Alaska Airlines 737-900 MAX loses a door in-flight out of PDX
Join Date: Jun 2009
Location: Montreal
Age: 65
Posts: 41
Likes: 0
Received 0 Likes
on
0 Posts
The indication of sliding movement on that black tubular hinge fitting maybe left from the nylon type material, but I think it's reflection. Not sure
I flatly discounted the elongated holes at first, now I'm fairly sure they are - but they're also very wide! Then they've got a small washer which would have be compressed onto a partial void under the head of the bolt. What is going on with design like this? You can't have floppy slots to make adjustments on aircraft, or maybe the world has changed.
I flatly discounted the elongated holes at first, now I'm fairly sure they are - but they're also very wide! Then they've got a small washer which would have be compressed onto a partial void under the head of the bolt. What is going on with design like this? You can't have floppy slots to make adjustments on aircraft, or maybe the world has changed.
But yes. There is always one designer who wants to see all your calculations to prove that slots wont work to hold the wing on.
Join Date: Oct 2008
Location: Dorset
Posts: 150
Likes: 0
Received 0 Likes
on
0 Posts
I read recently that the Chinese will be looking for EASA certification of the C919. Do we really think if 2 C919s nosedive into the ground, followed by evidence of significant QC/QA issues (rudder bolts, doors falling off) that EASA would go anywhere near certifying it?
Obviously EASA won't do anything with Boeing types other than follow the FAA. What a sorry mess.
Obviously EASA won't do anything with Boeing types other than follow the FAA. What a sorry mess.
Psychophysiological entity
incompleteness. Interesting. However, this business of those washers with the two phosphor-bronze nuts.
If I was looking at that anew, I'd just say there is no chance those parts are designed to stop the guide fittings from sliding off the end - or even being bumped. The washers are too thin and the nuts are not strong - unless they're made of some super stuff I don't know about. But now a poster has mentioned one washer cupped up as the guide fitting was forced by. Airflow would have had no problem in doing that, but for normal operation, I'm left with wondering just what engineers have to do to remove the plug/door off the black rods. It seems odd to undo two pairs of nuts despite it being a rare occurrence - simply because the nuts are not of a material that I'd want to keep messing with.
that both gude fittings bump the end washer at exactly the same time, so you need up-down adjustability that the slots give.
Boeing Culpability
I have been reading this developing story, like so many of us I’m sure, with exquisite details gradually being extracted from the many photos, videos and commentary, laying bare the full magnitude of this potential catastrophe. Because this is, but for the grace of whoever, a catastrophe in all but the actual outcome.
Had the seats adjacent to the failed door been occupied, had there been a larger pressure differential (ie greater altitude), had the nearby passengers not been wearing their seatbelts, had the departed door hit the horizontal stabiliser, this door failure would undoubtedly have caused deaths. Horrible deaths for ejected passengers, and even worse had the whole plane been lost.
Just listening to Ed Pierson ref Post 580, he reminds us of the many other 737 Max “issues” that have come to light, both in service and also during production, it’s a long list. Coming back to this particular accident - not sure if that’s the right word – it’s becoming clear that the cause is yet another failure in manufacture or assembly. If critical bolts had not been tightened, or worse omitted completely . . . how could this happen? How on earth could this be missed? I come from a background of military service (engineering), as I’m sure many others of us have, and so clearly recall the absolute importance of checks, independent inspections, signatures and so on. It was drummed into us, repeatedly. And this was largely on jets carrying 1 or 2 persons, not commercial aircraft carrying hundreds.
I know it’s early days for the investigation but it seems to me the NTSB has been unusually open with its findings to date, and as others have said, it’s becoming pretty clear reading between the lines what their view is.
What is to become of Boeing, once the world’s greatest aircraft manufacturer? How many more issues are still out there, undiscovered? This matter has really got me thinking, perhaps even more so than the crashes. I or my family could have been there on that aircraft . . . I’m pretty sure that they would never want to fly again, and who could blame them. Suddenly the fuselage, so strong, warm, reassuring, brightly lit, TVs on, has got a massive hole in it, there’s a hurricane from nowhere and we’re staring into space with the ground 3 miles below us.
I wonder what, if any, penalty will be imposed on Boeing; presumably the NTSB or the FAA have the powers to impose large fines. Whether any financial sanctions on Boeing would change anything is debatable; it seems to me the company is pretty much beyond redemption.
Had the seats adjacent to the failed door been occupied, had there been a larger pressure differential (ie greater altitude), had the nearby passengers not been wearing their seatbelts, had the departed door hit the horizontal stabiliser, this door failure would undoubtedly have caused deaths. Horrible deaths for ejected passengers, and even worse had the whole plane been lost.
