DHC-6 Questions:
Originally Posted by MachTwelve
...the FAA approved MMEL allows flight with the Beta Backup system deactivated, but states that reverse can not be selected. However when reverse is selected by twisiting the power lever grips, it de-activates the beta backup system anyway.
There is a difference between "depowering" the beta backup system in accordance with the MMEL you refer to, and the "disarming" of the beta backup system that takes place during normal operations when you twist the power levers.
The nuance in the wording is this: If there is some form of defect with the beta backup system, the MMEL allows you to dispatch (for a limited number of days) with the system turned off. You accomplish this 'turning off' by pulling the circuit breaker for the system, and once this is done, the system does not function at all. The MMEL refers to this process as 'deactivation', in this context, they mean 'depowering'.
When the beta backup system is operating normally, once you twist the power levers and pull them aft of the idle stop (thus actuating the microswitch above the power levers that detects the grips being twisted), the beta backup system DISARMS for each propeller (individually) the moment that each propeller blade move to a position that is finer than +9° blade angle. Once the system has disarmed for one or both blades, it will not re-arm until the propeller blade moves out of the ground fine range, to a blade angle of +11° or more.
The purpose of the DISARMING (note the difference in wording between 'disarming' and 'deactivation') is to ensure that if the pilot rapidly moves the power levers forward - thus changing the state of the grip switch to indicate that the pilot has no longer selected ground fine range - the beta backup system will not begin to function as the propeller blade moves out of the ground fine range, back towards the idle (or coarser) blade angle position.
Consider this scenario: The pilot lands, then hauls the power levers all the way back to passenger seating row 3. The engines and propellers respond, and the propellers move to the full reverse (-15° blade angle) position. The pilot then rapidly shoves the power levers forward to the idle position, thus releasing the grip switch that indicates to the aircraft that the pilot has commanded ground fine range. The propellers will not move back to +11° as quickly as the pilot can move the power levers forward... there will be a delay of one or two seconds before the propellers move to the idle (+11°) position. If there was no disarming relay, the beta backup system would activate and cycle as the propeller(s) moved forward, because the grip switch would indicate that the grips were not twisted, but the propeller microswitch(s) would still indicate that the propellers were at a blade angle less than +9°.
Hopefully that explains the distinction between 'deactivated' (i.e. circuit breaker pulled) and 'disarmed' (a very specific condition governed by Boolean logic that looks at the sequence of activation of the grip switch and the propeller microswitch(s).
Originally Posted by MachTwelve
...Why can you not select auto-feather prior to descent?
Michael

MachTwelve:
You ask some very reasonable questions. I'm going to try my best to answer them, however, because it is no secret here in the forum where I work or what I do at work, I am going to have to be somewhat circumspect with my reply.
With the system depowered (via the MEL), why can you not select reverse?
I have no answer for that. That particular restriction has been present in the MMEL since before the Old King died. If I was to rewrite the MMEL today, I would not include that restriction. The beta backup system is only depowered (i.e. circuit breaker pulled) when there is a problem with the (electrical) beta backup system... under these conditions the (mechanical) propeller control system is operating normally. Hence, I cannot explain why that requirement to not select reverse is there.
It is possible that the restriction to not select reverse arises as a result of a certification requirement that states that an aircraft equipped with a propeller that can operate in a ground fine range must be equipped with a system to annunciate when the propeller is, in fact, in the ground fine range. Because this annunciation system (the beta lights you see during normal ground fine operations) is powered from the same CB that you pull to depower the beta backup system, you lose the annunciation of ground fine range when you pull that CB. Hence, because there is no more annunciation of (normal, commanded) ground fine operation if you have pulled the CB, the MMEL then states that you must not invoke an operational mode (ground fine)that you know will not be annunciated to you. That is, however, a guess on my part.
I assume that the Beta Backup system was installed originally to avoid, the risk of inflight prop reversal at high torque settings...
No, not at all. If you think about it for a moment, the only possible way that the propeller can enter the ground fine range (in other words, zero thrust or reverse) is if the propeller is in an underspeed condition relative to what the pilot has selected with the prop levers. It is flat-out impossible for the propeller to enter the ground fine range if the power levers are significantly forward of the idle position (in other words, creating the 'high torque setting' that you refer to).
This is because if you have high torque present when the power levers are in the forward range, the propeller will rotate rapidly, and the propeller governor will reduce oil flow to the propeller hub in order to coarsen blade angle (for the purpose of limiting RPM to what you have selected with the propeller levers).
