TAM A320 crash at Congonhas, Brazil
PPRuNe supporter
Join Date: Dec 2003
Location: Planet Earth
Posts: 1,677
Likes: 0
Received 0 Likes
on
0 Posts
On a short slick runway as soon as you touch down you will be in reverse thrust and the go around option is not recommended by Bubbers


Join Date: Jul 2007
Location: Germany
Posts: 556
Likes: 0
Received 0 Likes
on
0 Posts
SIDSTAR,
very well put. I do not necessarily agree, but since I don't fly the machines I will not pass judgment.
(my emphasis)
Couldn't that be a key point? Lack of type-training?
The systems of different aircraft are fundamentally different in this respect (as well as the sidestick vs. conventional yoke respect, the sidestick also having been implicated in at least one accident I am aware of ... )
Even if it is possible that the static lever design has influenced this accident, the case for changing it is a far more compex one. We have seen accidents with similar (though ultimately less fatal) consequences which were in part caused by the back-driving mechanism of the B747-400 thrust levers.
While it is true that no part of a flight deck design can be allowed to be above criticism, a single (or even three) accident cannot be viewed individually to make a case for a fundamental design change. Looking at the balance of moving/non-moving levers in all situations, the score does not look so clear any more.
Add to that Buridan's Ass ("metastability", "undecidability", call it what you will, eloquently introduced here by PBL), and we have to wonder if changing the design here will not simply move the problem to another region.
Bernd
very well put. I do not necessarily agree, but since I don't fly the machines I will not pass judgment.
Having also watched many pilots new to this system, operate the aircraft very poorly in both sim and aircraft,
Couldn't that be a key point? Lack of type-training?
The systems of different aircraft are fundamentally different in this respect (as well as the sidestick vs. conventional yoke respect, the sidestick also having been implicated in at least one accident I am aware of ... )
Even if it is possible that the static lever design has influenced this accident, the case for changing it is a far more compex one. We have seen accidents with similar (though ultimately less fatal) consequences which were in part caused by the back-driving mechanism of the B747-400 thrust levers.
While it is true that no part of a flight deck design can be allowed to be above criticism, a single (or even three) accident cannot be viewed individually to make a case for a fundamental design change. Looking at the balance of moving/non-moving levers in all situations, the score does not look so clear any more.
Add to that Buridan's Ass ("metastability", "undecidability", call it what you will, eloquently introduced here by PBL), and we have to wonder if changing the design here will not simply move the problem to another region.
Bernd

Per Ardua ad Astraeus
Join Date: Mar 2000
Location: UK
Posts: 18,579
Likes: 0
Received 0 Likes
on
0 Posts
Originally Posted by bsieker
Couldn't that be a key point? Lack of type-training?


Join Date: Sep 2000
Location: Bielefeld, Germany
Posts: 955
Likes: 0
Received 0 Likes
on
0 Posts
Originally Posted by SIDSTAR
It is also worth bearing in mind that Airbus and Boeing are not above using forums such as this for their own purposes ...
it is maybe worth inquiring what such purposes would be, and how they could hope to achieve them in this forum.
If anyone helps establish The Truth, then more power to them, whatever the motivation. And if someone wants to spread falsehoods, it's hard for me to see how they would make it past the barrage of criticism.
PBL (NOT affiliated with any big company's marketing department


