Was MCAS needed?
TNX, Bergerie....
I would really like to have FAA or the European cert folks explain how the Airbus FBW was certified, but the 737 had to meet some formula about control force versus AoA or Gee or......
We had older planes like the 727 that had a nasty problem if you got to a high AoA, just like the VooDoo I flew as a clueless yute. For some reason Boeing implemented the MCAS versus a pusher or some warning to meet the requirement of Part XXX of the rules. And then they screwed up the MCAS activation and repeated cycles and.... GASP.
Make no mistake. I would love to fly a new plane without any "help" from the electronics or even yaw and pitch dampeners we saw in early 60's. Their performance would not be economical nowadays for commercial use, and sadly lacking for military performance - we could be like that guy in early days of the "max" debacle that iterated the stick and rudder mantra. After UPT in USAF, I only flew one plane that had actual feedback from the moving control surfaces. And my first high preformance plane had zero feedback in the stick!! Did I adapt? Yep.
The Viper FBW was an amazing advance and helped improve range plus high performance maneuvering that did not require Chuck Yeager to yank and bank. Ditto for the first Bus planes with near- complete FBW versus cables, torque tubes, pulleys and such. We pilots adapted in a new minutes and did not need the "feel" from the elevator or aileron or rudder to do the task.
So I iterate the question to FAA and other agencies to look at and change the cert requirements.
I would really like to have FAA or the European cert folks explain how the Airbus FBW was certified, but the 737 had to meet some formula about control force versus AoA or Gee or......
We had older planes like the 727 that had a nasty problem if you got to a high AoA, just like the VooDoo I flew as a clueless yute. For some reason Boeing implemented the MCAS versus a pusher or some warning to meet the requirement of Part XXX of the rules. And then they screwed up the MCAS activation and repeated cycles and.... GASP.
Make no mistake. I would love to fly a new plane without any "help" from the electronics or even yaw and pitch dampeners we saw in early 60's. Their performance would not be economical nowadays for commercial use, and sadly lacking for military performance - we could be like that guy in early days of the "max" debacle that iterated the stick and rudder mantra. After UPT in USAF, I only flew one plane that had actual feedback from the moving control surfaces. And my first high preformance plane had zero feedback in the stick!! Did I adapt? Yep.
The Viper FBW was an amazing advance and helped improve range plus high performance maneuvering that did not require Chuck Yeager to yank and bank. Ditto for the first Bus planes with near- complete FBW versus cables, torque tubes, pulleys and such. We pilots adapted in a new minutes and did not need the "feel" from the elevator or aileron or rudder to do the task.
So I iterate the question to FAA and other agencies to look at and change the cert requirements.
Gums, no first hand knowledge, but I believe the A320 (and subsequent brand 'A' FBW) were certified via an "Alternate Method of Compliance" - AMOC. AMOCs get used quite a bit when new technology allows the aircraft to meet the 'intent' of the rule without meeting the 'letter' of the rule. They are quite common when new technology basically makes the letter of the rule obsolete. A classic example on the Boeing side was the implementation of EICAS - the regulations say that you need full time indications for all sorts of things, with EICAS those full time indications were suppressed unless the were not doing what they were supposed to (e.g. fuel shutoff valve - on older aircraft there were indicator lights that indicated valve position - with EICAS those lights were replaced by an EICAS message if the valve wasn't in the commanded position).
So in the case of the side stick controller, I believe Airbus took the position that the FBW flight control algorithms eliminated the need for the physical feedback.
So in the case of the side stick controller, I believe Airbus took the position that the FBW flight control algorithms eliminated the need for the physical feedback.
"Lets try and do it right from the beginning."
Hi gums,
'… how the 'bus got certified with no control feedback …'
The simple answer is that they rewrote the rules. Airbus chose not to use stick force as a cue for speed, instead argued the then novel view that an artificially stabilised and well protected aircraft, available with 'FBW', would provide an equivalent level of safety.
This was no simple task, it took many years of proposals supported by extensive research, simulation and experimental flights; effectively having to re-educate the aviation world (regulators).
The step change to an electrically controlled aircraft with computed protections did not come with past 'baggage' from previous products. The A300 broke into the commercial market, it had three crew until modern avionics, EFIS, digital technology, resulted in the Forward Facing Crew Cockpit (FFCC) -600, thence A310. This change was at the time of great focus on workload and the 2 crew cockpit, where all new aircraft were subject to workload evaluation B737, MD80, F28, BAe146, thus opportunity for radical change.