The above is precisely why the abnormal checklist for a cycling beta light (indicating mechanical failure somewhere, with the beta backup system operating correctly, as it was designed to do) tells you to move the propeller levers to the minimum RPM position - this to make it as easy as possible for the propeller governor to take control - then add a bit of power - that to increase propeller speed, so that the propeller governor becomes active, begins to govern, and restricts oil flow to the hub.
Why... has the FAA approved an MEL for it?
The beta backup system is analogous to a smoke detector in a house. If the smoke detector activates as a result of the presence of smoke, hey, it's doing what it was designed to do, and the 'memory items' on the checklist begin with "Get out of the house..." However, if the smoke detector activates and starts making a great noise and commotion, and subsequent careful investigation shows that there is no smoke anywhere (perhaps you banged it and caused something inside the smoke detector to break), then, the checklist for your house suggests that you depower the smoke alarm and then carry on as normal, taking note that you no longer have a warning system to advise you if smoke is present.
The MMEL entry for the beta backup system addresses circumstances when the backup system operates when it should not operate (usually as a result of breakage of a microswitch out at the propeller). For example, consider that you are flying along in cruise, when suddenly one propeller slowly begins to feather. Torque rises at first (then drops as the propeller blade stalls), and Np drops dramatically from your usual 75% cruise to about 20 or 25%.
You look out the window, and see a propeller that is obviously feathered. Your leg muscles are throbbing from stuffing full rudder in to counteract the complete loss of thrust from the engine with the feathered propeller. But... one little beta light is illuminated, indicating to you that the propeller is in the ground fine range (less than +9° blade angle). You look out the window again and confirm that the propeller is at the full feathered position (+87° blade angle). The warning system - the beta backup system - is obviously crying Wolf, same as your smoke detector did. So, the checklist for the steady beta light tells you to do exactly what you did with your smoke detector - remove the power from the warning system that is raising the false alarm, then, go back to business as usual.
The MMEL entry allows you to dispatch from the next place that you land, and get the plane back to a maintenance base to get the "warning system" fixed.
Does the AFM contain an abnormal to deal with exactly this situation?
Yes. There are two abnormal procedures that deal with the beta backup system. The abnormal procedure for a STEADY beta light explains how to deal with a false alarm such as what I just described above. The abnormal procedure for a FLASHING beta light tells you how to deal with a mechanical failure of the propeller linkage that has caused the propeller to enter the ground fine range without the pilot commanding it to do so.
Note that neither of these procedures are memory items, and neither one requires fast or immediate action.
If you have a FLASHING beta light and you take a long time to complete the checklist, the worst that will happen is that the aircraft will yaw back and forth a little bit every time you reduce the power to a very low level... your passengers will think that you have a new co-pilot who is flying the plane while wearing 10 pound combat boots.
If you have a STEADY beta light and you take a long time to complete the checklist, the worst that will happen is that you will get a leg cramp from pressing on the rudder pedal (assuming that you don't apply trim). What you will have is, effectively, a single engine aircraft resulting from one propeller feathering itself in flight.
...Transport-Canada has approved the Kenn Borek STC to remove it
That is correct. Clearly TC thought that the STC was worthy of approval.
...and the 400 series doesn't even have it...
That is also correct. Clearly the manufacturer of the Series 400 Twin Otter thought that the system was not necessary, and TC agreed. Note, however, that the Series 400 does have a system to indicate to the pilot when the propeller enters the ground fine range. If the propeller enters the ground fine range when the aircraft is on ground AND the pilot has commanded ground fine range (evidenced by twisting the power levers, which activates the switch above the power levers), the background behind the Np indication changes to a blue colour, as shown in the illustration below.
But, if the propeller enters the ground fine range when the aircraft is in flight, a red PROPELLER LOW PITCH Crew Alerting System (CAS) message appears, an aural warning "Propeller Low Pitch" is voiced, and the Master Caution annunciator illuminates. So, although the backup system itself has been deleted from the Series 400, annunciation of propeller entry to the ground fine range is retained - both for normal and abnormal circumstances.
Hope this answers your questions.
Michael
Series 400 Annunciation of Ground Fine Range (commanded)
You ask some very reasonable questions. I'm going to try my best to answer them, however, because it is no secret here in the forum where I work or what I do at work, I am going to have to be somewhat circumspect with my reply.
With the system depowered (via the MEL), why can you not select reverse?