Just listening to Ed Pierson ref Post 580, he reminds us of the many other 737 Max “issues” that have come to light, both in service and also during production, it’s a long list. Coming back to this particular accident - not sure if that’s the right word – it’s becoming clear that the cause is yet another failure in manufacture or assembly. If critical bolts had not been tightened, or worse omitted completely . . . how could this happen? How on earth could this be missed? I come from a background of military service (engineering), as I’m sure many others of us have, and so clearly recall the absolute importance of checks, independent inspections, signatures and so on. It was drummed into us, repeatedly. And this was largely on jets carrying 1 or 2 persons, not commercial aircraft carrying hundreds.
I know it’s early days for the investigation but it seems to me the NTSB has been unusually open with its findings to date, and as others have said, it’s becoming pretty clear reading between the lines what their view is.
What is to become of Boeing, once the world’s greatest aircraft manufacturer? How many more issues are still out there, undiscovered? This matter has really got me thinking, perhaps even more so than the crashes. I or my family could have been there on that aircraft . . . I’m pretty sure that they would never want to fly again, and who could blame them. Suddenly the fuselage, so strong, warm, reassuring, brightly lit, TVs on, has got a massive hole in it, there’s a hurricane from nowhere and we’re staring into space with the ground 3 miles below us.
I wonder what, if any, penalty will be imposed on Boeing; presumably the NTSB or the FAA have the powers to impose large fines. Whether any financial sanctions on Boeing would change anything is debatable; it seems to me the company is pretty much beyond redemption.
Now that multiple loose bolts have been found during the mandated inspections, I would have expected the FAA to also order additional inspections for airframes with the regular emergency doors. Since they haven't done that (yet), there must be something specific about the installation process of the door plugs, I'd guess.
Something along the line of: "Emergency doors are provisionally installed by Spirit, then temporarily removed by Boeing to allow systems access (e.g. to connect sensor wiring) during final assembly. Replacement door plugs are provisionally installed by Spirit and should be temporarily removed by Boeing for final assembly, but this temporary removal was not done, because for a door plug no additional systems access is required." Highly speculative, I concur, but might the door plug have only been provisionally installed, period?
Something along the line of: "Emergency doors are provisionally installed by Spirit, then temporarily removed by Boeing to allow systems access (e.g. to connect sensor wiring) during final assembly. Replacement door plugs are provisionally installed by Spirit and should be temporarily removed by Boeing for final assembly, but this temporary removal was not done, because for a door plug no additional systems access is required." Highly speculative, I concur, but might the door plug have only been provisionally installed, period?
Last edited by xetroV; 10th Jan 2024 at 11:38. Reason: Typo
Join Date: Jan 2024
Location: UK
Posts: 47
Likes: 0
Received 0 Likes
on
0 Posts
OK, now that I can post images, these a couple of images that are available.
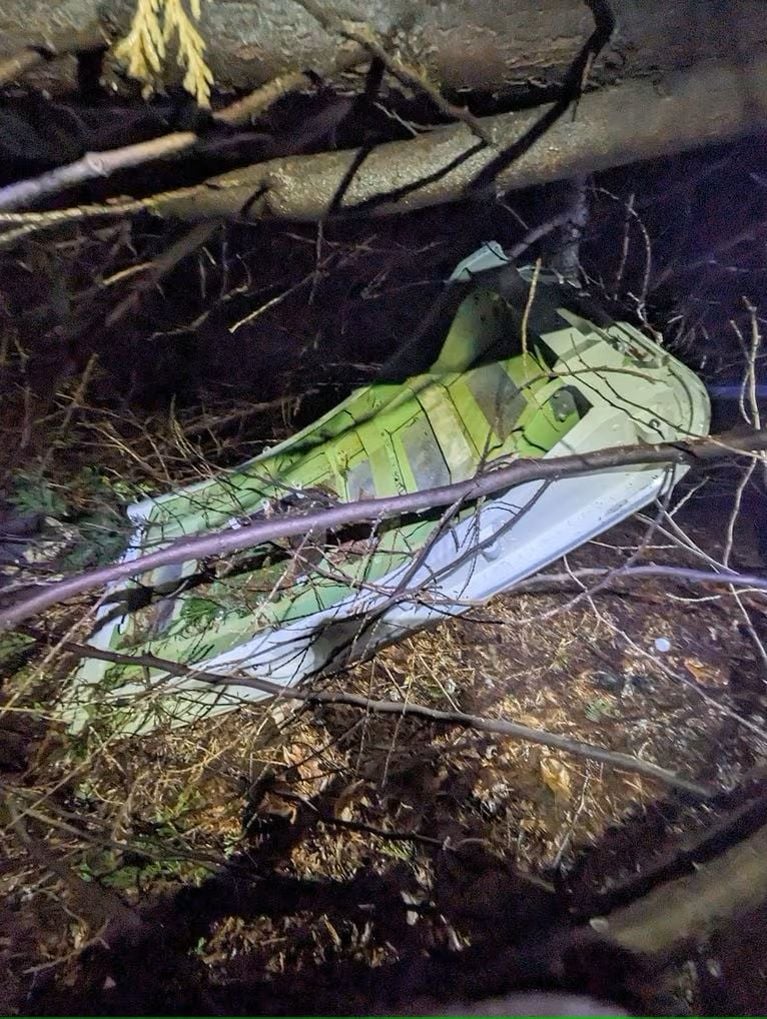
You can just about see what look like bushes that locate inside the slots in the rear green bracket. I have zoomed and image enhanced it in the next image. The bushes themselves are not completely clear but the shadow from them is.