Copy of Bernhard Ziegler's paper linked below; this is a very thoughtful and far reaching note, which provides the background and much more. Sorry you need to read the pages in reverse, last page first, so concentrate !
https://www.dropbox.com/s/8uzkoc47lmgeo4w/
Bernard Ziegler - much maligned at the time, but time writes history.
Also, many other contributions; including John Wilson (copilot on Comet first flight), with the Advanced Flight Deck simulator (ended up in the Smithsonian in DC).
https://www.dropbox.com/s/dte4j6oade...09410.pdf?dl=0
Some of the gems from Ziegler:-
"… very careful not to use guidelines which are too broad and subject to too many interpretations, like: 'The man shall be kept in the loop', which is obvious but of no practical use, which is too specific or may prove to be harmful constraints with the evolution of man and machine (at least of his evolution of his culture and habits)."
"Crews got use to automation much faster, but designers moved forward even faster. A lesson in modesty in front of the immense inventiveness of the human being, and the army experts in human science who are now descending on our community, and should well meditate on this lesson. … as Socrates said, the only thing we know is that we know nothing." - and then the last pages on "Protections …… ", human reasoning, culture, human machine interface, task, free flight;
… … are you listening Boeing, FAA.
'… how the 'bus got certified with no control feedback …'
The simple answer is that they rewrote the rules. Airbus chose not to use stick force as a cue for speed, instead argued the then novel view that an artificially stabilised and well protected aircraft, available with 'FBW', would provide an equivalent level of safety.
This was no simple task, it took many years of proposals supported by extensive research, simulation and experimental flights; effectively having to re-educate the aviation world (regulators).
The step change to an electrically controlled aircraft with computed protections did not come with past 'baggage' from previous products. The A300 broke into the commercial market, it had three crew until modern avionics, EFIS, digital technology, resulted in the Forward Facing Crew Cockpit (FFCC) -600, thence A310. This change was at the time of great focus on workload and the 2 crew cockpit, where all new aircraft were subject to workload evaluation B737, MD80, F28, BAe146, thus opportunity for radical change.
Copy of Bernhard Ziegler's paper linked below; this is a very thoughtful and far reaching note, which provides the background and much more. Sorry you need to read the pages in reverse, last page first, so concentrate !
https://www.dropbox.com/s/8uzkoc47lmgeo4w/
Bernard Ziegler - much maligned at the time, but time writes history.
Also, many other contributions; including John Wilson (copilot on Comet first flight), with the Advanced Flight Deck simulator (ended up in the Smithsonian in DC).
https://www.dropbox.com/s/dte4j6oade...09410.pdf?dl=0
Some of the gems from Ziegler:-
"… very careful not to use guidelines which are too broad and subject to too many interpretations, like: 'The man shall be kept in the loop', which is obvious but of no practical use, which is too specific or may prove to be harmful constraints with the evolution of man and machine (at least of his evolution of his culture and habits)."
"Crews got use to automation much faster, but designers moved forward even faster. A lesson in modesty in front of the immense inventiveness of the human being, and the army experts in human science who are now descending on our community, and should well meditate on this lesson. … as Socrates said, the only thing we know is that we know nothing." - and then the last pages on "Protections …… ", human reasoning, culture, human machine interface, task, free flight;
… … are you listening Boeing, FAA.
Last edited by PEI_3721; 1st Feb 2021 at 21:43. Reason: Typo
Only half a speed-brake
.. no first hand knowledge,
[..]
I believe Airbus took the position that the FBW flight control algorithms eliminated the need for the physical feedback.
[..]
I believe Airbus took the position that the FBW flight control algorithms eliminated the need for the physical feedback.
One imagines it could have been enjoyable to implement. The stick is spring-loaded towards the neutral and thus provides closed haptic loop how much the pilot is demanding. All the engineers needed to do after flight testing the aerodynamic behaviour was to "gear" their algorithms properly so that the plane would respond to deflections on the control any particular way that may have been required.
Yet you can't take Chicago out of the girl.
Sounds good fdr,
BUT MCAS does not operate with flaps extended as I understand things. So then, do what you like with the flappery, it matters not.