I have no answer for that. That particular restriction has been present in the MMEL since before the Old King died. If I was to rewrite the MMEL today, I would not include that restriction. The beta backup system is only depowered (i.e. circuit breaker pulled) when there is a problem with the (electrical) beta backup system... under these conditions the (mechanical) propeller control system is operating normally. Hence, I cannot explain why that requirement to not select reverse is there.
It is possible that the restriction to not select reverse arises as a result of a certification requirement that states that an aircraft equipped with a propeller that can operate in a ground fine range must be equipped with a system to annunciate when the propeller is, in fact, in the ground fine range. Because this annunciation system (the beta lights you see during normal ground fine operations) is powered from the same CB that you pull to depower the beta backup system, you lose the annunciation of ground fine range when you pull that CB. Hence, because there is no more annunciation of (normal, commanded) ground fine operation if you have pulled the CB, the MMEL then states that you must not invoke an operational mode (ground fine)that you know will not be annunciated to you. That is, however, a guess on my part.
I assume that the Beta Backup system was installed originally to avoid, the risk of inflight prop reversal at high torque settings...
No, not at all. If you think about it for a moment, the only possible way that the propeller can enter the ground fine range (in other words, zero thrust or reverse) is if the propeller is in an underspeed condition relative to what the pilot has selected with the prop levers. It is flat-out impossible for the propeller to enter the ground fine range if the power levers are significantly forward of the idle position (in other words, creating the 'high torque setting' that you refer to).
This is because if you have high torque present when the power levers are in the forward range, the propeller will rotate rapidly, and the propeller governor will reduce oil flow to the propeller hub in order to coarsen blade angle (for the purpose of limiting RPM to what you have selected with the propeller levers).
The above is precisely why the abnormal checklist for a cycling beta light (indicating mechanical failure somewhere, with the beta backup system operating correctly, as it was designed to do) tells you to move the propeller levers to the minimum RPM position - this to make it as easy as possible for the propeller governor to take control - then add a bit of power - that to increase propeller speed, so that the propeller governor becomes active, begins to govern, and restricts oil flow to the hub.
Why... has the FAA approved an MEL for it?
The beta backup system is analogous to a smoke detector in a house. If the smoke detector activates as a result of the presence of smoke, hey, it's doing what it was designed to do, and the 'memory items' on the checklist begin with "Get out of the house..." However, if the smoke detector activates and starts making a great noise and commotion, and subsequent careful investigation shows that there is no smoke anywhere (perhaps you banged it and caused something inside the smoke detector to break), then, the checklist for your house suggests that you depower the smoke alarm and then carry on as normal, taking note that you no longer have a warning system to advise you if smoke is present.
The MMEL entry for the beta backup system addresses circumstances when the backup system operates when it should not operate (usually as a result of breakage of a microswitch out at the propeller). For example, consider that you are flying along in cruise, when suddenly one propeller slowly begins to feather. Torque rises at first (then drops as the propeller blade stalls), and Np drops dramatically from your usual 75% cruise to about 20 or 25%.
You look out the window, and see a propeller that is obviously feathered. Your leg muscles are throbbing from stuffing full rudder in to counteract the complete loss of thrust from the engine with the feathered propeller. But... one little beta light is illuminated, indicating to you that the propeller is in the ground fine range (less than +9° blade angle). You look out the window again and confirm that the propeller is at the full feathered position (+87° blade angle). The warning system - the beta backup system - is obviously crying Wolf, same as your smoke detector did. So, the checklist for the steady beta light tells you to do exactly what you did with your smoke detector - remove the power from the warning system that is raising the false alarm, then, go back to business as usual.
The MMEL entry allows you to dispatch from the next place that you land, and get the plane back to a maintenance base to get the "warning system" fixed.
Does the AFM contain an abnormal to deal with exactly this situation?
Yes. There are two abnormal procedures that deal with the beta backup system. The abnormal procedure for a STEADY beta light explains how to deal with a false alarm such as what I just described above. The abnormal procedure for a FLASHING beta light tells you how to deal with a mechanical failure of the propeller linkage that has caused the propeller to enter the ground fine range without the pilot commanding it to do so.
Note that neither of these procedures are memory items, and neither one requires fast or immediate action.
If you have a FLASHING beta light and you take a long time to complete the checklist, the worst that will happen is that the aircraft will yaw back and forth a little bit every time you reduce the power to a very low level... your passengers will think that you have a new co-pilot who is flying the plane while wearing 10 pound combat boots.
If you have a STEADY beta light and you take a long time to complete the checklist, the worst that will happen is that you will get a leg cramp from pressing on the rudder pedal (assuming that you don't apply trim). What you will have is, effectively, a single engine aircraft resulting from one propeller feathering itself in flight.