Join Date: Feb 2007
Location: i don't know
Posts: 320
Likes: 0
Received 0 Likes
on
0 Posts
BOAC
.... basically we will then end up with many more drills the pilots have to recall instantly, under all circumstances, without any doubt about which one to apply, by switching off or on any failing lever, switch, pushbutton, without warnings as the system cannot know it failed, the pilot however has to recognise instantly .......................... to back up failing automatics, programs, designs, you name it.
That's the ultimate perversion to why automation has been brought in! We wanted help in the cockpit and end up beeing a watchdog for brilliant ideas of engineers, not so brilliantly implemented and not adapted to our human skills.
I pledge for the other way. Take out the ambiguous stuff, even if it brings us back a technologie or two, and REDESIGN AUTOMATION where it proved to confuse us. Take the average Joe and Jane to determine this, not the specialists who guide us through the wonders of engineering on pprune.
As has been said, it is not only a AI phenomenon.
The training side/AB may also need to consider a drill for a failed T/L sensor along the lines of the 'failed braking' drill.
That's the ultimate perversion to why automation has been brought in! We wanted help in the cockpit and end up beeing a watchdog for brilliant ideas of engineers, not so brilliantly implemented and not adapted to our human skills.
I pledge for the other way. Take out the ambiguous stuff, even if it brings us back a technologie or two, and REDESIGN AUTOMATION where it proved to confuse us. Take the average Joe and Jane to determine this, not the specialists who guide us through the wonders of engineering on pprune.
As has been said, it is not only a AI phenomenon.

Join Date: Sep 2000
Location: Bielefeld, Germany
Posts: 955
Likes: 0
Received 0 Likes
on
0 Posts
Originally Posted by BOAC
The training side/AB may also need to consider a drill for a failed T/L sensor along the lines of the 'failed braking' drill
If the FMEA is done right, I would imagine a failed TLA sensor arrangement is a 10^(-9) item, isn't it?
Originally Posted by GMDS
I pledge for the other way. Take out the ambiguous stuff, even if it brings us back a technologie or two, and REDESIGN AUTOMATION where it proved to confuse us. Take the average Joe and Jane to determine this, not the specialists who guide us through the wonders of engineering on pprune.
It's not as simple as lookit n fixit. If it were, we wouldn't be having this discussion.
PBL

Per Ardua ad Astraeus
Join Date: Mar 2000
Location: UK
Posts: 18,579
Likes: 0
Received 0 Likes
on
0 Posts
Originally Posted by GMDS
basically we will then end up with many more drills the pilots have to recall instantly
Let's suppose it happened at CGH.
a) Were the crew aware of the possibility? - I suggest not
b) would they have known instantly what action was required? - ditto
c) are there any SIGNIFICANT clues, preferably visual (or STRONG audio) to tell crew it has happened? - ditto?
I support GMDS's 'Joe and Jane' approach.

Join Date: Jul 2007
Location: Germany
Posts: 556
Likes: 0
Received 0 Likes
on
0 Posts
Originally Posted by BOAC
- from my limited understanding of the way the beast works, it seems that a failure of the sensors would be very difficult to detect and therefore IF it is a possibility inside the 'automation' it needs to be thought of.
THR LEVER FAULT: no reliable reading
THR LEVER DISAGREE: different readings from both sensors.
[Edit: corrected procedure description]
The handling is only slightly different, but TOGA/FLEX thrust during take-off/go-around will be maintained. In other situations, IDLE, MCT, or thrust according/limited to the higher reading in case of "disagree" will be set, according to various circumstances (speed, flight phase, slat position, TLA at failure ...).
Standard procedure is to set the lever of the affected engine to IDLE, and, if possible, keep autothrust on.
[/Edit]
There may be some mechanical failures (namely failure of the pushrod between artificial-feel unit and throttle control unit, which incorporates the sensors) that are hard to detect, but since these are mechanical parts, making them highly reliable is well-understood, and barring maintenance problems a failure seems unlikely.
Then again, a failure of the slat-track downstop on B737NG was also considered very unlikely, ...
(See this thread for reference.)
Bernd
Last edited by bsieker; 9th Sep 2007 at 13:51. Reason: Corrected SOPs.