A simple old engineer like me sees the easiest and best fix as small strakes on the aft fuselage set to zero incidence in the CRZ case. Now they cost a bit of wetted area and maybe a bit of extra drag on CLB coz the strakes do not align with the streamlines. However it is a simple once for all fix with no failure case. Never mind this software stuff, KISS.
BUT MCAS does not operate with flaps extended as I understand things. So then, do what you like with the flappery, it matters not.
A simple old engineer like me sees the easiest and best fix as small strakes on the aft fuselage set to zero incidence in the CRZ case. Now they cost a bit of wetted area and maybe a bit of extra drag on CLB coz the strakes do not align with the streamlines. However it is a simple once for all fix with no failure case. Never mind this software stuff, KISS.
The SFC is around 0:35 for the older blenders at SL, going to about 0.65 at cruise, and the new biggly built versions of the TFE731, the GENX etc are about 20% better. but, still, drop off at altitude. Why? cuz, the fan is a fixed pitch prop. yes, it changes the inflow velocity, but it is fixed pitch, and so the faster y'all go, the more turbojet you end up relying on (residual thrust) you still get the pleasure of the blade drag. If only there was a way of altering Cl vs Cd at static and high-speed conditions. And indeed there is. How that can be done is in a dumpster load of papers at ARC, NTRS, DLR etc, but as far as I am aware, it has only been tested once, on a really daggy JT15D-1A which was less than enjoyable to work on, and we only got around to doing the static runs. The prop mod stuff though we have flown since 1994, and that was fun in its own rights. turns out there is a philosophical question on the simple calculation of efficiency, otherwise, it is hard to get a 20% improvement in thrust output from a prop that is P=po/Pi= 85%. The static test of the JT15 got a marginal increase in efficiency for the thrust output, but it did put out 30% more thrust at 100% N1, while remarkably remaining within T5 limits. It put out the normal thrust at 94% so that wasn't a bad thing. I digress.
Miller time...
An angle grinder and some velcro would have removed the requirement for MCAS.
fdr, thank you for the extensive background.
Re 'angle grinder' fixes. One of the first western public conferences where TsAGI presented a paper on high alpha aerodynamics. - In answer to a question on their approach to strakes re nose slice, why some aircraft could perform 'cobra' manoeuvres (SU27) vs those requiring extensive theoretical development (F18); 'if a particular aircraft had a problem then change the nose cone until one was found which did not roll off'. A lesson in practicality.
EASA neatly concludes the certification need for MCAS:-
"MCAS has been established to play only a limited role in augmenting the stability and stall characteristics of the aircraft in certain conditions. … needed to ensure the stability margins that make the aircraft fully compliant to the applicable regulations on stall demonstration and pitch control characteristics. This explains its inclusion in the original 737 MAX design.
These stability margins are required by regulation in order to support the flight crew handling of the aircraft during certain manoeuvres such as approach to stall …
MCAS was needed to provide full compliance but also that the loss of this function does not preclude the safe flight and landing of the aircraft; i.e. the 737 MAX remains stable following the loss of the MCAS function."
Boeing 737 MAX Return to Service Report
https://www.easa.europa.eu/sites/def...ice_Report.pdf
Re 'angle grinder' fixes. One of the first western public conferences where TsAGI presented a paper on high alpha aerodynamics. - In answer to a question on their approach to strakes re nose slice, why some aircraft could perform 'cobra' manoeuvres (SU27) vs those requiring extensive theoretical development (F18); 'if a particular aircraft had a problem then change the nose cone until one was found which did not roll off'. A lesson in practicality.
EASA neatly concludes the certification need for MCAS:-
"MCAS has been established to play only a limited role in augmenting the stability and stall characteristics of the aircraft in certain conditions. … needed to ensure the stability margins that make the aircraft fully compliant to the applicable regulations on stall demonstration and pitch control characteristics. This explains its inclusion in the original 737 MAX design.
These stability margins are required by regulation in order to support the flight crew handling of the aircraft during certain manoeuvres such as approach to stall …
MCAS was needed to provide full compliance but also that the loss of this function does not preclude the safe flight and landing of the aircraft; i.e. the 737 MAX remains stable following the loss of the MCAS function."
