Tristar L-1011 FMS & Autopilot
Join Date: Jan 2006
Location: Georgia, USA
Posts: 454
Likes: 0
Received 0 Likes
on
0 Posts
An interesting variation on a theme is that the HS Trident, unlike its 727 look-alike, used the whole tailplane for pitch control I have seen pics of it fully deployed at rotation. Ditto for the VC-10 .
So in this sense tailplane use was similar to that of the TriStar.
So in this sense tailplane use was similar to that of the TriStar.
The L-1011 also trims the horizontal stabilizer nose down for takeoff, but instead of a ballscrew the L-1011 uses four hydraulic actuators.
The main difference between the two systems is: when the L-1011 reaches takeoff speed and the pilot pulls back on the control column the entire horizontal stabilizer moves even further down to allow the aircraft to rotate. On all the other aircraft when takeoff speed is reached and the pilot pulls back on the control column (or side stick) only the elevators move to allow the aircraft to rotate, the horizontal stabilized stays in the trimed position.
After takeoff the horizontal stabilizer in then repositioned, either by the ballscrews or the actuators, to a neutral position. However, on the L-1011 the entire horizontal stabilizer contines to be used for pitch control while all others use the elevators.
Thread Starter
Join Date: Nov 2008
Location: The New Forest, UK
Posts: 228
Likes: 0
Received 0 Likes
on
0 Posts
411A/glhcarl
the comparison with other a/c was useful thanks.
The pics I referred to are in Davis' "Handing the Big Jets" which shows the HS fully deployed on both the VC10 and Trident. I haven't the book with me now to double check but I thought one photo showed the HS fully nose down during what looks like a TO rotation. Might be a red herring though.
the comparison with other a/c was useful thanks.
The pics I referred to are in Davis' "Handing the Big Jets" which shows the HS fully deployed on both the VC10 and Trident. I haven't the book with me now to double check but I thought one photo showed the HS fully nose down during what looks like a TO rotation. Might be a red herring though.
Join Date: Jan 2006
Location: Georgia, USA
Posts: 454
Likes: 0
Received 0 Likes
on
0 Posts
I thought one photo showed the HS fully nose down during what looks like a TO rotation.
Thread Starter
Join Date: Nov 2008
Location: The New Forest, UK
Posts: 228
Likes: 0
Received 0 Likes
on
0 Posts
If trim setting corrects for loading CoG position then once set one would think it would stay there until the plane is retrimmed during flight. In what way is the trim system involved at takeoff? (Unless of course the CoG was so bad that it did require a full stabiliser nose down for correct trim leaving little margin for comfort)

Join Date: Jul 1999
Location: 58-33N. 00-18W. Peterborough UK
Posts: 3,040
Likes: 0
Received 0 Likes
on
0 Posts
The pics I referred to are in Davis' "Handing the Big Jets" which shows the HS fully deployed on both the VC10 and Trident. ...... I thought one photo showed the HS fully nose down during what looks like a TO rotation.
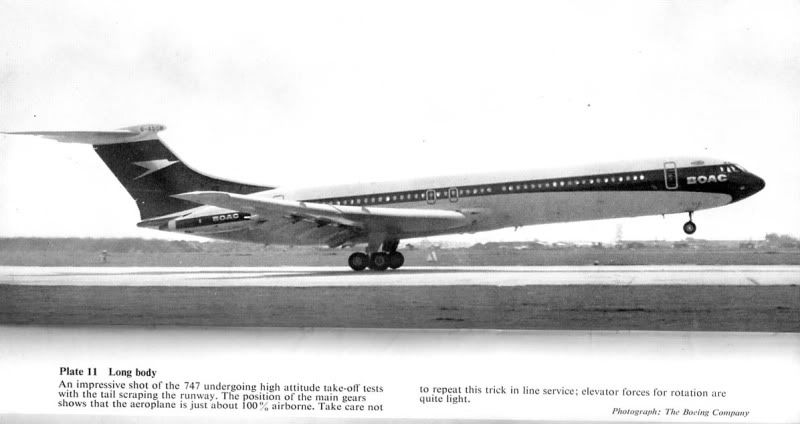
Join Date: Apr 2005
Location: Stockholm Sweden
Age: 74
Posts: 569
Likes: 0
Received 0 Likes
on
0 Posts
Lot of comments in here about the high maint load on the Tristar.