Per Ardua ad Astraeus
Join Date: Mar 2000
Location: UK
Posts: 18,579
Likes: 0
Received 0 Likes
on
0 Posts
according to various circumstances

I've read through this whole discussion and it's been extremely interesting. What no-one seems to have adequately answered is why a system's logic should allow the selection (not unwanted deployment through failure) of reverse thrust on one engine with significant commanded forward thrust on the other. I've spent some time thinking about it and cannot see a situation where this wouldn't lead to severe/terminal handling difficulties, both on the ground and in the air.
Just to re-iterate: I can see that for a non-normal situation like uncommanded T/R deployment in the air, you might want to have the ability to add thrust on the other engine. What I can't envisage is the need to select reverse on one having selected >idle forward thrust on the other - to my mind this just shouldn't be an available option as it will always be a bad one...
Comments?
Just to re-iterate: I can see that for a non-normal situation like uncommanded T/R deployment in the air, you might want to have the ability to add thrust on the other engine. What I can't envisage is the need to select reverse on one having selected >idle forward thrust on the other - to my mind this just shouldn't be an available option as it will always be a bad one...


Paxing All Over The World
SIDSTAR
The world moves by cøck-up, not by conspiracy. If a manufacturer wanted to influence matters in a malign way, they have all the money and advisors and politicians that they need.
It is also worth bearing in mind that Airbus and Boeing are not above using forums such as this for their own purposes ...


Join Date: Jul 2007
Location: Germany
Posts: 556
Likes: 0
Received 0 Likes
on
0 Posts
Quote:
I'll give it a try. Here we go.
. THR LEVER DISAGREE (this warning is inhibited between touchdown and 80kts, i. e. for entire "roll-out" in this accident):
- Before slats extension, TLA at or below MCT during failure:
-- with A/THR ON
===> A/THR active, limited to higher TLA reading, but max MCT.
-- with A/THR OFF
===> Thrust set to higher TLA reading, limited to MCT.
- After slats extension, TLA at or below MCT during failure:
===> IDLE.
- on the ground
===> IDLE, reverse is available.
. THR LEVER FAULT (this warning is not inhibited during approach and landing):
- Before slats extension, TLA at or below MCT during failure:
-- with A/THR ON
===> A/THR active, limited to MCT
-- with A/THR OFF
===> MCT
- After slats extension, TLA at or below MCT during failure:
===> IDLE
on the ground
===> IDLE, reverse is not available, deployed reverser will be restowed.
I hope I got it all right.
Bernd
[setting of thrust at thrust lever angle sensor failure] according to various circumstances
Originally Posted by BOAC
- do you know how it would have 'reverted' in this case, bearing in mind it could have failed at any time from clean up out of previous to landing at CGH and the pilots would not know until....?
. THR LEVER DISAGREE (this warning is inhibited between touchdown and 80kts, i. e. for entire "roll-out" in this accident):
- Before slats extension, TLA at or below MCT during failure:
-- with A/THR ON
===> A/THR active, limited to higher TLA reading, but max MCT.
-- with A/THR OFF
===> Thrust set to higher TLA reading, limited to MCT.
- After slats extension, TLA at or below MCT during failure:
===> IDLE.
- on the ground
===> IDLE, reverse is available.
. THR LEVER FAULT (this warning is not inhibited during approach and landing):
- Before slats extension, TLA at or below MCT during failure:
-- with A/THR ON
===> A/THR active, limited to MCT
-- with A/THR OFF
===> MCT
- After slats extension, TLA at or below MCT during failure:
===> IDLE
on the ground
===> IDLE, reverse is not available, deployed reverser will be restowed.
I hope I got it all right.
Bernd

Per Ardua ad Astraeus
Join Date: Mar 2000
Location: UK
Posts: 18,579
Likes: 0
Received 0 Likes
on
0 Posts
Thanks Bernd - so are you saying that unless the 'pushrod' failed at touchdown there would have been a recorded indication (somewhere?) of a disagreement between the two position sensors on the No 2 T/L? Where would the disagree signal be recorded?
So, as I read you, ?in the absence of such?, it really focusses on pilot mis-positioning of the lever - or an unlikely failure of the 'pushrod' as the T/L No2 was closed.
So, as I read you, ?in the absence of such?, it really focusses on pilot mis-positioning of the lever - or an unlikely failure of the 'pushrod' as the T/L No2 was closed.

