Starting and running an IO540-K1A5 w/CS prop
Thread Starter
Join Date: Feb 2007
Location: Amsterdam
Posts: 4,598
Likes: 0
Received 0 Likes
on
0 Posts
Starting and running an IO540-K1A5 w/CS prop
It looks likely that in the near future I'm going to be flying an aircraft equipped with a Lycoming IO540-K1A5 engine and a C/S propellor. Obviously after a checkout with an instructor, but I'd like to hit the ground running and am studying the POH and related documents. I'm a bit confused by what exactly happens inside a fuel injected engine and inside a C/S hub, and can't find any answers in the ol' Jeremy Pratt books...
1. Priming. Throttle half open, fuel pump on, mixture rich OR mixture rich and prime with the prime button (which operates the fuel pump) for a few seconds (4-5 when cold, 2-4 when hot). Then close the throttle for a hot start, or set the throttle to 1/4" for a hot start. Why the half throttle during the prime? Does the throttle, in a fuel injected engine, have any influence on the fuel flow/injectors/whatever and if so, how?
2. Starting. Once primed, you run the starter with the mixture ICO, then move the mixture once the engine catches. What exactly happens in the engine at this time? Is the fuel in liquid, vapor, atomized, gas state, and where does it collect? I assume it has something to do with starting over-rich and since you are adding air but no fuel, the engine will find its right mixture point by itself, at which point you add fuel. True?
3. Why the difference between 1/4" throttle on a cold start, and closed throttle on a hot start? Any other tips on hot starting? (It looks like hot starting will happen a lot in the type of operations we're going to do.)
4. Run-up. At 1500 RPM you exercise/check the prop governor. Do you pull all the way back, or until you see a 500 RPM drop? What is the normal governing range that this blue lever sets? Furthermore, one of the items to check while doing this is the oil pressure rising. Why is that?
5. Furthermore, there is a full-power check, where you check the RPM, oil pressure and a few other obvious items. But it also says "check max power available". How do you know the engine is developing max power? Fuel flow? EGT?
6. Last. Say you're doing six flights a day. Do you do the magneto/prop/full power check for every flight, or are there things that you can reasonably skip after having done them on the first flight?
1. Priming. Throttle half open, fuel pump on, mixture rich OR mixture rich and prime with the prime button (which operates the fuel pump) for a few seconds (4-5 when cold, 2-4 when hot). Then close the throttle for a hot start, or set the throttle to 1/4" for a hot start. Why the half throttle during the prime? Does the throttle, in a fuel injected engine, have any influence on the fuel flow/injectors/whatever and if so, how?
2. Starting. Once primed, you run the starter with the mixture ICO, then move the mixture once the engine catches. What exactly happens in the engine at this time? Is the fuel in liquid, vapor, atomized, gas state, and where does it collect? I assume it has something to do with starting over-rich and since you are adding air but no fuel, the engine will find its right mixture point by itself, at which point you add fuel. True?
3. Why the difference between 1/4" throttle on a cold start, and closed throttle on a hot start? Any other tips on hot starting? (It looks like hot starting will happen a lot in the type of operations we're going to do.)
4. Run-up. At 1500 RPM you exercise/check the prop governor. Do you pull all the way back, or until you see a 500 RPM drop? What is the normal governing range that this blue lever sets? Furthermore, one of the items to check while doing this is the oil pressure rising. Why is that?
5. Furthermore, there is a full-power check, where you check the RPM, oil pressure and a few other obvious items. But it also says "check max power available". How do you know the engine is developing max power? Fuel flow? EGT?
6. Last. Say you're doing six flights a day. Do you do the magneto/prop/full power check for every flight, or are there things that you can reasonably skip after having done them on the first flight?
Join Date: Dec 2011
Posts: 2,460
Likes: 0
Received 0 Likes
on
0 Posts
I have an IO540-C4D5D.
The starting is installation and fuel system layout dependent. The POH procedure should work for both cold and hot starts.