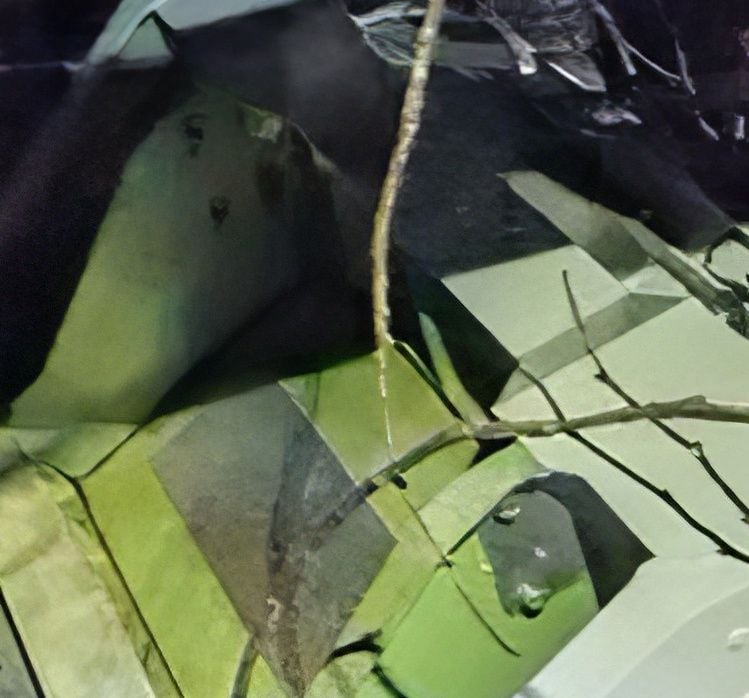
Another image shows the detail of where it was made.
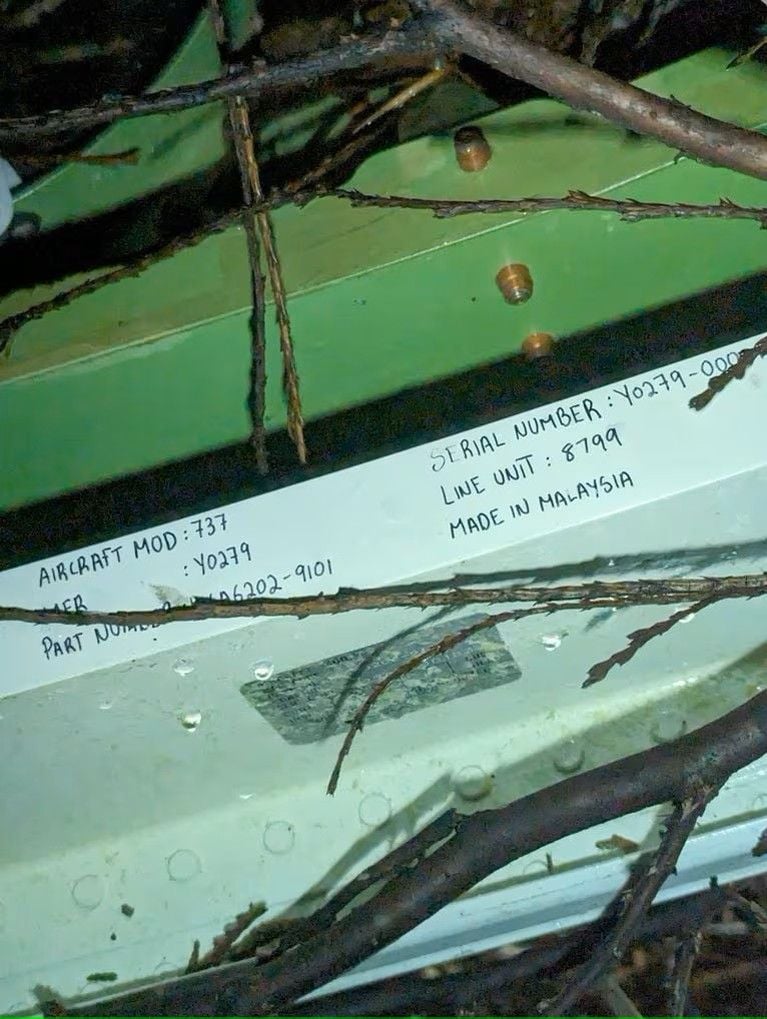
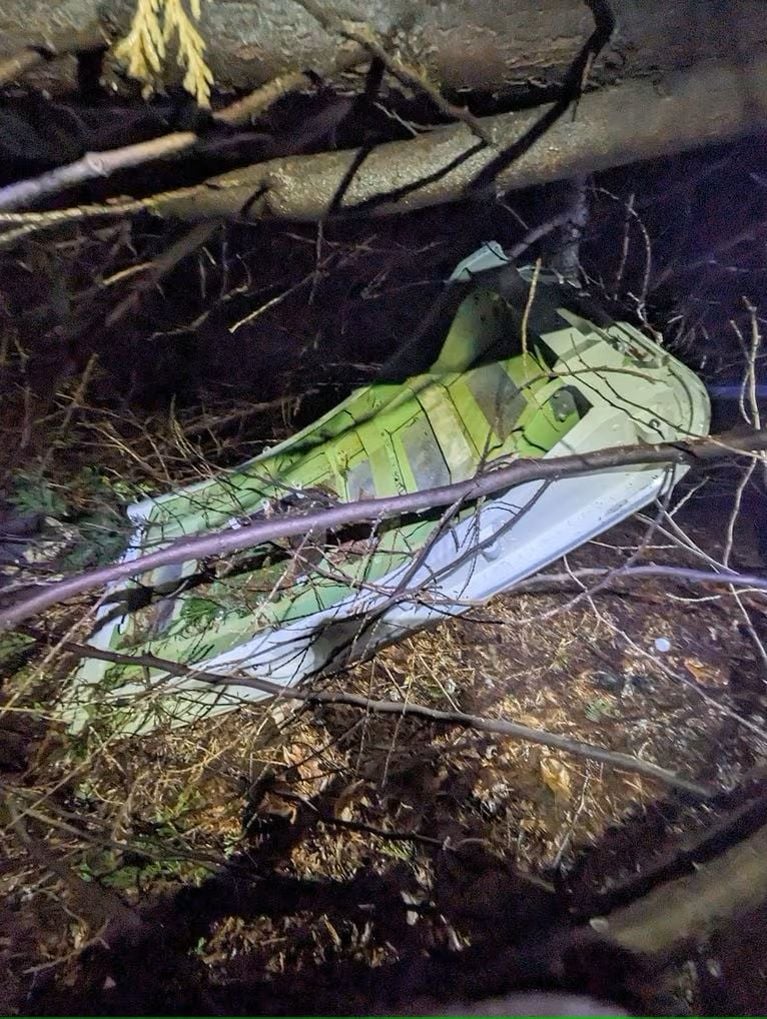
You can just about see what look like bushes that locate inside the slots