Boeing 737 MAX Return to Service Report
https://www.easa.europa.eu/sites/def...ice_Report.pdf
The 16 was more stablerer, the nose is not as near to circular. The F-35 nose is much more stable, but even there, it could have done away with the short radius upper curve of the cross-section, which would have given more lift at the nose which could be an issue for the pitching moment but would be extremely stable at high alpha. Pyotr Ufimtsev's work may have led to a preference for roundy upper shoulders when run through better supercomputers, otherwise, the 117 style edge would work well, upside down. fluids don't care that much about the front bits they are very interested in the rear area. That point which is pretty basic seems to be lost in almost all car design, up through F-1, and to an extent in lots of light aircraft design,
[Funny thing is we have smart design of stealth structures and we use dumb designs of anechoics]
PS: F-15 nose slicing was also an issue identified in flight, similar deal to -18, 16 was a little better, flow control on the 16 was related to advanced manoeuvering more than stopping an instability, but they are similar in nature and the cures are similar too. jet blowing avoids the impact on target RCS but is a pain to maintain.
PPS: the fact that NASA has an F18 as the HARV probably added some emphasis to it being the poster child for CFD in the early 90s, and the cracking of the vertical stabs that started to become expensive, along with the tail bits from the vortex interaction from the LEX. neat fix for the classic F18s, cleaner with the E/Fs, but it took away the charm of the design.
Last edited by fdr; 2nd Feb 2021 at 11:50. Reason: PPS
Thread Starter
Thank you fdr, Gums, PEI 3721 and tdracer.
I started this thread because, having read the EASA report, I really did wonder why Boeing decided to use MCAS. I can see its advantages for Boeing as 'a simple extension of the STS', but as we know, without triple AoA sensors it was vulnerable to a failure. Surely simpler solutions would have been a stick nudger as required by the UK CAA on the 747 (had that been fitted to the MAX it would not have required any extra crew training) or some aerodynamic device like the 'angle grinder' devices you have mentioned.
But I guess Boeing decided that the MCAS was cheaper.
And, as hinted to by EASA and by some of you, was it really necessary to meet a regulatory requirement on stick force gradient when the aircraft may have been perfectly safe without any of these fixes?
I started this thread because, having read the EASA report, I really did wonder why Boeing decided to use MCAS. I can see its advantages for Boeing as 'a simple extension of the STS', but as we know, without triple AoA sensors it was vulnerable to a failure. Surely simpler solutions would have been a stick nudger as required by the UK CAA on the 747 (had that been fitted to the MAX it would not have required any extra crew training) or some aerodynamic device like the 'angle grinder' devices you have mentioned.
But I guess Boeing decided that the MCAS was cheaper.
And, as hinted to by EASA and by some of you, was it really necessary to meet a regulatory requirement on stick force gradient when the aircraft may have been perfectly safe without any of these fixes?
Hey fdr,
Thanks for the learned explanations of this stuff.
I'll work through it tomorrow before beer o'clock and after I revise some old aero notes. Been a long time since I had to think much about this stuff!!
Thanks for the learned explanations of this stuff.
I'll work through it tomorrow before beer o'clock and after I revise some old aero notes. Been a long time since I had to think much about this stuff!!
FDR
Re
They did try that - or at least they tried revising the leading edge stall strip. They also tried modifying the leading edge vortilons and a revised wing vortex generator pattern but none could be made to work so they borrowed MCAS from the 767 tanker.
Re
An angle grinder and some velcro would have removed the requirement for MCAS.
LE stall strips generally act to give a reliable buffet signal to the driver from vortex impingement on the stabilizer, while that is nice to have, they generally don't act on altering the stall event. They can, but if you look where they are located, they are not used for that purpose.
Vortilons are great at stopping the spanwise flow, which has it's benefits but not to the issue of the nacelle Cm effect. The NG adopted them and they were great, along with the revised aileron design in stopping the 737's aileron vibration at high Mach (relatively...) Wing VGs are not going to do a whole lot to alter the Cm issue either, not if the flow is already happily attached, and the Cm non-linearity starts before there is separation on the outboard sections. The 737 aileron effectiveness in high AOA is not too bad, so long as the slats are rigged symmetrically. The suto-slat function could have avoided the MCAS, it is scheduled at an AOA however, so would have needed to have some reliability, I can't recall if it has dual sensing or not, its a few years since I last stalled a 737.