...Transport-Canada has approved the Kenn Borek STC to remove it
That is correct. Clearly TC thought that the STC was worthy of approval.
...and the 400 series doesn't even have it...
That is also correct. Clearly the manufacturer of the Series 400 Twin Otter thought that the system was not necessary, and TC agreed. Note, however, that the Series 400 does have a system to indicate to the pilot when the propeller enters the ground fine range. If the propeller enters the ground fine range when the aircraft is on ground AND the pilot has commanded ground fine range (evidenced by twisting the power levers, which activates the switch above the power levers), the background behind the Np indication changes to a blue colour, as shown in the illustration below.
But, if the propeller enters the ground fine range when the aircraft is in flight, a red PROPELLER LOW PITCH Crew Alerting System (CAS) message appears, an aural warning "Propeller Low Pitch" is voiced, and the Master Caution annunciator illuminates. So, although the backup system itself has been deleted from the Series 400, annunciation of propeller entry to the ground fine range is retained - both for normal and abnormal circumstances.
Hope this answers your questions.
Michael
Series 400 Annunciation of Ground Fine Range (commanded)
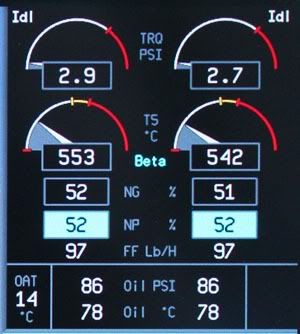

MachTwelve (what is your first name, anyway?):
The procedure you refer to for 'inflight propeller reversal' (item 3.2.3 at revision 43 status) is totally unrelated to the beta backup system procedures. I realize that the causal factor for such a problem would, in theory, be something that should be caught (and prevented) by the beta backup system, but don't mix apples and oranges by trying to read too deep into the probable cause of the potential problem that this procedure addresses.
What the AFM says is (in summary) this: If a propeller enters the reverse range during flight and the aircraft does not have propeller blade latches installed, shut down the engine. If the aircraft does have propeller blade latches installed (these are normally only found on aircraft that are operated on floats for all or part of the year), then don't shut the engine down, just move the power lever to idle.
That procedure makes sense. For your information, I have reviewed engineering, certification, and flight test data that shows that with engine power at idle, a fully reversed (-15° blade angle) propeller actually creates less drag than the same propeller at +11° blade angle. This is because there is less flat plate drag presented at -15° than there is at +11°. So, the 'inflight propeller reversal' - a pretty remote possibility with the propeller control system installed on the Twin Otter - is not something that you should stay up late at night worrying about.
DON'T EVEN THINK ABOUT DOING THAT!
If you refer to the "Safety of Flight Supplement" number 4, dated 1 February 1981, which is found at the beginning of the Supplementary Operating Data (PSM 1-63-1), you will see that de Havilland explicitly forbids doing this.
For either one of the beta malfunctions (steady light or flashing light), take your time, go slowly, correctly identify the nature of the malfunction, correctly identify the right checklist to use and get agreement from the other pilot (if you are in a two-crew environment), then carry out the checklist actions as "read aloud and do", not from memory.
As I said earlier, if you were to freeze up in terror and do absolutely nothing in response to a steady beta light, the only consequence would be that you would get a sore leg from holding in all the rudder during the single-engine flight that would result. If you were to freeze up in terror and do absolutely nothing in response to a flashing beta light, the only consequence would be that when you finally brought the power back for landing, the aircraft would yaw back and forth a little bit (entirely controllably) during the flare.
However... if you act in haste and screw up and carry out the wrong procedure (e.g. complete the 'steady beta light' procedure when the problem is in fact a 'flashing beta light'), the consequences could be quite severe.
You have to keep in mind that the ONLY time that the propeller can go into a very fine pitch (meaning, less than +11°, with the reverse range from 0° to -15° being sort of an 'ultra fine pitch') is when the propeller is underspeeding relative to the propeller governor. This means that during the takeoff, climb, and cruise phases of flight, it is impossible to get a flashing beta light, because during all those phases of flight, because the large amount of power (torque) being applied to the propeller is keeping it under the control of the governor, which modulates the oil supply in order to maintain the propeller RPM selected by the pilot.