Join Date: Jul 2007
Location: Germany
Posts: 556
Likes: 0
Received 0 Likes
on
0 Posts
Thanks Bernd - so are you saying that unless the 'pushrod' failed at touchdown there would have been a recorded indication (somewhere?) of a disagreement between the two position sensors on the No 2 T/L? Where would the disagree signal be recorded?
Since Autothrust remained active, either failure described above would not have made a difference until Autothrust-disconnect. But a deteced failure, as described above, would have put the affected engine to IDLE after Autothrust disconnect, which did not happen.
So, as I read you, ?in the absence of such?, it really focusses on pilot mis-positioning of the lever - or an unlikely failure of the 'pushrod' as the T/L No2 was closed.
This is speculative, but I guess that even after the fire, the experts (the real ones conducting the hands-on-work of the investigation) will be able to tell if and in which way the thrust lever mechanics may have failed.
If there had been an indication of such a failure, there would have been an all-operators telex and/or service bulletin and/or an emergency AD, as has been the case in the China Airlines fire in Okinawa.
That there wasn't is a strong indication that there was nothing wrong mechanically with the throttle system.
... Leaving only an undetected electronics failure. Very remote, but we never said it was absolutely impossible.
Bernd

Paxing All Over The World
With the resurgent interest in the TLs and their possible failure. I checked back to see where the electronic explanation was given. There are more posts, as well as the diagrams of the physical layout but this is about the electronic layout. To the outsider (me) who spent 25 years in IT, this looks like they have covered the eventuality of mechanical failure and ensured that it can be picked up by electronic means, which are themselves heavily duplicated.
TyroPicard #884
TripleBravo #1474
vapilot2004 #1510
TyroPicard #884
There are two Angle sensors on each Thrust Lever. If the two sensors disagree about the TLA, on the ground, but not at TOGA or FLX/MCT (i.e. take-off thrust setting), the FADEC selects Idle thrust irrespective of thrust lever position. An ECAM warning occurs and as part of the drill the pilot backs this up by selecting idle.
If neither sensor produces a valid signal, on the ground, the FADEC selects Idle thrust. An ECAM etc......
If neither sensor produces a valid signal, on the ground, the FADEC selects Idle thrust. An ECAM etc......
The position information is transmitted by 6 cables per sensor, which allow to cross-check for cable breaks and potentiometer breakups for each sensor. These analog signals are fed into one channel of FADEC (A), the other 6 from the second sensor are treated completely separate in channel B. The arbitration between the two FADEC channels takes place after input check and evaluation of the signals. Each channel is capable to control the engine on its own if the other fails. They are independent, also physically, which means that every chip is only responsible for one of the two channels.
Once again, this is no cheapo hardware like just one microcontroller doing all the math, so there is no need for such constructions like IRQs.
The engineering is well aware of the importance of treating these things right. Also the test departments are very creative inventing scenarios the engineering departments might have overlooked, kind of competition. Trust me, I have worked in that business, although not especially on thrust levers and engines.
Once again, this is no cheapo hardware like just one microcontroller doing all the math, so there is no need for such constructions like IRQs.
The engineering is well aware of the importance of treating these things right. Also the test departments are very creative inventing scenarios the engineering departments might have overlooked, kind of competition. Trust me, I have worked in that business, although not especially on thrust levers and engines.
Airbus thrust lever description
The mechanical thrust controls for the A320 consists of three main parts:
The Levers,artificial feel units and control units.
This setup is common for most FADEC equipped aircraft with the only difference between Airbus A320/330/340 and others is the addition of a servo motor to back drive the throttle levers in autothrust mode.
Each thrust lever is connected by a pushrod to the input of an artificial feel unit. This unit provides friction and the detents throughout the motion of the thrust levers.
The artificial feel unit's output shaft is connected to the thrust control unit via a second pushrod. Within each thrust control unit are 6 potentiometers and 2 thrust angle resolvers.