in the rear green bracket. I have zoomed and image enhanced it in the next image. The bushes themselves are not completely clear but the shadow from them is.
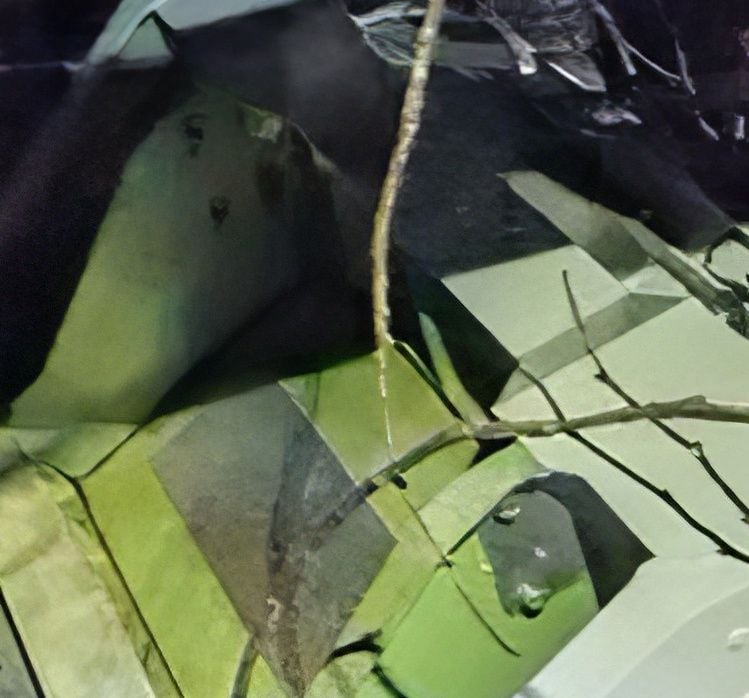
Another image shows the detail of where it was made.