I was there at the start of BA service. When the Tristars were introduced at LHR, the engineers refused to work it. So the turnrounds at LHR were performed by management, and the maint was done on the line, mainly CDG and AMS. The aircraft kept flying. Being used to the Trident it was amazing how the (new) Tristars just kept on going. I was an apprentice, but got involved when we were sent off to AMS to change the first Nbr 2 engine. 3 Line trainers, 6 ex apprentices, and 6 Gulf Air engineers on OJT used the fly away nbr 2 engine staging for the first time in KLM's hangar and changed the engine in two days.
two years later I was in BAH with Gulf Air's brand new L1011s. They also kept flying. It was amazing how well developed the MEL was and how it kept the aircraft out of the hangar. But there we were comparing them to the BAC111s!!
I think that now people are compring them to new modern aircraft, and yes they were not that reliable, but compared to the aircraft in service in 1976, they were good.
I was there at the start of BA service. When the Tristars were introduced at LHR, the engineers refused to work it. So the turnrounds at LHR were performed by management, and the maint was done on the line, mainly CDG and AMS. The aircraft kept flying. Being used to the Trident it was amazing how the (new) Tristars just kept on going. I was an apprentice, but got involved when we were sent off to AMS to change the first Nbr 2 engine. 3 Line trainers, 6 ex apprentices, and 6 Gulf Air engineers on OJT used the fly away nbr 2 engine staging for the first time in KLM's hangar and changed the engine in two days.
two years later I was in BAH with Gulf Air's brand new L1011s. They also kept flying. It was amazing how well developed the MEL was and how it kept the aircraft out of the hangar. But there we were comparing them to the BAC111s!!
I think that now people are compring them to new modern aircraft, and yes they were not that reliable, but compared to the aircraft in service in 1976, they were good.
Join Date: Mar 2000
Location: Arizona USA
Posts: 8,571
Likes: 0
Received 0 Likes
on
0 Posts
**In what way is the trim system involved at takeoff?**
Same as on other jet transports.
The stab is set at xxx units, according to the trim sheet.
Re-trimming is then used after takeoff, normally for acceleration after flaps are set to 4 degrees.
Same as on other jet transports.
The stab is set at xxx units, according to the trim sheet.
Re-trimming is then used after takeoff, normally for acceleration after flaps are set to 4 degrees.
Join Date: Sep 2007
Location: Greensboro, NC USA
Posts: 58
Likes: 0
Received 0 Likes
on
0 Posts
Early delivery's versus later ones
There were a lot of improvements made in the equipment, workmanship and engines over the course of the L-1011's delivery schedule. I was in Palmdale in the first maintenance training class (1972) and was not happy with the wiring standards I saw. Whole looms were built up in the shop and then placed in the aircraft where the unpinned ends ends cascaded down in the cockpit and FESC like a waterfall. Techies sat there with prints and combing thru the wires looking for a particular number. When found it was trimmed to length and a terminal was installed and it was plugged into the Burndy block, hopefully into the right hole. The checkout was made with the Ditmico testing machine and there were a lot of faults found, in the thousands on the very early ones. Around airframe 1012 they got it under better control and then went to a still higher standard later. We had lots of problems for years with the earlier models with miswiring.
The 22C model RB-211 on the first deliveries were derated and did pretty well. With the 22B models we had first the fan disk failures due to titanium problems requiring us to change them at short life cycles. Then the lack of a stall margin bit us. Pilots logged a lot of two engine time as engines stalled and blew out their compressors and turbines. Tailpipes were full of blades and bits. EAL had a rampful of gliders at one point. They instituted a mandatory warmup prior to takeoff, requiring three minutes at pretty high power prior to applying takeoff power. Mods alleviated the problems considerably after several years of suffering. Still later of course the failures and fires in the #1 bearing hit. I'll never forget viewing the aircraft where the #2 fan came loose and walked forward to near the rear pressure bulkhead before flying apart. Required mods to install a "fan-grabber' and later on the bearing locator warning system modification that essentially killed the -22B.
The -22B starting problems were very bad too. I had the EAL mgr of RB211 engineering up in Toronto one very cold day and we timed out engines that took on average five minutes each to get to idle. The worst took a whole seven minutes. In the AM we looked out the window as an EAL L-1011 and a AAL DC-10 both started up for departure. The L1011 fogged the whole ramp while the DC10 started all three, taxied out and took off before EAL got the third started. Rolls couldn't understand it because Air Canada had faster starting. JP-4 fuel explained part of that.
I almost fainted the first time I saw a L-1011 with -524 engines start right up.
