 months ago, handled by guys who sometimes post on here. Nothing of the spectacle has been lost over the years !
Last edited by WHBM; 24th Mar 2010 at 18:32.
Join Date: Jun 2001
Location: In da north country
Age: 62
Posts: 452
Likes: 0
Received 0 Likes
on
0 Posts
Back in the late eighties/early nineties, the company I worked for had been operating DC-6's (R2800) for many years. We got into the DC-8's at that time, 54's and 55's. Get this! WE had better engine reliability on our DC-6's than we did our DC-8's. I happened to be dual qualified as an engineer at the time, and I never would have believed it had I not seen it!
Our company was contracted to go to Miami and do the island grocery run for Trans Air Link. They were having an exceptionally hard time completeing the 6 leg roundtrip back to miami with four motors running. Well, we managed to complete the 6 week contract without shutting one down.
Engine reliability had a lot to do with how the engineers treated the engines.
Hell yes, big radials were reliable!
I have some friends that flew skydivers in the Southern Cross DC-3 in Z-hills, and it had Wright 1820's on it. they managed to do very well with their engines. Again, it had sooo much to do with how they were treated!
Our company was contracted to go to Miami and do the island grocery run for Trans Air Link. They were having an exceptionally hard time completeing the 6 leg roundtrip back to miami with four motors running. Well, we managed to complete the 6 week contract without shutting one down.
Engine reliability had a lot to do with how the engineers treated the engines.
Hell yes, big radials were reliable!
I have some friends that flew skydivers in the Southern Cross DC-3 in Z-hills, and it had Wright 1820's on it. they managed to do very well with their engines. Again, it had sooo much to do with how they were treated!
Join Date: Oct 2003
Location: In an Airplane
Posts: 125
Likes: 0
Received 0 Likes
on
0 Posts
Flying Radials is kinda like a dose of the Clap......
You're having fun when you catch it....
After a while it really starts to be painful....
However once cured....you think back and say...
Well hell it wasn't that bad.....
Not that I've ever had the clap
You're having fun when you catch it....
After a while it really starts to be painful....
However once cured....you think back and say...
Well hell it wasn't that bad.....
Not that I've ever had the clap

Join Date: Apr 2005
Location: Australia
Posts: 1,414
Likes: 0
Received 0 Likes
on
0 Posts
To Brian Abraham. Thank you so much for placing on Pprune that wonderful description of the operation of the R2800. Having spent time as a QFI on the Convair 440 Metropolitan of the RAAF VIP squadron, I can identify with everything packed into the description you provided. I have copied the description you supplied and it is now tucked among the pages of my flying log book of that era as a happy piece of nostalgia of the good old days. Again, thanks.

Not entirely, lynn789. Even the RR Spey could be a bit recalcitrant when asked to start on a cold morning. This was often exacerbated by the "plugs" being damp. When the fuel eventually ignited in the combustion chambers, the unburned fuel downstream would also light-up, pushing a flame out of the back end. "Milking" the HP (fuel valve) cock - in an attemt to avoid exceeding the maximum TGT (turbine gas temp) - could get you into trouble if the CSDS (constant-speed [AC generator] drive-cum- [engine] starter) drive-shaft sheared, an occasional inconvenience. Something similar could happen on hot days if the APU (or HP-air start-truck) was not delivering enough air pressure, leading to the N2 (HP) shaft not rotating fast enough for the engine to cope with the introduction of fuel. Again, high temperatures at the back end of the engine would be the result.
One aspect of Brian Abraham's guide to the P&W 2800 surprised me. On the P&W 1830, do we not have the mags on from start of engine rotation ("meshing"), and only introduce the fuel when the requisite number of blades have passed the window? Don't recall any priming being required (but it's been 42 years). If I'm right, why the difference?
One aspect of Brian Abraham's guide to the P&W 2800 surprised me. On the P&W 1830, do we not have the mags on from start of engine rotation ("meshing"), and only introduce the fuel when the requisite number of blades have passed the window? Don't recall any priming being required (but it's been 42 years). If I'm right, why the difference?
Join Date: Aug 2003
Location: Sale, Australia
Age: 80
Posts: 3,832
Likes: 0
Received 0 Likes
on
0 Posts
Chris, since you mention "meshing" assume you are talking of the inertia starters (lovely sound) and your memory does not fail you. Checklist for the R-1830 with inertia starters called for,
Ignition Switches ON
Energise Starter - "START" position for 10 to 15 seconds
When starter is energised, engage the starter - "MESH" position and simultaneously actuate primer until engine is running on the primer.