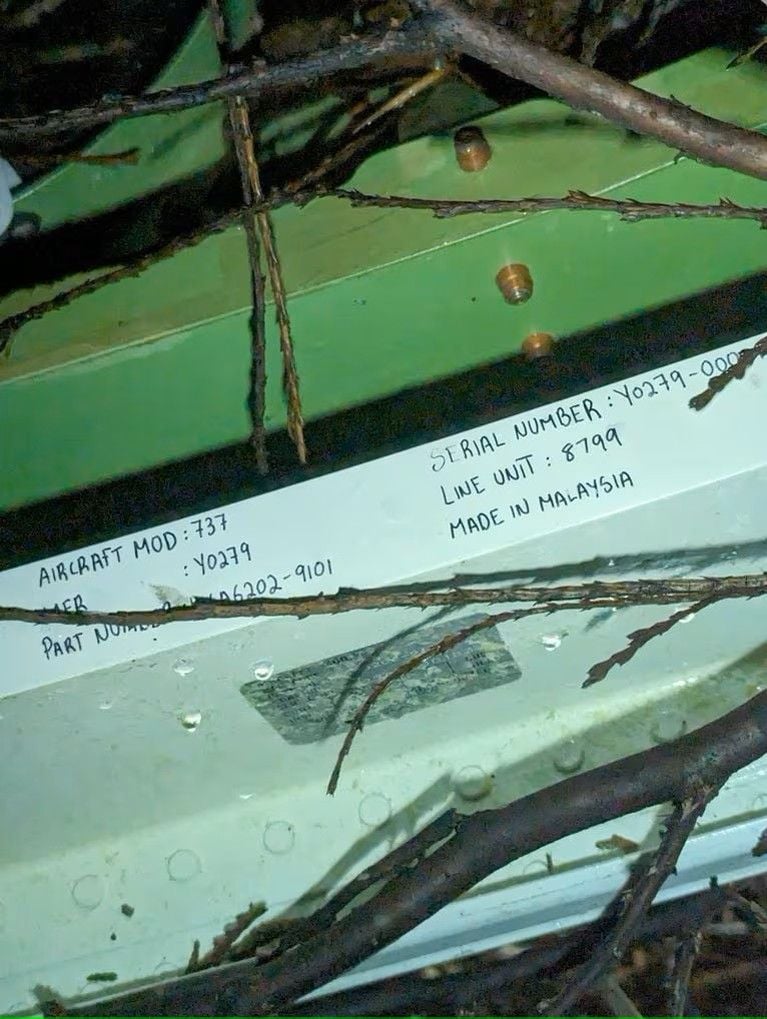
Join Date: Apr 2019
Location: Scotland
Posts: 8
Likes: 0
Received 0 Likes
on
0 Posts
Could it be that Spirit simply install the plugs essentially finger tight to seal the fuselage for transport, with the expectation that Boeing will be removing them and doing the final reinstall, but for some reason, that final reinstall has never happened?
Join Date: Jul 2021
Location: FL95
Posts: 32
Likes: 0
Received 0 Likes
on
0 Posts
Regardless of who first installed the plug or removed and reinstalled it during the course of production for whatever reason, I have the very strong opinion that the point in time to (re)inspect the installation and locking of all these bolts (not only the four locking bolts) hast to be just before that interior panel is installed the first and every consecutive time.
Join Date: Apr 2010
Location: Alexandria VA USA
Posts: 40
Likes: 0
Received 0 Likes
on
0 Posts
Mid-Door Door Options
The plug door is one of a number of options for the mid exit on the Max9. The standard configuration is an inactivated exit door with no windows. Other options are type I, type II, type III and type C exits depending on airline needs. Boeing makes it clear that if an airline ever intends to change the configuration of the exit, they should not order the plug option as the amount of rework needed to activate the exit is substantial and is effectively impractical. So swapping out plugs with a door is not a practical option.
I have been reading this developing story, like so many of us I’m sure, with exquisite details gradually being extracted from the many photos, videos and commentary, laying bare the full magnitude of this potential catastrophe. Because this is, but for the grace of whoever, a catastrophe in all but the actual outcome.
Had the seats adjacent to the failed door been occupied, had there been a larger pressure differential (ie greater altitude), had the nearby passengers not been wearing their seatbelts, had the departed door hit the horizontal stabiliser, this door failure would undoubtedly have caused deaths. Horrible deaths for ejected passengers, and even worse had the whole plane been lost.