The pots provide thrust lever position to the flight control system while the resolvers are dedicated to the engine thrust control.
A resolver is a sort of rotary transformer that outputs sine & cosine waves corresponding the the thrust lever angle. The mechanical ratio of the thrust lever angle and the resolver angle is 1:1.9. For every degree of movement of the levers, there is a 1.9 degree movement indicated by the resolver. Resolver units are more accurate and reliable in translating angular position data than potentiometers and is the reason for their use here.
Each thrust control unit has two resolvers - one for each EEC channel. A disagreement of more than 15' (1/4 degree) causes the EEC to go into resolver failure mode.
Each EEC also checks the resolver output for upper and lower limits. For the IAE engines the limits are from -41 to 88 degrees. Any value outside of these limits will cause the FADEC system to transfer engine thrust control to the alternate EEC.
Outside of a jammed feel unit or thrust control unit, a failure of the A320 manual thrust control system seems unlikely.
The mechanical thrust controls for the A320 consists of three main parts:
The Levers,artificial feel units and control units.
This setup is common for most FADEC equipped aircraft with the only difference between Airbus A320/330/340 and others is the addition of a servo motor to back drive the throttle levers in autothrust mode.
Each thrust lever is connected by a pushrod to the input of an artificial feel unit. This unit provides friction and the detents throughout the motion of the thrust levers.
The artificial feel unit's output shaft is connected to the thrust control unit via a second pushrod. Within each thrust control unit are 6 potentiometers and 2 thrust angle resolvers.
The pots provide thrust lever position to the flight control system while the resolvers are dedicated to the engine thrust control.
A resolver is a sort of rotary transformer that outputs sine & cosine waves corresponding the the thrust lever angle. The mechanical ratio of the thrust lever angle and the resolver angle is 1:1.9. For every degree of movement of the levers, there is a 1.9 degree movement indicated by the resolver. Resolver units are more accurate and reliable in translating angular position data than potentiometers and is the reason for their use here.
Each thrust control unit has two resolvers - one for each EEC channel. A disagreement of more than 15' (1/4 degree) causes the EEC to go into resolver failure mode.
Each EEC also checks the resolver output for upper and lower limits. For the IAE engines the limits are from -41 to 88 degrees. Any value outside of these limits will cause the FADEC system to transfer engine thrust control to the alternate EEC.
Outside of a jammed feel unit or thrust control unit, a failure of the A320 manual thrust control system seems unlikely.

Join Date: Aug 2005
Location: fl
Posts: 2,525
Likes: 0
Received 0 Likes
on
0 Posts
Quote:
On a short slick runway as soon as you touch down you will be in reverse thrust and the go around option is not recommended by Bubbers
Please don't put everyone in this category, this would not be my technique, I choose to keep my options open.
Options open means you want to be able to go around without coming out of reverse first which can easily be done but is not recommended by sop. How far with your procedure of landing on a short slick runway do you travel before you select reverse thrust? How much does that extend your landing distance? Most airplanes, you know the ground spoilers will work so if you fly that airplane you can always get ground spoilers so there isn't any reason to wait for ground spoilers to deploy before commiting to a landing. If you fly an airplane that you don't know if you can get ground spoilers I see your point.
On a short slick runway as soon as you touch down you will be in reverse thrust and the go around option is not recommended by Bubbers
Please don't put everyone in this category, this would not be my technique, I choose to keep my options open.
Options open means you want to be able to go around without coming out of reverse first which can easily be done but is not recommended by sop. How far with your procedure of landing on a short slick runway do you travel before you select reverse thrust? How much does that extend your landing distance? Most airplanes, you know the ground spoilers will work so if you fly that airplane you can always get ground spoilers so there isn't any reason to wait for ground spoilers to deploy before commiting to a landing. If you fly an airplane that you don't know if you can get ground spoilers I see your point.