The only time that the 'flashing beta light' malfunction can appear is during the approach and/or landing phase of flight, when the power being applied to the propeller is reduced to such a low value that it is insufficient to keep the propeller turning at the RPM selected by the pilot. If the flashing beta light malfunction does appear, and the pilot adds power (one of the two items the checklist calls for the pilot to do), the addition of power will increase propeller RPM and hand control of the propeller back to the governor. The problem will disappear, at least, it will disappear until the power lever is next pulled back and the propeller is unable to maintain the speed selected using the PROP lever.
It was mandated because the design of the propeller control system used on the Twin Otter - which provides direct control of propeller blade angle via the power lever during approach and landing - was considered new and novel when it was first introduced in the 1960s. Therefore, the regulators at the time asked for an independent electrical (rather than mechanical) backup system to prevent the propeller from entering the ground fine range during flight should the mechanical system somehow fail. This was prudent on their behalf and entirely understandable given the lack of flight experience with this new and novel propeller control system.
40 years later, we have the benefit of having learned from (literally) millions of hours of Twin Otter flight time that:
1) If the mechanical propeller control system fails, 99.9% of the time, the result is that the propeller feathers. That is the least hazardous thing that the propeller could do as a result of a failure, and no back-up system is needed if the propeller feathers.
2) Although the theory behind the beta backup system is sound, in practice, the system causes more problems (unwanted featherings as a result of the 'steady beta light' scenario) that it prevents. Therefore, regulators have approved STC modifications permitting removal of the backup system - although the INDICATION system (lights that show when the propeller is in the ground fine range) must remain.
Be aware, however, that during the 1980s, de Havilland introduced an optional modification to the design of the beta backup system (Mod 6/1831, S/B 6/478 at Rev A refers) that replaced the propeller mounted microswitches with a proximity switch, and this modification has virtually eliminated all 'steady beta light' malfunctions, except of course for those arising from a rigging problem, which would in any case be detected on the ground as soon as the engine was started up following the maintenance activity. This modification can be easily retrofitted to all legacy DHC-6 aircraft.
In the case of the Series 400, a very clear alert (text message and voice announcement) is made to the pilot if the propeller ever enters the ground fine range during flight. The actions that the Series 400 pilot then takes are identical to the actions set out for the "flashing beta light" for a Series 300 aircraft.
--------------
You may also want to review and compare the actions set out in the AFMs of single engine aircraft that use a similar engine and propeller control system (e.g. Cessna Caravan, Pilatus PC-6, Pilatus PC-12) and do not utilize a 'high idle' fuel control position such as the Beech products. Aircraft that utilize a 'high idle' position are, mechanically, sufficiently different that it is not appropriate to make a direct comparison with the Twin Otter.
Michael
Originally Posted by MachTwelve
The AFM abnormal I was actually referring to was 3.2.3 Inflight Propeller Reversal.
The procedure you refer to for 'inflight propeller reversal' (item 3.2.3 at revision 43 status) is totally unrelated to the beta backup system procedures. I realize that the causal factor for such a problem would, in theory, be something that should be caught (and prevented) by the beta backup system, but don't mix apples and oranges by trying to read too deep into the probable cause of the potential problem that this procedure addresses.
What the AFM says is (in summary) this: If a propeller enters the reverse range during flight and the aircraft does not have propeller blade latches installed, shut down the engine. If the aircraft does have propeller blade latches installed (these are normally only found on aircraft that are operated on floats for all or part of the year), then don't shut the engine down, just move the power lever to idle.
That procedure makes sense. For your information, I have reviewed engineering, certification, and flight test data that shows that with engine power at idle, a fully reversed (-15° blade angle) propeller actually creates less drag than the same propeller at +11° blade angle. This is because there is less flat plate drag presented at -15° than there is at +11°. So, the 'inflight propeller reversal' - a pretty remote possibility with the propeller control system installed on the Twin Otter - is not something that you should stay up late at night worrying about.
Originally Posted by MachTwelve
...can you comment on the option of twisting the power levers to dis-arm the system...
DON'T EVEN THINK ABOUT DOING THAT!
If you refer to the "Safety of Flight Supplement" number 4, dated 1 February 1981, which is found at the beginning of the Supplementary Operating Data (PSM 1-63-1), you will see that de Havilland explicitly forbids doing this.
For either one of the beta malfunctions (steady light or flashing light), take your time, go slowly, correctly identify the nature of the malfunction, correctly identify the right checklist to use and get agreement from the other pilot (if you are in a two-crew environment), then carry out the checklist actions as "read aloud and do", not from memory.