Just listening to Ed Pierson ref Post 580, he reminds us of the many other 737 Max “issues” that have come to light, both in service and also during production, it’s a long list. Coming back to this particular accident - not sure if that’s the right word – it’s becoming clear that the cause is yet another failure in manufacture or assembly. If critical bolts had not been tightened, or worse omitted completely . . . how could this happen? How on earth could this be missed? I come from a background of military service (engineering), as I’m sure many others of us have, and so clearly recall the absolute importance of checks, independent inspections, signatures and so on. It was drummed into us, repeatedly. And this was largely on jets carrying 1 or 2 persons, not commercial aircraft carrying hundreds.
I know it’s early days for the investigation but it seems to me the NTSB has been unusually open with its findings to date, and as others have said, it’s becoming pretty clear reading between the lines what their view is.
What is to become of Boeing, once the world’s greatest aircraft manufacturer? How many more issues are still out there, undiscovered? This matter has really got me thinking, perhaps even more so than the crashes. I or my family could have been there on that aircraft . . . I’m pretty sure that they would never want to fly again, and who could blame them. Suddenly the fuselage, so strong, warm, reassuring, brightly lit, TVs on, has got a massive hole in it, there’s a hurricane from nowhere and we’re staring into space with the ground 3 miles below us.
I wonder what, if any, penalty will be imposed on Boeing; presumably the NTSB or the FAA have the powers to impose large fines. Whether any financial sanctions on Boeing would change anything is debatable; it seems to me the company is pretty much beyond redemption.
Had the seats adjacent to the failed door been occupied, had there been a larger pressure differential (ie greater altitude), had the nearby passengers not been wearing their seatbelts, had the departed door hit the horizontal stabiliser, this door failure would undoubtedly have caused deaths. Horrible deaths for ejected passengers, and even worse had the whole plane been lost.
Just listening to Ed Pierson ref Post 580, he reminds us of the many other 737 Max “issues” that have come to light, both in service and also during production, it’s a long list. Coming back to this particular accident - not sure if that’s the right word – it’s becoming clear that the cause is yet another failure in manufacture or assembly. If critical bolts had not been tightened, or worse omitted completely . . . how could this happen? How on earth could this be missed? I come from a background of military service (engineering), as I’m sure many others of us have, and so clearly recall the absolute importance of checks, independent inspections, signatures and so on. It was drummed into us, repeatedly. And this was largely on jets carrying 1 or 2 persons, not commercial aircraft carrying hundreds.
I know it’s early days for the investigation but it seems to me the NTSB has been unusually open with its findings to date, and as others have said, it’s becoming pretty clear reading between the lines what their view is.
What is to become of Boeing, once the world’s greatest aircraft manufacturer? How many more issues are still out there, undiscovered? This matter has really got me thinking, perhaps even more so than the crashes. I or my family could have been there on that aircraft . . . I’m pretty sure that they would never want to fly again, and who could blame them. Suddenly the fuselage, so strong, warm, reassuring, brightly lit, TVs on, has got a massive hole in it, there’s a hurricane from nowhere and we’re staring into space with the ground 3 miles below us.
I wonder what, if any, penalty will be imposed on Boeing; presumably the NTSB or the FAA have the powers to impose large fines. Whether any financial sanctions on Boeing would change anything is debatable; it seems to me the company is pretty much beyond redemption.
The plug door is one of a number of options for the mid exit on the Max9. The standard configuration is an inactivated exit door with no windows. Other options are type I, type II, type III and type C exits depending on airline needs. Boeing makes it clear that if an airline ever intends to change the configuration of the exit, they should not order the plug option as the amount of rework needed to activate the exit is substantial and is effectively impractical. So swapping out plugs with a door is not a practical option.
Re substituting a live door for a door plug, if that were to happen it would more likely be a lessor's decision when judged necessary for remarketing an aircraft, rather than an individual airline's.

Join Date: Jun 2023
Location: United States
Posts: 1
Likes: 0
Received 0 Likes
on
0 Posts
I am amazed that it was recognized (rightly so) that the retention bolt holding the Hinge Guide Fitting to the Hinge Shaft was important enough to require a catellated nut to prevent it from coming loose, and yet the Hinge Guide Fitting itself was being held to the door plug with only ordinary nuts and lock washers. This is akin to securing one important part to another using superglue, and yet the second part is secured to a third using only chewing gum (an oversimplification, but you get my drift).
Join Date: Apr 2010
Location: Alexandria VA USA
Posts: 40
Likes: 0
Received 0 Likes
on
0 Posts
Regardless of who first installed the plug or removed and reinstalled it during the course of production for whatever reason, I have the very strong opinion that the point in time to (re)inspect the installation and locking of all these bolts (not only the four locking bolts) hast to be just before that interior panel is installed the first and every consecutive time.

Shoddy workmanship by cheaper less trained workforce.
There is an old saying, If you think that quality is expensive try an accident.
On a longer time scale those accountant games destroy a company. For the accountant the trick is to move to another position or company faster, than he is hold responsible.