Have a look at where the stall strips are located and where that is relative to the outboard tips of the stab.(other than the early 737s which had a strip on the Krueger which was a curious thing to have) The neat thing about fluid flow is that almost everything you do will work to some extent. A B52's stunning cheese grater array, like the Gloster Javelin, The Lear's various forms except for John Raisbecks beautiful MK II wing... The Avanti's wing... lots of fluid getting pushed around there... the B707, B757, B767, the 737 tail area, a fence on the 727, hawker vortilon & VGs...... , the outboard wing on the classics, the mid-wing on the classic, and NG, the 787... the MD80 vortilon, the Hunter and F4s dog tooth, notches, MiG15, 17, 19, 21 fences, (not great help on the 15, good on the 21 though) etc and pretty much everything else out there. The EFA Typhoid drools a notch inboard.... a bit like a 330. The A-10 has some stuff going on out there, looks suspiciously like aileron effectiveness related. Gee whizzes have lots of cheese slicers on the wing outboard... which is aileron buzz related I guess. Of all of those, the P168 is curious, the cuff on a beautiful little rocket seems out of place, about like a Ferrari with a bull bar. I digress. Pretty clean wings came out on the 747, and on the A330-340-350-380. Boeing excelled with the 747, but Airbus really did well on their wing design (making up for the A300Bs wing/aileron... woof).
Vortilons are great at stopping the spanwise flow, which has it's benefits but not to the issue of the nacelle Cm effect. The NG adopted them and they were great, along with the revised aileron design in stopping the 737's aileron vibration at high Mach (relatively...) Wing VGs are not going to do a whole lot to alter the Cm issue either, not if the flow is already happily attached, and the Cm non-linearity starts before there is separation on the outboard sections. The 737 aileron effectiveness in high AOA is not too bad, so long as the slats are rigged symmetrically. The suto-slat function could have avoided the MCAS, it is scheduled at an AOA however, so would have needed to have some reliability, I can't recall if it has dual sensing or not, its a few years since I last stalled a 737.
Have a look at where the stall strips are located and where that is relative to the outboard tips of the stab.(other than the early 737s which had a strip on the Krueger which was a curious thing to have) The neat thing about fluid flow is that almost everything you do will work to some extent. A B52's stunning cheese grater array, like the Gloster Javelin, The Lear's various forms except for John Raisbecks beautiful MK II wing... The Avanti's wing... lots of fluid getting pushed around there... the B707, B757, B767, the 737 tail area, a fence on the 727, hawker vortilon & VGs...... , the outboard wing on the classics, the mid-wing on the classic, and NG, the 787... the MD80 vortilon, the Hunter and F4s dog tooth, notches, MiG15, 17, 19, 21 fences, (not great help on the 15, good on the 21 though) etc and pretty much everything else out there. The EFA Typhoid drools a notch inboard.... a bit like a 330. The A-10 has some stuff going on out there, looks suspiciously like aileron effectiveness related. Gee whizzes have lots of cheese slicers on the wing outboard... which is aileron buzz related I guess. Of all of those, the P168 is curious, the cuff on a beautiful little rocket seems out of place, about like a Ferrari with a bull bar. I digress. Pretty clean wings came out on the 747, and on the A330-340-350-380. Boeing excelled with the 747, but Airbus really did well on their wing design (making up for the A300Bs wing/aileron... woof).
Last edited by fdr; 2nd Feb 2021 at 11:46.
Only half a speed-brake
I think it links to your conclusion on the (lack of) other fixes apart from MCAS. They seem to have honestly chosen a solution that was readily available, required less R&D and cost as little as necessary, all that without penalizing performance As much as the internet likes to ridicule that decision, showboating and all [this thread is a great exception!!], what's being called clearly obvious in the laymen media sphere was for sure well known and thoroughly considered by the dedicated professionals yet AFTERWARDS they chose MCAS. No matter the pathetic killer gremlin MCAS 1.0 which was born later, the initial choice of picking the MCAS tool was a fair one. If it would be done again, there's absolutely no presentable evidence to deny that particular path. And as matter of fact that's what happened: The proper and agreed solution to control forces is MCAS 2.0 which is all that 1.0 wasn't and at the same time the exact thing they originally planned for.