I support PPRuNe
Join Date: Jul 2007
Location: Belo Horizonte, Brazil
Posts: 162
Likes: 0
Received 0 Likes
on
0 Posts
From a Brazilian Pilot Site
From a talented Brazilian Jet Pilot (http://aviationtroubleshooting.*************/
Sábado, 1 de Setembro de 2007
TAM 3054 - Aceleração BRUSCA antes do pouso
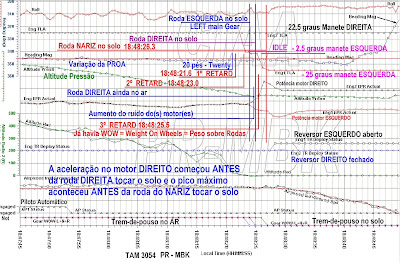
A aceleração do motor DIREITO, cujo reversor estava 'pinado', começou ANTES das rodas do Trem-de-pouso DIREITO e NARIZ terem tocado o solo.
The acceleration of the RIGHT motor, where the reverser was locked out, started BEFORE the RIGHT and NOSE wheels touched the ground.
Na imagem acima apresenta o detalhamento na linha do tempo sobre o fato da aceleração ter se iniciado num momento inconveniente.
In the above graphic one can see the details of the libe of time about the fact that the acceleration having started at an incovenient moment,
Não foi uma aceleração típica de correção de potência dos motores e sim uma BRUSCA aceleração que atingiu o pico em 3.5 segundos subindo a EPR do motor DIREITO para 1,260.
It was not a typical acceleration for the correction of the potency of the motors, instead it was a sudden acceleration that reached the peak in 3.5 seconds raising the EPR of the RIGHT motor to 1,260.
Esta observação já foi postada neste Blog, mas alguns internautas não entenderam.
I already posted this observation in this Blog but some internauts did not understand.
É injustificável um sistema de automatização acelerar vertiginosamente a potência de um dos motores, ANTES da aeronave estar com as 3 (três) rodas do Trem-de-pouso no solo, a menos que uma arremetida tenha sido executada.
One can´t justify a system of automatization accelerating dramatically the potency of one of the motors, BEFORE the airplane have the three
(3) wheels on the ground, unless a go around has been executed.
Observe no gráfico que o terceiro alerta, RETARD, aconteceu quando as rodas principais, Esquerda e Direita, do Trem-de-pouso já estavam no solo, porém a roda do NARIZ ainda estava no ar.
Observe in record that the thirs alarm, Retard, happened when the LEFT and RIGHT wheels where on the ground but the NOSE wheel was yet on the air.
O anúncio RETARD foi silenciado devido ter sido selecionado o reversor ESQUERDO na posição angular de -2.5 graus (menos dois decimal cinco).
The warning RETARD became silent because the LEFT reverser was selected in the angulkar position -2.5 degrees (less two decimal five)
Sorry for the translation. My impression is that George Rocha, this talented Jet pilot feels that the software did not work very well because even eith the LEFT motor reversed and the pilot aplying brakes, it still behaved as if the plane wanted to go around (I am just trying without knowing for sure if this is his thinking. I am not a jet pilot, much less a
Airbus or Boeing pro pilot. I just love aviation and my experiences have been with small planes. Just trying to help).
Sábado, 1 de Setembro de 2007
TAM 3054 - Aceleração BRUSCA antes do pouso
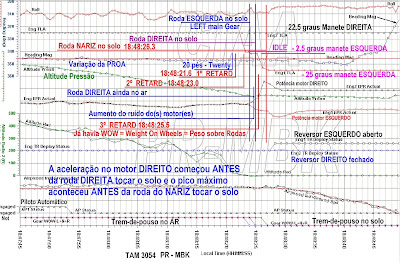
A aceleração do motor DIREITO, cujo reversor estava 'pinado', começou ANTES das rodas do Trem-de-pouso DIREITO e NARIZ terem tocado o solo.
The acceleration of the RIGHT motor, where the reverser was locked out, started BEFORE the RIGHT and NOSE wheels touched the ground.
Na imagem acima apresenta o detalhamento na linha do tempo sobre o fato da aceleração ter se iniciado num momento inconveniente.
In the above graphic one can see the details of the libe of time about the fact that the acceleration having started at an incovenient moment,
Não foi uma aceleração típica de correção de potência dos motores e sim uma BRUSCA aceleração que atingiu o pico em 3.5 segundos subindo a EPR do motor DIREITO para 1,260.
It was not a typical acceleration for the correction of the potency of the motors, instead it was a sudden acceleration that reached the peak in 3.5 seconds raising the EPR of the RIGHT motor to 1,260.
Esta observação já foi postada neste Blog, mas alguns internautas não entenderam.
I already posted this observation in this Blog but some internauts did not understand.
É injustificável um sistema de automatização acelerar vertiginosamente a potência de um dos motores, ANTES da aeronave estar com as 3 (três) rodas do Trem-de-pouso no solo, a menos que uma arremetida tenha sido executada.
One can´t justify a system of automatization accelerating dramatically the potency of one of the motors, BEFORE the airplane have the three
(3) wheels on the ground, unless a go around has been executed.
Observe no gráfico que o terceiro alerta, RETARD, aconteceu quando as rodas principais, Esquerda e Direita, do Trem-de-pouso já estavam no solo, porém a roda do NARIZ ainda estava no ar.
Observe in record that the thirs alarm, Retard, happened when the LEFT and RIGHT wheels where on the ground but the NOSE wheel was yet on the air.
O anúncio RETARD foi silenciado devido ter sido selecionado o reversor ESQUERDO na posição angular de -2.5 graus (menos dois decimal cinco).
The warning RETARD became silent because the LEFT reverser was selected in the angulkar position -2.5 degrees (less two decimal five)
Sorry for the translation. My impression is that George Rocha, this talented Jet pilot feels that the software did not work very well because even eith the LEFT motor reversed and the pilot aplying brakes, it still behaved as if the plane wanted to go around (I am just trying without knowing for sure if this is his thinking. I am not a jet pilot, much less a
Airbus or Boeing pro pilot. I just love aviation and my experiences have been with small planes. Just trying to help).