For pilots such a behavior does not work out, as mother nature holds them accountable within the next hours of their decision making. So this group here might have more difficulty to understand those decision processes.
There is an old saying, If you think that quality is expensive try an accident.
On a longer time scale those accountant games destroy a company. For the accountant the trick is to move to another position or company faster, than he is hold responsible.
For pilots such a behavior does not work out, as mother nature holds them accountable within the next hours of their decision making. So this group here might have more difficulty to understand those decision processes.
There are processes in place to trigger Line Replaceable Unit (LRU) tests in the event of an out of sequence part removal/replacement. But the normal production sequence work is tightly controlled. To make sure stuff gets done and checked off. This door problem could be the result of a process change between Boeing and Spirit where the initial plan was for Boeing to perform a fit and inspect test at the end of door removal/replacement. But when Boeing re-plans their work, that check fell through the cracks when the door removal was no longer done.
We had a few systems where we (Boeing) would re-run acceptance tests on received components. But there was pressure years ago to eliminate this kind of work. Since vendors performed it once and we rarely, if ever caught anything.
The only thing that I would suggest is that when Spirit ship fuselage with temporarily fit hardware, they include a big red sticker indicating the necessity to do a final adjustment and check. To even get the sticker off. Not much chance in losing the job planning paperwork then.
In the typical workflow for assembly:
There may be some overlapped responsibilities, particularly with the various groups overlooking to see that each stage has correctly interpreted the needs of previous and later stages.
It appears that the design is fine. All the parts that were apparently present seem to have functioned exactly as expected, ruling out a fundamental design flaw.
We don't know what QA specified and we don't know what QC recorded.
The biggest unknown is that assemblers don't always follow instructions. One would expect that this would be anticipated by QA to identify missed or incorrect steps and by QC for missed or incorrectly performed work. This is especially a problem when an assembly task is completed, verified, signed off by QC and then another assembler comes along to make some change they think is necessary, it isn't recorded, and there is no mechanism to go back to check work that should not have been done.
Personal experience - had an assembler, trying to help with a rotary seal leak problem, take an already inspected part with known surface roughness, and chuck it into a lathe to take a cutting pass because there were concerns a runout problem was contributing to leakage. Bad news, made it far worse. From 40 hours to failure down to about 5 hours. QA had the roughness requirement inspected; QC did the roughness check. All paperwork was in order. No one was watching the assembler re-work the part because reworking the part was not in any instructions. QA and QC were panicked. Good news, the assembler fessed up and the additional wear data point showed that the nominal roughness our vendor had chosen was too rough and not suitable. Polished to a high mirror finish and the wear problem went away.
So far I am assuming this is an honest mistake or simple incompetence.
Manufacturing engineering failed to provide control of all required steps. This might be "Remove and Replace door" without further detail.
QA might accept that as a sufficient instruction.
QC might look to see that there is a door in the hole and sign off.
None of that should be happening, but that door should still be in the plane and no other fasteners should be loose and rattling about, so here we are.
With excellent assemblers that would be enough. I've had the experience of working with a few, they got the engineering drawings and compared to the manufacturing engineering process and then called engineering asking WTF is happening due to discrepancies. We, uh, closed the loop with manufacturing engineering.
- Engineering designs the parts and how they are assembled.
- Manufacturing Engineering produces an assembly sequence, along with necessary tools and auxiliary materials (gloves, wipes, et al) to meet the engineering design.
- Quality Assurance (QA) Engineering validates that the manufacturing plan covers all the elements in the engineering design and adds checks to ensure the assembly is done correctly. For demanding applications it should also include checks to see that all auxiliary materials (gloves, wipes, et al) are accounted for to ensure none are left behind.
- Quality Control (QC) follows the checks that quality assurance has indicated are necessary to the assembly process.
There may be some overlapped responsibilities, particularly with the various groups overlooking to see that each stage has correctly interpreted the needs of previous and later stages.
It appears that the design is fine. All the parts that were apparently present seem to have functioned exactly as expected, ruling out a fundamental design flaw.
We don't know what QA specified and we don't know what QC recorded.
The biggest unknown is that assemblers don't always follow instructions. One would expect that this would be anticipated by QA to identify missed or incorrect steps and by QC for missed or incorrectly performed work. This is especially a problem when an assembly task is completed, verified, signed off by QC and then another assembler comes along to make some change they think is necessary, it isn't recorded, and there is no mechanism to go back to check work that should not have been done.
Personal experience - had an assembler, trying to help with a rotary seal leak problem, take an already inspected part with known surface roughness, and chuck it into a lathe to take a cutting pass because there were concerns a runout problem was contributing to leakage. Bad news, made it far worse. From 40 hours to failure down to about 5 hours. QA had the roughness requirement inspected; QC did the roughness check. All paperwork was in order. No one was watching the assembler re-work the part because reworking the part was not in any instructions. QA and QC were panicked. Good news, the assembler fessed up and the additional wear data point showed that the nominal roughness our vendor had chosen was too rough and not suitable. Polished to a high mirror finish and the wear problem went away.