Without getting carried away too far: Imagine the trailing edge modification had been chosen resulting in all the super critical geeky cool effects fdr explains. BUT THEN during the actual design and implementation aviation reality would be abused same as with MCAS 1.0. Such as failing to do ice contamination test and the additional load stress calculations. Resulting in flaps detaching a few years down the road - with crew performance same as on the second crash day, the death toll would have been identical.
Trying to say that selecting what is now disclosed and known as MCAS as a tool cannot be faulted. With extreme probability, it was well-reviewed against all the other options and chosen maybe even as a win-win.
Cons of the other suggestions, as picked up over the forums here1:
strakes
- Very badly predictable in the design stage. You do not know what it does unless you flight test it. Single engine, side slipped flight at high AoA with ice on them and only one gets a hot air blast the exhaust,? A/C departs controlled flight to the side. Unpredictable risk on the development scope and amount of effort. fdr's stories on fast jet nose section design speak volumes.
- Adding weight and drag penalties, no matter how small amounts, does count (for some). The largest customers do care, rightfully or not their Excels are sharp and furious.
- Extra maintenance requirement for inspections over the lifetime of the airframe. Cost, costs, costs... customer choice, customer choice, customer choice
- Increased risk of ramp collisions. IDK but any object with mass has its own gravity and on the ramp EVERYTHING gets hit eventually. New repair schedule, new DDG items... oh.
trailing edge mod on the wing or elevators
- Completely out of scope, design frozen, signed and dusted for. The simple little issue needs a simple little solution. Constant re-tweaking kills projects like nothing else. And why touch the wing unless you absolutely have to? You don't. Sure, for the MAX+ at 2028 it will be done.
stick pusher AS WELL AS artificial feel unit mod
- certification review of the F/CTL system
- training required, commonality tanked
- extra weight
- messing with what works never goes without problems. Probably best they did not - geez these guys failed to connect the AoA light and could not see MCAS acting on the sole most powerful aerodynamic control is class A critical item like no other.
MCAS
- a software routine, simple to model and dry test
- easy to update and change later across the global fleet
- does what needs to be done
- does not involve touching any of the existing systems that have been time-tested to perfection
- no extra hardware
- no additional training as it really is just an additional spinning mode for what the STS actually is - an autonomous THS compensator.
Yet, after all, the very same teams who understandably chose the proper way out is with MCAS against the hard options, could not avail themselves to just doing anything but simply admit a less than perfect force characteristics on the control column. The EASA boss statement is inconclusive. Various otherwise dangerous aeroplanes (not the case of MAX) can be flown safely if you know how to do it.
Copy of Bernhard Ziegler's paper linked below; this is a very thoughtful and far reaching note, which provides the background and much more. Sorry you need to read the pages in reverse, last page first, so concentrate !
https://www.dropbox.com/s/8uzkoc47lmgeo4w/
Bernard Ziegler - much maligned at the time, but time writes history.
Also, many other contributions; including John Wilson (copilot on Comet first flight), with the Advanced Flight Deck simulator (ended up in the Smithsonian in DC).
https://www.dropbox.com/s/dte4j6oade...09410.pdf?dl=0
Some of the gems from Ziegler:-
"… very careful not to use guidelines which are too broad and subject to too many interpretations, like: 'The man shall be kept in the loop', which is obvious but of no practical use, which is too specific or may prove to be harmful constraints with the evolution of man and machine (at least of his evolution of his culture and habits)."
"Crews got use to automation much faster, but designers moved forward even faster. A lesson in modesty in front of the immense inventiveness of the human being, and the army experts in human science who are now descending on our community, and should well meditate on this lesson. … as Socrates said, the only thing we know is that we know nothing." - and then the last pages on "Protections …… ", human reasoning, culture, human machine interface, task, free flight;
… … are you listening Boeing, FAA.
'… why did Boeing go through with MCAS and not just simply declaring the behaviour and asking for relief? '
This is likely to be the financial 'dazzle' of commonality with previous versions.
The MAX might have met the requirements, but it may not have been sufficiently similar to a 737' for the minimum-change training objective (valued at $1M / SW aircraft).
'Angle Grinder devices, or strakes'
An example; https://www.rafmuseum.org.uk/researc...-demonstrator/
The the leading edge extensions and mass location deliberately destabilised the aircraft.