Join Date: Sep 2000
Location: Bielefeld, Germany
Posts: 955
Likes: 0
Received 0 Likes
on
0 Posts
Originally Posted by marciovp, quoting George Rochas
A aceleração do motor DIREITO, cujo reversor estava 'pinado', começou ANTES das rodas do Trem-de-pouso DIREITO e NARIZ terem tocado o solo.
The acceleration of the RIGHT motor, where the reverser was locked out, started BEFORE the RIGHT and NOSE wheels touched the ground.
The acceleration of the RIGHT motor, where the reverser was locked out, started BEFORE the RIGHT and NOSE wheels touched the ground.
EPR is sampled on the #1 roughly on the full-second boundary; #2 EPR is sampled slightly before the 1/2-second boundary. WoW LMLG occurs between 18:48:23 and :24; WoW RMLG between 18:48:24 and :25. The first *slight* divergence between EPRs occurs between the #1 sample at 18:48:24 and the #2 sample at 18:48:24+.
I would incline more towards the conclusion that WoW RMLG occurred just past the 18:48:24 second boundary, and the EPRs started to diverge after that.
PBL

PPRuNe supporter
Join Date: Dec 2003
Location: Planet Earth
Posts: 1,677
Likes: 0
Received 0 Likes
on
0 Posts
How far with your procedure of landing on a short slick runway do you travel before you select reverse thrust? by bubbers44