So far I am assuming this is an honest mistake or simple incompetence.
Manufacturing engineering failed to provide control of all required steps. This might be "Remove and Replace door" without further detail.
QA might accept that as a sufficient instruction.
QC might look to see that there is a door in the hole and sign off.
None of that should be happening, but that door should still be in the plane and no other fasteners should be loose and rattling about, so here we are.
With excellent assemblers that would be enough. I've had the experience of working with a few, they got the engineering drawings and compared to the manufacturing engineering process and then called engineering asking WTF is happening due to discrepancies. We, uh, closed the loop with manufacturing engineering.
Genuine question! Is "production" very different to "in service maintenance" in terms of paperwork? I've not done the former but I assumed it was the same but .... assumptions can be dangerous. In all my time in Mil Comms/Radar I've lost track of the number of times I've had to remove/move some of my kit to give access to stuff behind for others to work on. Not only was the removal/moving of my kit detailed and signed for by me, my sig would also certify that I'd called up all the appropriate "refit work" for my kit including subsequent "inspection and testing" as appropriate - the inspector for my removal work also confirming I'd called up everything correctly for the refit task as part of their inspection before they signed my "removal" bit off. If I'd removed the main access panel, then there would be a panel refit task called up too but, often, I'd find the panel gone, that task being called under the main job. If Spirit "loosely fitted" the plugs doors as has been suggested, surely that would leave an open paperwork entry to "finally fit, inspect and test" the plug door which should travel with the fuselage? 

I don't know how they operate, but one would assume they use an electronic system rather than any physical paper copies, to keep tabs on and track work carried out across the manufacture and assembly of the fuselage to the state it is, prior to dispatch to Renton.
At the same time, you would also believe that Boeing should have a statement of work which details all aspects of the final assembly, including doors and interior fit and finish. I'd like to think (but can't assume) that there would be a pre-requisite for the interior plug door panel to ensure that the plug is fully installed and inspected prior to installation of the interior panel. It does sound like someone or some people somewhere didn't check and/or pencil whipped the inspection of said plug door and seemingly may have a habit of not checking.
Moderator
In the typical workflow for assembly:
- Engineering designs the parts and how they are assembled.
Sometimes the design engineers are so focused on the details of their task, the bigger picture of a failure opportunity goes un noticed. Sometimes shop floor workers are not encouraged to speak up when they see a possibility for failure, or they don't recognize a critical element as it passes before them. Aviation has a sad history of a decent airplane design, into which was accidentally designed a potential for unsafe configuration assembly, and inadequate warnings about this in the instructions, be they assembly, or maintenance.
There must be a continued willingness to invest the time to listen to everyone involved in the build of a plane, so workers become even more familiar with critical aspects, and designers learn to design out criticality in assembly/maintenance wherever possible. This whole "door" situation seems to point to a big miss in this broad discipline consideration. The opportunity to assemble in a weakness in the airplane went un noticed until the bang. A lot more "what if" questions needed to be asked during design and process development.
Quote:”Hot 'n' High
my experience… much more paperwork in production and the preceding production planning and the manufacturing engineering preceding that…
not exact …, but try think an order of magnitude more…
which gives an indication of how low Boeing appears to have sunk…
The ‘tearful’ video message of Mr Calhoun ( https://www.nu.nl/305470/video/emoti...737-max-9.html
https://www.nu.nl/305470/video/emoti...737-max-9.html )
shocked me deeply. All his statements were (sad pun …) open doors. Everything, everything he said were basics for people in aerospace. Last time I saw a manager say something like ‘that’ the professionals literally turned their backs on him and went to work. The brilliant cartoon of Matt may be more right than he imagines. This is not the Boeing the market knew and respected.
Genuine question! Is "production" very different to "in service maintenance" in terms of paperwork? I've not done the former but I assumed it was the same but .... assumptions can be dangerous.”
not exact …, but try think an order of magnitude more…
which gives an indication of how low Boeing appears to have sunk…
The ‘tearful’ video message of Mr Calhoun ( https://www.nu.nl/305470/video/emoti...737-max-9.html
https://www.nu.nl/305470/video/emoti...737-max-9.html )
shocked me deeply. All his statements were (sad pun …) open doors. Everything, everything he said were basics for people in aerospace. Last time I saw a manager say something like ‘that’ the professionals literally turned their backs on him and went to work. The brilliant cartoon of Matt may be more right than he imagines. This is not the Boeing the market knew and respected.
Last edited by A0283; 10th Jan 2024 at 16:41.