The tricky bit is "warm" starts and usually the hot start procedure works but it needs more cranking. What really helps, in all conditions, is a Sky-tec lightweight starter. These draw a lot more current (so the starter relay and potentially other relays carrying the starter motor current get knackered more quickly, unless you replace them with better versions) but they turn the engine so fast that starting problems just go away.
You generally check the fuel flow on the takeoff power setting. 23USG/hr for mine @ISA.
Mag check every flight.
Prop governor I do every flight (2x) but it is not really necessary once the governor is full of nice warm oil.
Full power fuel flow - must check on each takeoff.
The starting is installation and fuel system layout dependent. The POH procedure should work for both cold and hot starts.
The tricky bit is "warm" starts and usually the hot start procedure works but it needs more cranking. What really helps, in all conditions, is a Sky-tec lightweight starter. These draw a lot more current (so the starter relay and potentially other relays carrying the starter motor current get knackered more quickly, unless you replace them with better versions) but they turn the engine so fast that starting problems just go away.
5. Furthermore, there is a full-power check, where you check the RPM, oil pressure and a few other obvious items. But it also says "check max power available". How do you know the engine is developing max power? Fuel flow? EGT?
6. Last. Say you're doing six flights a day. Do you do the magneto/prop/full power check for every flight, or are there things that you can reasonably skip after having done them on the first flight?
Prop governor I do every flight (2x) but it is not really necessary once the governor is full of nice warm oil.
Full power fuel flow - must check on each takeoff.
Good luck. A while back I flew about 100 hours in a 182T with an IO540. Cold starts were easy. Hot starts were a nightmare, a variation of the old pilot joke/saying: "There are three secrets to getting a fuel injected engine to start first time every time. Unfortunately, nobody knows what they are". I only came close to tears/beating the thing with a large spanner once, I never actually had it fail completely to start. Generally there is some combination of full/partial/idle throttle, cutoff/full mixture and no/slight/normal/over prime that works, before the battery dies. Generally.
The theory, iirc, was no prime, throttle cracked. I don't think I ever got that to work.
Considering that the ultimate recourse to starting an injected engine is generally full-rich mixture, I've never really understood why the normal way is with idle cutoff mixture. iirc the desperation technique was half throttle, rich mixture, a bit more prime than for a cold start, crank and crank and crank. iirc.
Otoh the same engine in the R44 starts easily even when hot. Go figure.
The theory, iirc, was no prime, throttle cracked. I don't think I ever got that to work.
Considering that the ultimate recourse to starting an injected engine is generally full-rich mixture, I've never really understood why the normal way is with idle cutoff mixture. iirc the desperation technique was half throttle, rich mixture, a bit more prime than for a cold start, crank and crank and crank. iirc.
Otoh the same engine in the R44 starts easily even when hot. Go figure.
In all the Lycoming IO- or TSIO-540s I've flown, I've found it easiest to to prime with Throttle FULL OPEN & Mixture RICH then Pump ON to prime then OFF for both hot or cold starts . Slightly longer prime for cold, barely pumps ON for hot or warm. Then Throttle just cracked eg 1/4" when cold, and fully open for hot. Takes the guess work out of it.
Crank with mixture ICO then advance mixture once the engine catches. If a hot start then use your starter switch hand to retard the throttle as you advance the mixture.
Crank with mixture ICO then advance mixture once the engine catches. If a hot start then use your starter switch hand to retard the throttle as you advance the mixture.
Last edited by Tinstaafl; 4th Oct 2012 at 13:55.
Join Date: Mar 2009
Location: QLD
Age: 35
Posts: 123
Likes: 0
Received 0 Likes
on
0 Posts
IO540 (in a TB20)
Throttle 1/4", mixture rich, prime with fuel pump
6 seconds if cold
2 seconds if warm (doesn't start? Prime again 2secs)
0 seconds if hot (doesn't start? Prime 2secs)
Fuel pump off, mixture cut-off, engage starter and mixture back to rich when it fires. Works everytime for me.