NB: On this particular aircraft the props were pulled through 15 blades by hand if shutdown had been greater than 30 minutes so there was no counting blades on engaging "MESH".
Another aircraft calls for engaging "MESH", let the prop make one revolution, Ignition ON, actuate primer etc etc. Prior to start pull engine through two complete revolutions. So seems more than one method of skinning the cat was employed.
The R-1820 with Bendix type starter called for starter engage, count at least eight blades (3 blade prop), ignition ON, depress primer etc etc. At least on the checklist I have.
Ignition Switches ON
Energise Starter - "START" position for 10 to 15 seconds
When starter is energised, engage the starter - "MESH" position and simultaneously actuate primer until engine is running on the primer.
NB: On this particular aircraft the props were pulled through 15 blades by hand if shutdown had been greater than 30 minutes so there was no counting blades on engaging "MESH".
Another aircraft calls for engaging "MESH", let the prop make one revolution, Ignition ON, actuate primer etc etc. Prior to start pull engine through two complete revolutions. So seems more than one method of skinning the cat was employed.
The R-1820 with Bendix type starter called for starter engage, count at least eight blades (3 blade prop), ignition ON, depress primer etc etc. At least on the checklist I have.
Last edited by Brian Abraham; 26th Mar 2010 at 05:05.
I recall my first start in a Sea Fury. All I had to go on was the Pilots Notes and a Sub Lieutenant standing on the wing telling me what to do. After doing whatever I was supposed to do, I pressed the start button which activated a cartridge and a big whoosh and lots of smoke happened and the prop spun a few times and stopped. A naval airmen jumped like Tarzan on to the starboard wing via the wheel (an Olympic feat if ever I saw one) and with a large rubber mallet bashed the side of the engine cowl a few inches from my face. Apparently that freed up a solenoid or somefink.
Went through the same process and selected another cartridge but same result with lots of sooty smoke which impinged on the Sub Lieut perched on the port wing root giving me "advice". Prop spun and lots more smoke but still the engine did not start.
"What the f..k is wrong now" said the chap bending over into the cockpit? I looked around and saw the magneto switch was still off. Said sorry, Sir, but mag switch was off. Chap bending over cockpit mightily unimpressed and gave me the death glare. Snobbish type. Probably because I was a RAAF Sergeant Pilot instead of a Navy pilot.
Selected third cartridge and mag switch to on and tried again. The engine started this time and the prop slipstream nearly blew the Sub Lieutenant off the wing. He walked away in disgust. Nice aircraft to fly though - although the landing was a shocker.
Went through the same process and selected another cartridge but same result with lots of sooty smoke which impinged on the Sub Lieut perched on the port wing root giving me "advice". Prop spun and lots more smoke but still the engine did not start.
"What the f..k is wrong now" said the chap bending over into the cockpit? I looked around and saw the magneto switch was still off. Said sorry, Sir, but mag switch was off. Chap bending over cockpit mightily unimpressed and gave me the death glare. Snobbish type. Probably because I was a RAAF Sergeant Pilot instead of a Navy pilot.
Selected third cartridge and mag switch to on and tried again. The engine started this time and the prop slipstream nearly blew the Sub Lieutenant off the wing. He walked away in disgust. Nice aircraft to fly though - although the landing was a shocker.
Join Date: Aug 2003
Location: Sale, Australia
Age: 80
Posts: 3,832
Likes: 0
Received 0 Likes
on
0 Posts
Happens to the best Centaurus. On a cross country instrument nav trip as a student we had parked at the finger of a major airport to refuel. Cranking up for departure with muggins in the back seat under the hood and Sir in the front trying to breath life into Mr Wrights finest. Much cranking and nothing happening, pax in the lounge starting to take interest, muggins looks down to see the mags off. What to do? Sir is not in good humour today anyway, does muggins reach down and quietly flip them on, or what, the battery is beginning to display a measure of lethargy? Decisions, decisions. At this point Sir realises problem, turns them on and off we go.
Join Date: Dec 2007
Location: Southeast U K
Posts: 291
Likes: 0
Received 0 Likes
on
0 Posts
Willit Run, You must have been pretty unlucky with your
DC 8 engines if they were less reliable than the piston jobs,
is all I can think.
Never had a great deal of problems with with ours.( JT3's)
Just keep 'em filled up, and they'd run forever.
The Wright Curtiss Cyclones on the Conny, on the other hand,
were bitches.