The hot stream spoilers (turbine reverser) were a disaster. Ball-nut jackscrews do not live happily near tailpipes and highspeed flex shafts either. When they were deactivated, we had a celebration.
There were the slat/flap assymetry problems, the flap LRS faults, the infamous FECES computer (actually FCES). Kapton wiring, toilet flush computers. Usual Lockheed overdesigns put heater blankets under baggage floors - not a good idea, heaters on the toilet tank outlets - had a fire start there that almost took out the aircraft.
Then there were aircycle machines that made ice down in Florida and San Juan and delivered spouts of icy water from the overhead gasper air outlets. And never forget the master caution and dimming problems. They had a separate conference at Palmdale on just that one area. The MUX system was a disaster for many years. Always thought too that it needed a manual depressurization valve -
Structurally, the worst problem was the rear spar fatigue. We had one that cracked right across the entire web. The earlier aircraft required a major mod in that area. Fuselage was great with its thick skin design. Usual corrosion problems of course.
All that said, the pilots loved it, it flew better than anything they said since the Electra. The DLC system made the airplane look like it was on rails on landing, no bobbing of the nose, steady attitude. If DLC was turned off as one old Captain did, you had to watch for dragging the aft fuselage. He did it requiring major repairs to rear presure bulkhead.
Later on at another outfit operating the only -1 freighter made, we got some -200 pax aircraft from Gulf Air. Wiring problems pretty well gone, engines much better. Still an aircraft that needed experienced techies but manageable. Those that experienced later deliveries reaped the benefits of the early problems. Proves one point, don't fly the "A" model of anything.
The 22C model RB-211 on the first deliveries were derated and did pretty well. With the 22B models we had first the fan disk failures due to titanium problems requiring us to change them at short life cycles. Then the lack of a stall margin bit us. Pilots logged a lot of two engine time as engines stalled and blew out their compressors and turbines. Tailpipes were full of blades and bits. EAL had a rampful of gliders at one point. They instituted a mandatory warmup prior to takeoff, requiring three minutes at pretty high power prior to applying takeoff power. Mods alleviated the problems considerably after several years of suffering. Still later of course the failures and fires in the #1 bearing hit. I'll never forget viewing the aircraft where the #2 fan came loose and walked forward to near the rear pressure bulkhead before flying apart. Required mods to install a "fan-grabber' and later on the bearing locator warning system modification that essentially killed the -22B.
The -22B starting problems were very bad too. I had the EAL mgr of RB211 engineering up in Toronto one very cold day and we timed out engines that took on average five minutes each to get to idle. The worst took a whole seven minutes. In the AM we looked out the window as an EAL L-1011 and a AAL DC-10 both started up for departure. The L1011 fogged the whole ramp while the DC10 started all three, taxied out and took off before EAL got the third started. Rolls couldn't understand it because Air Canada had faster starting. JP-4 fuel explained part of that.
I almost fainted the first time I saw a L-1011 with -524 engines start right up.
The hot stream spoilers (turbine reverser) were a disaster. Ball-nut jackscrews do not live happily near tailpipes and highspeed flex shafts either. When they were deactivated, we had a celebration.
There were the slat/flap assymetry problems, the flap LRS faults, the infamous FECES computer (actually FCES). Kapton wiring, toilet flush computers. Usual Lockheed overdesigns put heater blankets under baggage floors - not a good idea, heaters on the toilet tank outlets - had a fire start there that almost took out the aircraft.
Then there were aircycle machines that made ice down in Florida and San Juan and delivered spouts of icy water from the overhead gasper air outlets. And never forget the master caution and dimming problems. They had a separate conference at Palmdale on just that one area. The MUX system was a disaster for many years. Always thought too that it needed a manual depressurization valve -
Structurally, the worst problem was the rear spar fatigue. We had one that cracked right across the entire web. The earlier aircraft required a major mod in that area. Fuselage was great with its thick skin design. Usual corrosion problems of course.
All that said, the pilots loved it, it flew better than anything they said since the Electra. The DLC system made the airplane look like it was on rails on landing, no bobbing of the nose, steady attitude. If DLC was turned off as one old Captain did, you had to watch for dragging the aft fuselage. He did it requiring major repairs to rear presure bulkhead.
Later on at another outfit operating the only -1 freighter made, we got some -200 pax aircraft from Gulf Air. Wiring problems pretty well gone, engines much better. Still an aircraft that needed experienced techies but manageable. Those that experienced later deliveries reaped the benefits of the early problems. Proves one point, don't fly the "A" model of anything.