Throttle 1/4", mixture rich, prime with fuel pump
6 seconds if cold
2 seconds if warm (doesn't start? Prime again 2secs)
0 seconds if hot (doesn't start? Prime 2secs)
Fuel pump off, mixture cut-off, engage starter and mixture back to rich when it fires. Works everytime for me.
Thread Starter
Join Date: Feb 2007
Location: Amsterdam
Posts: 4,598
Likes: 0
Received 0 Likes
on
0 Posts
Okay, I gather that starting that engine, particularly when hot, will be a bit of a black art and is best taught by somebody familiar with that particular aircraft. As they will know the proper deities of fuel, air and spark to appeal to.
But now for the more technical questions. Can someone describe the interconnect between throttle and fuel injectors/metering? When the fuel is injected during priming and running, where does it end up and in what state? What happens exactly during the prop exercising in the runup?
But now for the more technical questions. Can someone describe the interconnect between throttle and fuel injectors/metering? When the fuel is injected during priming and running, where does it end up and in what state? What happens exactly during the prop exercising in the runup?
Join Date: Feb 2002
Location: Dublin
Posts: 2,547
Likes: 0
Received 0 Likes
on
0 Posts
1. Priming. Throttle half open, fuel pump on, mixture rich OR mixture rich and prime with the prime button (which operates the fuel pump) for a few seconds (4-5 when cold, 2-4 when hot). Then close the throttle for a hot start, or set the throttle to 1/4" for a hot start. Why the half throttle during the prime? Does the throttle, in a fuel injected engine, have any influence on the fuel flow/injectors/whatever and if so, how?
Join Date: Aug 2012
Location: Wales
Posts: 532
Likes: 0
Received 0 Likes
on
0 Posts
Hi Backpacker, our club has a 172SP with a fuel injected engine, and it is a pig to start when hot. It requires absolutely no priming, which might be unique to itself.
I once sat in another aircraft behind it at the pumps, whilst the SP Pilot almost drained the battery trying to get it to run after re-fuelling...
As to where the fuel goes....
It goes all over the concrete apron just underneath the engine !
Pete
I once sat in another aircraft behind it at the pumps, whilst the SP Pilot almost drained the battery trying to get it to run after re-fuelling...
As to where the fuel goes....
It goes all over the concrete apron just underneath the engine !
Pete
Join Date: Dec 2011
Posts: 2,460
Likes: 0
Received 0 Likes
on
0 Posts
In order to get some fuel to flow in to prime the engine, the throttle needs to be opened.

There are installations where the extra fuel is recycled back to the wing tank(s) but I believe they are mostly Conti setups.
Pilot forums are full of weird starting tips but I have never had starting problems by just following the POH.
Join Date: Jan 2008
Location: lancs.UK
Age: 77
Posts: 1,191
Likes: 0
Received 0 Likes
on
0 Posts
How this is a very interesting question!
Plenty of replies by "skilled" operators who haven't a clue how the bloody thing works!!!....So that was a waste of study-time for your PPL, wasn't it?
Without understanding the fundamentals of the injection-system, it will continue to be a "black art"
Machines are inanimate......within production tolerances, there should be very little variation in the starting technique,-but that depends on the sophistication (or lack thereof) of the fuel-system.
I'm curious to know more and would suggest to the OP that the Lyco. workshop manual may be the starting-point (so to speak)
Likewise the CS Prop.
Most tech. manuals wil be prefaced with a chapter on general principles of design and operation.
Plenty of replies by "skilled" operators who haven't a clue how the bloody thing works!!!....So that was a waste of study-time for your PPL, wasn't it?

Without understanding the fundamentals of the injection-system, it will continue to be a "black art"
Machines are inanimate......within production tolerances, there should be very little variation in the starting technique,-but that depends on the sophistication (or lack thereof) of the fuel-system.
I'm curious to know more and would suggest to the OP that the Lyco. workshop manual may be the starting-point (so to speak)
Likewise the CS Prop.