Join Date: Sep 2007
Location: Melbourne
Posts: 180
Likes: 0
Received 0 Likes
on
0 Posts
I’ve followed this thread from the beginning with great interest, and learned a lot from it. But (being only a GA and glider pilot, and retired at that) I’ve only just plucked up courage to mention something that I’ve been wondering about, which so far doesn’t appear to have been discussed.
Most people will have seen this video of a (highly-competent, ‘textbook’) A320 landing at Madeira. It’s unusually informative because the camera guy, instead of just filming straight ahead during the touchdown, filmed the pilot’s hand retarding the throttle levers and then applying reverse thrust.
http://www.youtube.com/watch?v=3OtcaFkpUpk
It shows that the pilot’s grip on the handles looks slightly odd – only the forefinger is actually hooked over the levers, the thumb and middle finger are gripping the sides of the levers. I researched this a bit and found that there are in fact red buttons on the outside of each lever, which trigger ‘autothrust disconnect.’ That is presumably the reason for the odd grip, so that the pilot could disconnect the autothrust before flaring – even though he would have been planning to pull the levers back to ‘idle’ in any case.
From information earlier in the thread, we all know that, with the A320 setup, autothrust disconnect does not automatically reduce engine thrust to ‘idle.’ If the throttles are above ‘idle’ the thrust merely ‘defaults’ to the last recorded thrust setting (which in this case was presumably the power required to maintain landing speed on final approach). So, as I see it, even if the wheels are down, the ONLY way to reduce thrust on a given engine to ‘idle,’ and keep it there, is to retard the lever all the way to the ‘idle’ stop?
Is it even barely possibly that the pilot at CGH didn’t know this, or didn’t recall the point under the pressures of landing on a short wet runway with only one operating reverser? And therefore, in his own mind, used the buttons to order ‘autothrust disconnect’ and then interpreted that as ‘finished with engines,’ and concentrated only on making sure that he got hold of the correct lever for the operating reverser and moved it into ‘max. reverse’ as soon as possible?
Thought I’d ask the question, anyway. If I’m talking rubbish, don’t hesitate to say so and I’ll shut up.
Most people will have seen this video of a (highly-competent, ‘textbook’) A320 landing at Madeira. It’s unusually informative because the camera guy, instead of just filming straight ahead during the touchdown, filmed the pilot’s hand retarding the throttle levers and then applying reverse thrust.
http://www.youtube.com/watch?v=3OtcaFkpUpk
It shows that the pilot’s grip on the handles looks slightly odd – only the forefinger is actually hooked over the levers, the thumb and middle finger are gripping the sides of the levers. I researched this a bit and found that there are in fact red buttons on the outside of each lever, which trigger ‘autothrust disconnect.’ That is presumably the reason for the odd grip, so that the pilot could disconnect the autothrust before flaring – even though he would have been planning to pull the levers back to ‘idle’ in any case.
From information earlier in the thread, we all know that, with the A320 setup, autothrust disconnect does not automatically reduce engine thrust to ‘idle.’ If the throttles are above ‘idle’ the thrust merely ‘defaults’ to the last recorded thrust setting (which in this case was presumably the power required to maintain landing speed on final approach). So, as I see it, even if the wheels are down, the ONLY way to reduce thrust on a given engine to ‘idle,’ and keep it there, is to retard the lever all the way to the ‘idle’ stop?
Is it even barely possibly that the pilot at CGH didn’t know this, or didn’t recall the point under the pressures of landing on a short wet runway with only one operating reverser? And therefore, in his own mind, used the buttons to order ‘autothrust disconnect’ and then interpreted that as ‘finished with engines,’ and concentrated only on making sure that he got hold of the correct lever for the operating reverser and moved it into ‘max. reverse’ as soon as possible?
Thought I’d ask the question, anyway. If I’m talking rubbish, don’t hesitate to say so and I’ll shut up.