Join Date: Dec 2008
Location: Portugal
Posts: 62
Likes: 0
Received 0 Likes
on
0 Posts
Yaw SAS was computed by 3 hydraulic levels: over 1000 PSI, over 2000 PSI and over 3000 PSI. These info were computed by LRS computer, according to flaps/slats, altitude, attitude and speed. Or so the guys that worked it tell me...
Just another input.
Just another input.
Join Date: Jan 2006
Location: Georgia, USA
Posts: 454
Likes: 0
Received 0 Likes
on
0 Posts
Yaw SAS was computed by 3 hydraulic levels: over 1000 PSI, over 2000 PSI and over 3000 PSI. These info were computed by LRS computer, according to flaps/slats, altitude, attitude and speed. Or so the guys that worked it tell me...
Rudder scheduling works as follows:
Below 164 knots the rudder was powered by all three hydraulic systems at 3000 psi each.
Over 164 knots two of the three systems (A and B) were shutoff. System C still supplied 3000 psi.
Above 260 knots the pressure in the one remaining system (system C) was reduced to 2000 psi. Addtionally the L1011-1 had rudder limiter actuators that positioned stops that physically prevented excessive rudder movement above 260 knots.
The above numbers are for the L-1011-1's. L-1011's with higher takeoff weights used the same system but a slightly different speeds and the limiter actuators were removed.
None of this had anything to do with the Yaw SAS system.
Join Date: Dec 2008
Location: Portugal
Posts: 62
Likes: 0
Received 0 Likes
on
0 Posts
Yes I stand corrected. Checked with TAP guys and what happens is I misunderstood their explanation.
Even so, it is a real pleasure see it taking off at LIS, and still one of the best flying aircraft around (when it actually flies).
Even so, it is a real pleasure see it taking off at LIS, and still one of the best flying aircraft around (when it actually flies).
Thread Starter
Join Date: Nov 2008
Location: The New Forest, UK
Posts: 228
Likes: 0
Received 0 Likes
on
0 Posts
411A
you appear to be in desert cemetery country so you could delight us with a few pics of the many dusty L-1011s awaiting aluminiun recyclers?
I have always thought the DC-10 was the better looking of the wide body trijets but there's no denying the technical merits of the 1011 warts and all.
Only flew in it once on a brief flight from Geneva to Gatwick but can not forget the loud clunky undercarriage.
you appear to be in desert cemetery country so you could delight us with a few pics of the many dusty L-1011s awaiting aluminiun recyclers?
I have always thought the DC-10 was the better looking of the wide body trijets but there's no denying the technical merits of the 1011 warts and all.
Only flew in it once on a brief flight from Geneva to Gatwick but can not forget the loud clunky undercarriage.
Join Date: Apr 2005
Location: Stockholm Sweden
Age: 74
Posts: 569
Likes: 0
Received 0 Likes
on
0 Posts
What is a "Frisbee Faring"?
He never lived it down.
Join Date: Nov 2006
Location: world
Posts: 21
Likes: 0
Received 0 Likes
on
0 Posts
Respect the onl lady
Two types of pilots. The ones who had the pleasure to fly them and the ones who did not.
And challenge any of you to compare the so called new acft systems, with the L1011. Can bring the B744 if you want (i fly those ) except EFIS for obvious reasons. But if EFIS is all you got i don't know how to fly. And i'll show you the big dif between a ,YES, old fat lady and a todays model
And challenge any of you to compare the so called new acft systems, with the L1011. Can bring the B744 if you want (i fly those ) except EFIS for obvious reasons. But if EFIS is all you got i don't know how to fly. And i'll show you the big dif between a ,YES, old fat lady and a todays model
Join Date: Jan 2006
Location: Georgia, USA
Posts: 454
Likes: 0
Received 0 Likes
on
0 Posts
The Frisbee rairing replaced a lot of sound deadening lead wool in the upper aft fuselage
The insulation batts were made from spun fiberglass with tedlar covering.
Join Date: Sep 2007
Location: Greensboro, NC USA
Posts: 58
Likes: 0
Received 0 Likes
on
0 Posts
Lead Wool in Aft Fuselage
Sorry but there was lead wool in aft overhead of the early aircraft. I saw them putting it in at Palmdale in 1972 and 1973. Came out later with improvements.
Also, air cycles sounded like muted police sirens in early aircraft. The finally put in tuned mounts for them.
Also, air cycles sounded like muted police sirens in early aircraft. The finally put in tuned mounts for them.