As I said earlier, if you were to freeze up in terror and do absolutely nothing in response to a steady beta light, the only consequence would be that you would get a sore leg from holding in all the rudder during the single-engine flight that would result. If you were to freeze up in terror and do absolutely nothing in response to a flashing beta light, the only consequence would be that when you finally brought the power back for landing, the aircraft would yaw back and forth a little bit (entirely controllably) during the flare.
However... if you act in haste and screw up and carry out the wrong procedure (e.g. complete the 'steady beta light' procedure when the problem is in fact a 'flashing beta light'), the consequences could be quite severe.
You have to keep in mind that the ONLY time that the propeller can go into a very fine pitch (meaning, less than +11°, with the reverse range from 0° to -15° being sort of an 'ultra fine pitch') is when the propeller is underspeeding relative to the propeller governor. This means that during the takeoff, climb, and cruise phases of flight, it is impossible to get a flashing beta light, because during all those phases of flight, because the large amount of power (torque) being applied to the propeller is keeping it under the control of the governor, which modulates the oil supply in order to maintain the propeller RPM selected by the pilot.
The only time that the 'flashing beta light' malfunction can appear is during the approach and/or landing phase of flight, when the power being applied to the propeller is reduced to such a low value that it is insufficient to keep the propeller turning at the RPM selected by the pilot. If the flashing beta light malfunction does appear, and the pilot adds power (one of the two items the checklist calls for the pilot to do), the addition of power will increase propeller RPM and hand control of the propeller back to the governor. The problem will disappear, at least, it will disappear until the power lever is next pulled back and the propeller is unable to maintain the speed selected using the PROP lever.
Originally Posted by MachTwelve
...don't really understand why it was mandated and thence effectively (via both the STC and the 400) the requirement was removed.
40 years later, we have the benefit of having learned from (literally) millions of hours of Twin Otter flight time that:
1) If the mechanical propeller control system fails, 99.9% of the time, the result is that the propeller feathers. That is the least hazardous thing that the propeller could do as a result of a failure, and no back-up system is needed if the propeller feathers.
2) Although the theory behind the beta backup system is sound, in practice, the system causes more problems (unwanted featherings as a result of the 'steady beta light' scenario) that it prevents. Therefore, regulators have approved STC modifications permitting removal of the backup system - although the INDICATION system (lights that show when the propeller is in the ground fine range) must remain.
Be aware, however, that during the 1980s, de Havilland introduced an optional modification to the design of the beta backup system (Mod 6/1831, S/B 6/478 at Rev A refers) that replaced the propeller mounted microswitches with a proximity switch, and this modification has virtually eliminated all 'steady beta light' malfunctions, except of course for those arising from a rigging problem, which would in any case be detected on the ground as soon as the engine was started up following the maintenance activity. This modification can be easily retrofitted to all legacy DHC-6 aircraft.
In the case of the Series 400, a very clear alert (text message and voice announcement) is made to the pilot if the propeller ever enters the ground fine range during flight. The actions that the Series 400 pilot then takes are identical to the actions set out for the "flashing beta light" for a Series 300 aircraft.
--------------
You may also want to review and compare the actions set out in the AFMs of single engine aircraft that use a similar engine and propeller control system (e.g. Cessna Caravan, Pilatus PC-6, Pilatus PC-12) and do not utilize a 'high idle' fuel control position such as the Beech products. Aircraft that utilize a 'high idle' position are, mechanically, sufficiently different that it is not appropriate to make a direct comparison with the Twin Otter.
Michael

Hi Pete:
I would highly recommend that the operators of those aircraft consider fitting Mod 6/1831. That would address the root of the problem, and eliminate any perceived need by the pilots to follow non-standard procedures to cope with problems.
Below is an image of the "Safety of Flight" supplement that DH promulgated in 1980.
I would highly recommend that the operators of those aircraft consider fitting Mod 6/1831. That would address the root of the problem, and eliminate any perceived need by the pilots to follow non-standard procedures to cope with problems.
Below is an image of the "Safety of Flight" supplement that DH promulgated in 1980.