Most tech. manuals wil be prefaced with a chapter on general principles of design and operation.
Join Date: Dec 2011
Posts: 2,460
Likes: 0
Received 0 Likes
on
0 Posts
So that was a waste of study-time for your PPL, wasn't it?
Here, maybe
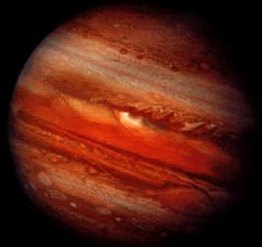
You did well

there should be very little variation in the starting technique

Last edited by peterh337; 4th Oct 2012 at 10:54.
Thread Starter
Join Date: Feb 2007
Location: Amsterdam
Posts: 4,598
Likes: 0
Received 0 Likes
on
0 Posts
Ow, come on guys. I appreciate that the PPL syllabus cannot cover each and every engine/prop combination, and the starting technique involved, that you might meet in your flying career. Let's be honest (without wanting to start a new thread on this), you can fly an A380 on a PPL and I don't think anyone would appreciate the operating procedures for an A380 to be part of the PPL syllabus.
That's why we call the PPL a "license to learn", and that's why the PPL syllabus mentions stuff like "ANO", "LASORS", "AIP", "POH" and similar acronyms. So you know where to find extra information as and when required. (They should include "PPRuNe" in the PPL syllabus though. :-) )
Could you expand on this a bit, Peter? Is that RDA fuel servo dependent on physical throttle position, or does it use MAP, or something else?
That's why we call the PPL a "license to learn", and that's why the PPL syllabus mentions stuff like "ANO", "LASORS", "AIP", "POH" and similar acronyms. So you know where to find extra information as and when required. (They should include "PPRuNe" in the PPL syllabus though. :-) )
That would be pretty normal for a Lyco fuel injected engine, with the standard RDA fuel servo,
Last edited by BackPacker; 4th Oct 2012 at 11:08.
Join Date: Aug 2001
Location: BFS
Posts: 1,177
Likes: 0
Received 0 Likes
on
0 Posts
You're right. A cold start is simple, just prime it ( and remember to turn the fuel on first! )
My only experience of IO540 is a Connie. And when that was hot, after sitting for an hour it could be a pig. One mate runs the boost pump at low boost, starts as normal and it works for him. I just follow the POH, I can't remember off hand but 'priming' it with the mixture at ico seems to ring a bell, followed by a normal prime and start I think.
The POH is your friend. But I disagree with cockney Steve. In theory they'll all be the same but with so many different installations, and engineers own little quirks, unless your flying a factory new airplane there could well be little 'tricks' for your machine. However be prepared to disregard a lot of what you hear in flying schools/clubs about it. Generally it comes from people with no experience of the engine, or even fuel injection. I've heard all sorts of crap.
My only experience of IO540 is a Connie. And when that was hot, after sitting for an hour it could be a pig. One mate runs the boost pump at low boost, starts as normal and it works for him. I just follow the POH, I can't remember off hand but 'priming' it with the mixture at ico seems to ring a bell, followed by a normal prime and start I think.
The POH is your friend. But I disagree with cockney Steve. In theory they'll all be the same but with so many different installations, and engineers own little quirks, unless your flying a factory new airplane there could well be little 'tricks' for your machine. However be prepared to disregard a lot of what you hear in flying schools/clubs about it. Generally it comes from people with no experience of the engine, or even fuel injection. I've heard all sorts of crap.
Join Date: Jul 2005
Location: SoCal
Posts: 1,929
Likes: 0
Received 0 Likes
on
0 Posts
On the various fuel-injected engines I have flown, the technique described by maehhh above is about right. Definitely a good starting point.
Re the prop governor - you cycle the thing for two reasons: check it works, get warm oil into it. This is quite hard on the engine, so typically you only pull back to see about a 500 rpm drop. Two or three times, as per POH. Definitely do this every time before t/o.