DC 8 engines if they were less reliable than the piston jobs,
is all I can think.
Never had a great deal of problems with with ours.( JT3's)
Just keep 'em filled up, and they'd run forever.
The Wright Curtiss Cyclones on the Conny, on the other hand,
were bitches.
Join Date: Oct 2008
Location: Mexico
Age: 23
Posts: 12
Likes: 0
Received 0 Likes
on
0 Posts
Big Lycoming Radial
Does anyone remember the big 5,000+ hp Lycoming radial. I can't remember the number designation but it was supposedly the largest radial ever built...but was never built in any big numbers due to some reason or other. Getting old, brain is foggy but I do remember reading about it. Anyone else?

Join Date: Aug 2003
Location: Sale, Australia
Age: 80
Posts: 3,832
Likes: 0
Received 0 Likes
on
0 Posts

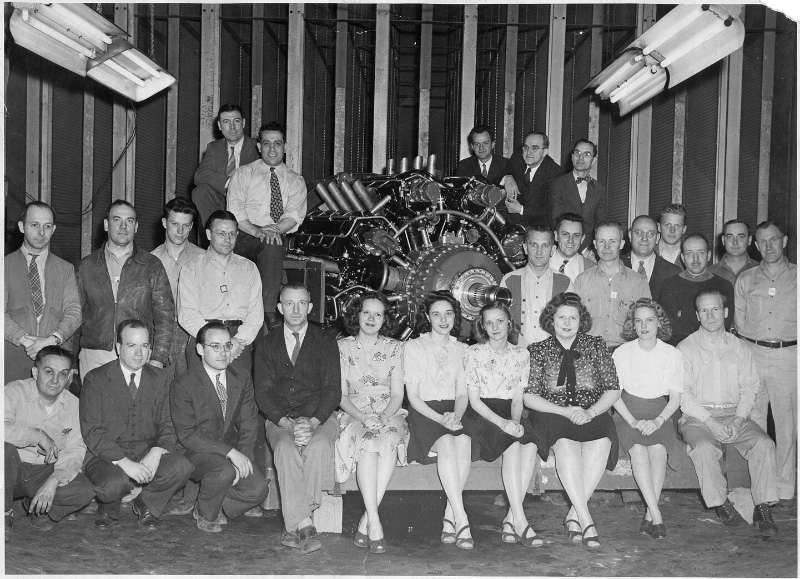
XR-7755 ENGINEERING TEAM are shown with their "baby", the giant 36 cylinder engine. Left to right in the front row are; Boris Osojnak, Tom Kennedy, Otto Shuey, Sam Fry, Robert McElhanny and Don Little. In the second row are Jack Carpenter, John Guibord, Clarence Wiegman, Charlotte Plankenhorn, Roscoe Kendig, Robert Dittmar and Paul M. McBride. In the third row are Hess Wertz, George Love, Bernard Shew, Edgar Demmien, Frank Murray, Leo Aldrich, Fred Jones, Waldo Bird and Jim McRoberts. This photograph was taken November 14, 1945. (Photo: Paul M. McBride)
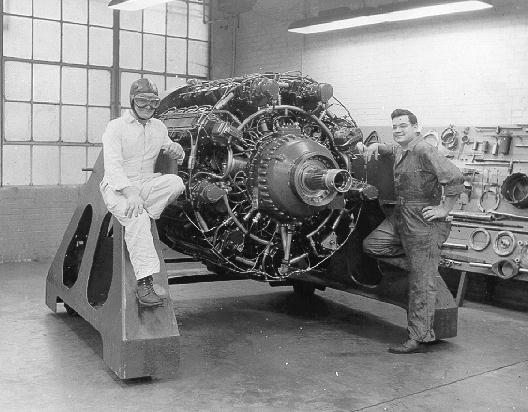
This 36 cylinder engine was destined to be the largest reciprocating engine ever built. The displacement was 7,755 cubic inches. When compared to Lycoming's largest production engine in production today which displaces 720 cubic inches, it was more than 10 times larger!
Development of the XR-7755 began at Lycoming in Williamsport in the summer of 1943. With the end of World War II in 1945, the military no longer had a need for an engine of this size, and development of the XR-7755 stopped at the prototype stage.
During those years, Lycoming put together a team, under the leadership of VP Engineering Clarence Wiegman, to develop this super-size engine.