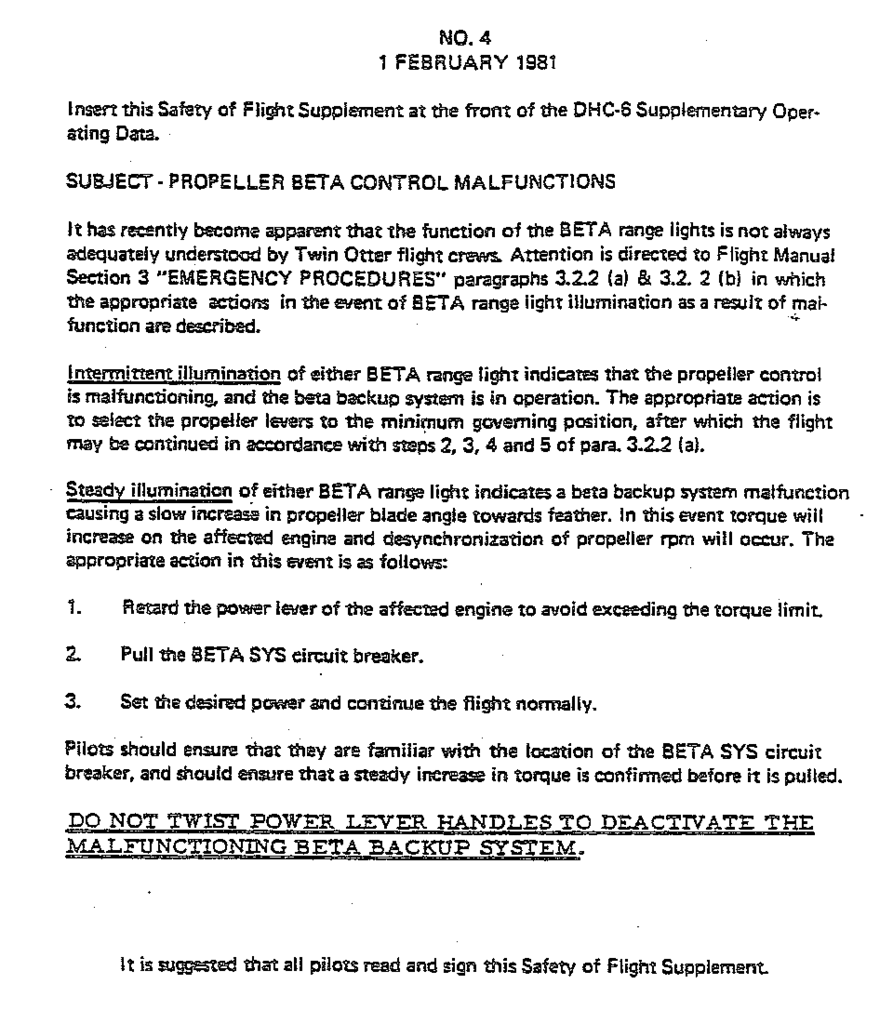

Join Date: Jun 2007
Location: SAYE
Posts: 281
Likes: 0
Received 0 Likes
on
0 Posts
Michael,
Many thanks for the in-depth comments and remarks.
About twisting the power lever in flight, a good reminder not to do it is the March 2001 accident of F-OGES on approach to TFFJ. Prior to the accident the pilot reported that he used to use "beta" in flight in order to slow down during the [non-conventional] approach to this particular runway. Video footage (and audio) taken by a PAX during the flight was retrieved from the wreckage and supported the probable cause.
PROBABLE CAUSES: "The accident appears to result from the Captain's use of the propellers in the reverse beta range, to improve control of his track on short final. A strong thrust asymmetry at the moment when coming out of the reverse beta range would have caused the loss of yaw control, then roll control of the aircraft.
Accident description
BEA Accident Report
Many thanks for the in-depth comments and remarks.
About twisting the power lever in flight, a good reminder not to do it is the March 2001 accident of F-OGES on approach to TFFJ. Prior to the accident the pilot reported that he used to use "beta" in flight in order to slow down during the [non-conventional] approach to this particular runway. Video footage (and audio) taken by a PAX during the flight was retrieved from the wreckage and supported the probable cause.
PROBABLE CAUSES: "The accident appears to result from the Captain's use of the propellers in the reverse beta range, to improve control of his track on short final. A strong thrust asymmetry at the moment when coming out of the reverse beta range would have caused the loss of yaw control, then roll control of the aircraft.
Accident description
BEA Accident Report

Hello Pete:
I don't think there is a reference in the Revision 52 (current version) AFM or the current version Supplementary Operating Data that addresses how long to wait to allow fuel to settle prior to using the dipstick.
The Series 300 AFM has recently been completely revised, and this new revision of the AFM (all pages are at Revision 53 status) will be distributed to operators who subscribe to the document revision service sometime within the next few months. I believe that the document is at the printers now, and I am going to GUESS that it will be distributed to subscribers sometime in the first quarter 2011.
I have attached an image below showing the remarks about the dipstick that are contained in this new (Revision 53) AFM.