I wouldn't skip any of the engine/prop checks, even after having done several flights a day. Things that break don't know you've been flying all day - and if you don't check, you don't know....
Re the prop governor - you cycle the thing for two reasons: check it works, get warm oil into it. This is quite hard on the engine, so typically you only pull back to see about a 500 rpm drop. Two or three times, as per POH. Definitely do this every time before t/o.
I wouldn't skip any of the engine/prop checks, even after having done several flights a day. Things that break don't know you've been flying all day - and if you don't check, you don't know....
Join Date: Dec 2011
Posts: 2,460
Likes: 0
Received 0 Likes
on
0 Posts
Sorry I meant RSA, as in say the RSA-5AD1. See here for example.
My comment on Jupiter was intended to illustrate that only there would one cover fuel servo internals in the PPL ground school
My comment on Jupiter was intended to illustrate that only there would one cover fuel servo internals in the PPL ground school

Join Date: Apr 2008
Location: Cilboldentune, Britannia
Posts: 555
Likes: 0
Received 0 Likes
on
0 Posts
Isn't it that a hot engine tends to vapourise the fuel in the pipes! I read once that one technique is to run the fuel pump with the throttle closed to pump cool fuel around the system.
Join Date: Dec 2004
Location: East Anglia
Posts: 832
Likes: 0
Received 0 Likes
on
0 Posts
There are two setups for the injectors on Lycomings. Some have a return line to the fuel tank and some do not.
The injectors squirt fuel into the inlet manifold just before the inlet valve. The injectors are just open nozzles not like the computer controlled things on cars.
When you prime a cold engine, you squirt neat fuel into the inlet and the engine fires on the resulting rich mixture. You start with the mixture in ICO so that no more fuel is provided, otherwise it might flood.
When the engine is stopped hot, the heat soaks upwards to the injector lines. The fuel in these can then boil and squirt fuel out. You can then end up with an empty line which causes starting problems. Obviously this is dependent on how hot it is and the time and the configuration. Just after stopping the boiling fuel in the line will be ejected into the inlet. So sometimes hot engines can be started with no priming.
Some aircraft have a return fuel line so that you can prime when hot and fill the lines with nice cool fuel with the excess going back to the tank. Others don't and priming will cause a very rich mixture as the fuel goes straight into the hot inlet manifold.
So, that's why each engine/aircraft set-up is slightly different and there isn't a universal answer to your question.
The injectors squirt fuel into the inlet manifold just before the inlet valve. The injectors are just open nozzles not like the computer controlled things on cars.
When you prime a cold engine, you squirt neat fuel into the inlet and the engine fires on the resulting rich mixture. You start with the mixture in ICO so that no more fuel is provided, otherwise it might flood.
When the engine is stopped hot, the heat soaks upwards to the injector lines. The fuel in these can then boil and squirt fuel out. You can then end up with an empty line which causes starting problems. Obviously this is dependent on how hot it is and the time and the configuration. Just after stopping the boiling fuel in the line will be ejected into the inlet. So sometimes hot engines can be started with no priming.
Some aircraft have a return fuel line so that you can prime when hot and fill the lines with nice cool fuel with the excess going back to the tank. Others don't and priming will cause a very rich mixture as the fuel goes straight into the hot inlet manifold.
So, that's why each engine/aircraft set-up is slightly different and there isn't a universal answer to your question.
Join Date: Dec 2011
Posts: 2,460
Likes: 0
Received 0 Likes
on
0 Posts
Some aircraft have a return fuel line
There are definitely some installations where fuel is returned to the tank(s) but then I wonder how this is dealt with when installing a fuel totaliser. I have seen some STCs for those, for Lycos, and none make a provision for any of this.
The most common Lyco engine fuel system configuration has no bypass whatever. When the fuel servo is shut (closed throttle) you cannot pump any fuel into it. So both the engine driven pump and the electric pump are pumps with a built-in output pressure limit (either implicit, as in a diaphragm pump, or explicit, as in a gear pump with a spring loaded bypass valve).