The resulting design used nine banks of four cylinders arranged around a central crankshaft to form a four-row radial engine. Unlike most multi-row radials, which splay the cylinders to allow cooling air to reach them, the R-7755 was water-cooled and so the cylinder heads were in-line under a cooling jacket. Contrast this with the Junkers Jumo 222, which looked similar from the outside but ran on a V-style cycle instead of a radial. The R-7755 was 10 ft (3 m) long, 5 ft (1.5 m) in diameter, and weighed 6,050 lb (2,740 kg). At full power it was to produce 5,000 hp (3,700 kW) at 2,600 rpm, maintaining that with a turbocharger to a critical altitude of 7,000 feet. It used 580 GPH of avgas at the 5,000 HP rating.
Each cylinder bank had a single overhead cam powering the poppet valves. The camshaft included two sets of cams, one for full takeoff power, and another for economical cruise. The pilot could select between the two settings, which would shift the camshaft along its axis to bring the other set of cams over the valve stems. Interestingly, the design mounted some of the accessories on the "front side" of the camshafts, namely two magnetos and four distributors. The seventh camshaft was not used in this fashion, its location on the front of the engine was used to feed oil to the propeller reduction gearing.
The original XR-7755-1 design drove a single propeller, but even on the largest aircraft the propeller needed to absorb the power would have been ridiculously large. This led to a minor redesign that produced the XR-7755-3, using a new propeller gearing system driving two shafts to power a set of contra-rotating props. The propeller reduction gearing also had two speed settings to allow for a greater range of operating power than adjustable props alone could deliver. Another minor modification resulted in the XR-7755-5, the only change being the replacement of carburetors with a new fuel injection system.
Operational history
The engine first started testing at 5,000 hp (3,700 kW) in 1944 with the XR-7755-3, but demonstrated terrible reliability problems. A second example was provided, as planned, to the United States Army Air Forces at Wright Field in 1946. However, by this time the Air Force had lost interest in new piston designs due to the introduction of jet engines, and the Lycoming delivery team was instructed to simply "dump it on the ground". This engine has since disappeared. The original test engine was later delivered to the Smithsonian Institution, where it was recently restored.
Join Date: Jan 2002
Location: The Far Side
Posts: 297
Likes: 0
Received 0 Likes
on
0 Posts
Going back to the Bristol Hercules. It was a rugged and reliable engine.
BWIA (island hopping in Caribbean-lots of heat humidity and sea blast) had them on their Vickers Vikings in the early fifties.
Before that, they had Lodestars with Pratts. The Vikings were followed by DC-3s with Pratts.
During the Viking era they won the coveted Cumberbatch Trophy for "regularity"
, a feat they never came close to before or after, even with jets, in their 66 year history!
Those Hercules just kept on humming even in relatively primitive conditions.
BWIA (island hopping in Caribbean-lots of heat humidity and sea blast) had them on their Vickers Vikings in the early fifties.
Before that, they had Lodestars with Pratts. The Vikings were followed by DC-3s with Pratts.
During the Viking era they won the coveted Cumberbatch Trophy for "regularity"

Those Hercules just kept on humming even in relatively primitive conditions.
P&W 1830 (Twin Wasp) starting
Quote from Brian Abraham:
"Chris, since you mention "meshing" assume you are talking of the inertia starters (lovely sound) and your memory does not fail you."
Well, it had certainly had on one point: failure to prime the 1830s (dash 92s in our case) at the beginning of the start sequence. Might need some retraining before flying the old Gooney Bird again? My recollection is that it was a one-arm paper-hanging exercise to get them started.
Have lost whatever notes I made in 1967. (We had some highly experienced Dak operators in Morton's.) The 1946 Pilot's Notes for Dakota IV (Dash 90Cs) does not mention any requirement for counting a minimum number of blades before opening the mixture control to AUTO RICH, but I'm reasonably sure that's what we did on the Dash 92 – was it 7 blades (i.e., 2 revs)?
"Chris, since you mention "meshing" assume you are talking of the inertia starters (lovely sound) and your memory does not fail you."
Well, it had certainly had on one point: failure to prime the 1830s (dash 92s in our case) at the beginning of the start sequence. Might need some retraining before flying the old Gooney Bird again? My recollection is that it was a one-arm paper-hanging exercise to get them started.
Have lost whatever notes I made in 1967. (We had some highly experienced Dak operators in Morton's.) The 1946 Pilot's Notes for Dakota IV (Dash 90Cs) does not mention any requirement for counting a minimum number of blades before opening the mixture control to AUTO RICH, but I'm reasonably sure that's what we did on the Dash 92 – was it 7 blades (i.e., 2 revs)?