A note to everyone: I cannot, and will not participate in any further discussion about the contents of the Revision 53 AFM until it is distributed. To do so would just cause chaos, I am sure you can all appreciate that.
Here's the blurb that addresses use of the dipstick. Note that it is by no means obligatory to use the dipstick.
I don't think there is a reference in the Revision 52 (current version) AFM or the current version Supplementary Operating Data that addresses how long to wait to allow fuel to settle prior to using the dipstick.
The Series 300 AFM has recently been completely revised, and this new revision of the AFM (all pages are at Revision 53 status) will be distributed to operators who subscribe to the document revision service sometime within the next few months. I believe that the document is at the printers now, and I am going to GUESS that it will be distributed to subscribers sometime in the first quarter 2011.
I have attached an image below showing the remarks about the dipstick that are contained in this new (Revision 53) AFM.
A note to everyone: I cannot, and will not participate in any further discussion about the contents of the Revision 53 AFM until it is distributed. To do so would just cause chaos, I am sure you can all appreciate that.
Here's the blurb that addresses use of the dipstick. Note that it is by no means obligatory to use the dipstick.
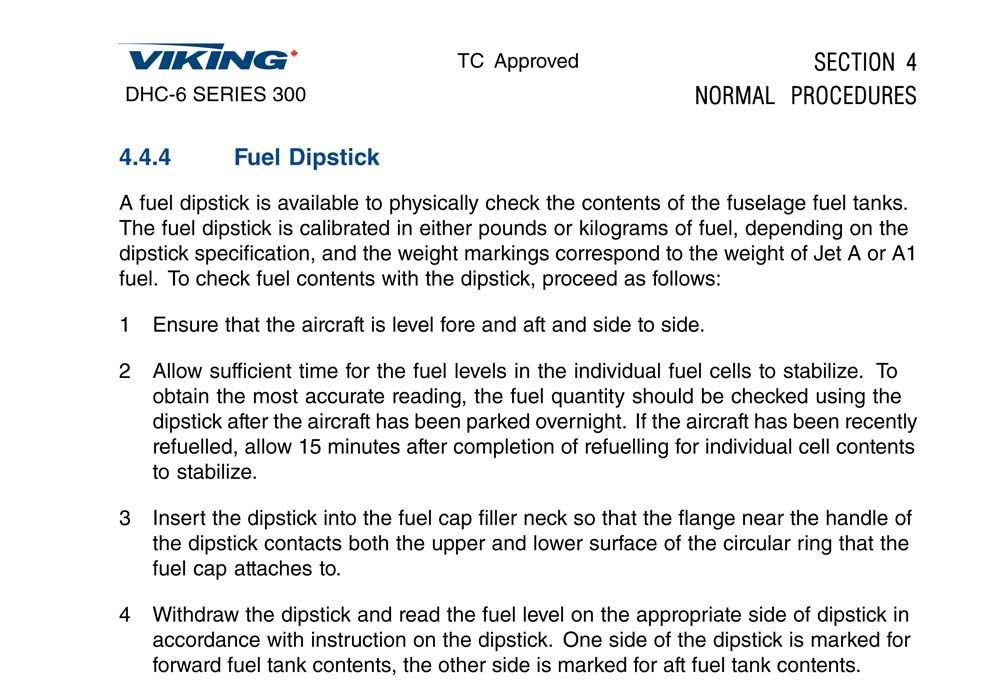

Join Date: Dec 2010
Location: Hiding in the Rockies
Posts: 79
Likes: 0
Received 0 Likes
on
0 Posts
In the Arctic we started in fine pitch on all models 100, 200 & 300. It started oil flowing to the prop and thus lubricating the shaft. We had some initial problems with shaft bearings due to the different coefficients of expansion at those temps. At those temps we would feather at least 4 or 5 times after the start to keep the oil flowing. And this was after about 30 minutes with Herman in each intake (engine covers on).


Join Date: Apr 2008
Location: nowhere
Posts: 1
Likes: 0
Received 0 Likes
on
0 Posts
Never held the prop once for this reason and never heard of anyone else doing it either. Tried to hold a prop once during a start and I remember that it took quite a bit of force. Mind you we always plugged in our engines.
Besides, why not let your oil warm up while in feather. Isn't it actual prop blade blade angle change that will damage seals?
Besides, why not let your oil warm up while in feather. Isn't it actual prop blade blade angle change that will damage seals?
Last edited by JammedStab; 12th Oct 2012 at 09:13.