The experimental control system provided the basis of a quadruplex 'FBW' poof of design and certification (*) for future military aircraft - Typhoon, and for the B777 flight controls, but with a Boeing (stick-force) algorithm.
The 737 Max may not have warranted this level of design, but did require equivalent certification. The dominating bias was commerce - simple low cost, quick, time = money, and 'the same as previous 737s'.
Conversely, all to often we seek to use the latest technology; e.g. use Artificial Intelligence, but not always understanding the need for it.
Instead of AI we need 'IA', Intelligent Assistance.
With hindsight, MCAS was designed to assist, but it wasn't intelligent.
* for the technophobes - https://apps.dtic.mil/dtic/tr/fulltext/u2/p002713.pdf
fdr, yes please - see pm.
Clean wing - you overlook the 146/RJ. Not a VG in sight; a stall breaker to ensure that the inboard wing stalled before the tip. Same aero team as the early Airbus wings.
This is likely to be the financial 'dazzle' of commonality with previous versions.
The MAX might have met the requirements, but it may not have been sufficiently similar to a 737' for the minimum-change training objective (valued at $1M / SW aircraft).
'Angle Grinder devices, or strakes'
An example; https://www.rafmuseum.org.uk/researc...-demonstrator/
The the leading edge extensions and mass location deliberately destabilised the aircraft.
The experimental control system provided the basis of a quadruplex 'FBW' poof of design and certification (*) for future military aircraft - Typhoon, and for the B777 flight controls, but with a Boeing (stick-force) algorithm.
The 737 Max may not have warranted this level of design, but did require equivalent certification. The dominating bias was commerce - simple low cost, quick, time = money, and 'the same as previous 737s'.
Conversely, all to often we seek to use the latest technology; e.g. use Artificial Intelligence, but not always understanding the need for it.
Instead of AI we need 'IA', Intelligent Assistance.
With hindsight, MCAS was designed to assist, but it wasn't intelligent.
* for the technophobes - https://apps.dtic.mil/dtic/tr/fulltext/u2/p002713.pdf
fdr, yes please - see pm.
Clean wing - you overlook the 146/RJ. Not a VG in sight; a stall breaker to ensure that the inboard wing stalled before the tip. Same aero team as the early Airbus wings.
Last edited by PEI_3721; 2nd Feb 2021 at 14:21. Reason: Typo
Thanks to Bergerie for hosting this thread on the subject. I was disappointed when the Mods froze all the 737 threads, as I am a curious type and wanted to learn about the development of the MCAS. I unnerstan freezing the main forum stuff when discussion got away from the technical and factual aspects of the two crashes. But I sought refuge here on Tech Log. My AF447 education in the Tech Log was a joy, and I hope I contributed just a bit to folks' understanding of FBW.
I especially appreciate the contributions here by FDR, PEI and Detent. Then we got an occasional input from Tdracer, that offered inside looks at Big B. At the outset it seems we had a "mole" in Boeing that contributed to our technical discussions and may still be around or was found out by the company and silenced.
As with some here, my academic aero study was from the 60's, then I learned new stuff flying brand new planes until the mid-80's. Who thot of relaxed static stability back then, or vortex contributions we see with strakes and LEX and.....
So I salute all of you and will try to lurk more.
I especially appreciate the contributions here by FDR, PEI and Detent. Then we got an occasional input from Tdracer, that offered inside looks at Big B. At the outset it seems we had a "mole" in Boeing that contributed to our technical discussions and may still be around or was found out by the company and silenced.
As with some here, my academic aero study was from the 60's, then I learned new stuff flying brand new planes until the mid-80's. Who thot of relaxed static stability back then, or vortex contributions we see with strakes and LEX and.....
So I salute all of you and will try to lurk more.
Going to the feds with a waiver request would have been embarrassing, but probably not pushed back by the feds, maybe. There are some good guys in the ACO/ transport office, but that horse has bolted. The aircraft still has to be acceptable within the guidelines of 25.173 by methods per 25.175 AC25.07 (Rev D at present) has a couple of interesting graphs on that matter. EASA and the associated comments suggest that the non-linearities were not substantial, but without the flight data and force measurements how close that was to being waivable is not quantified. The manner by which vortex interaction occurs would suggest that it was not a severe non linearity. IMHO.
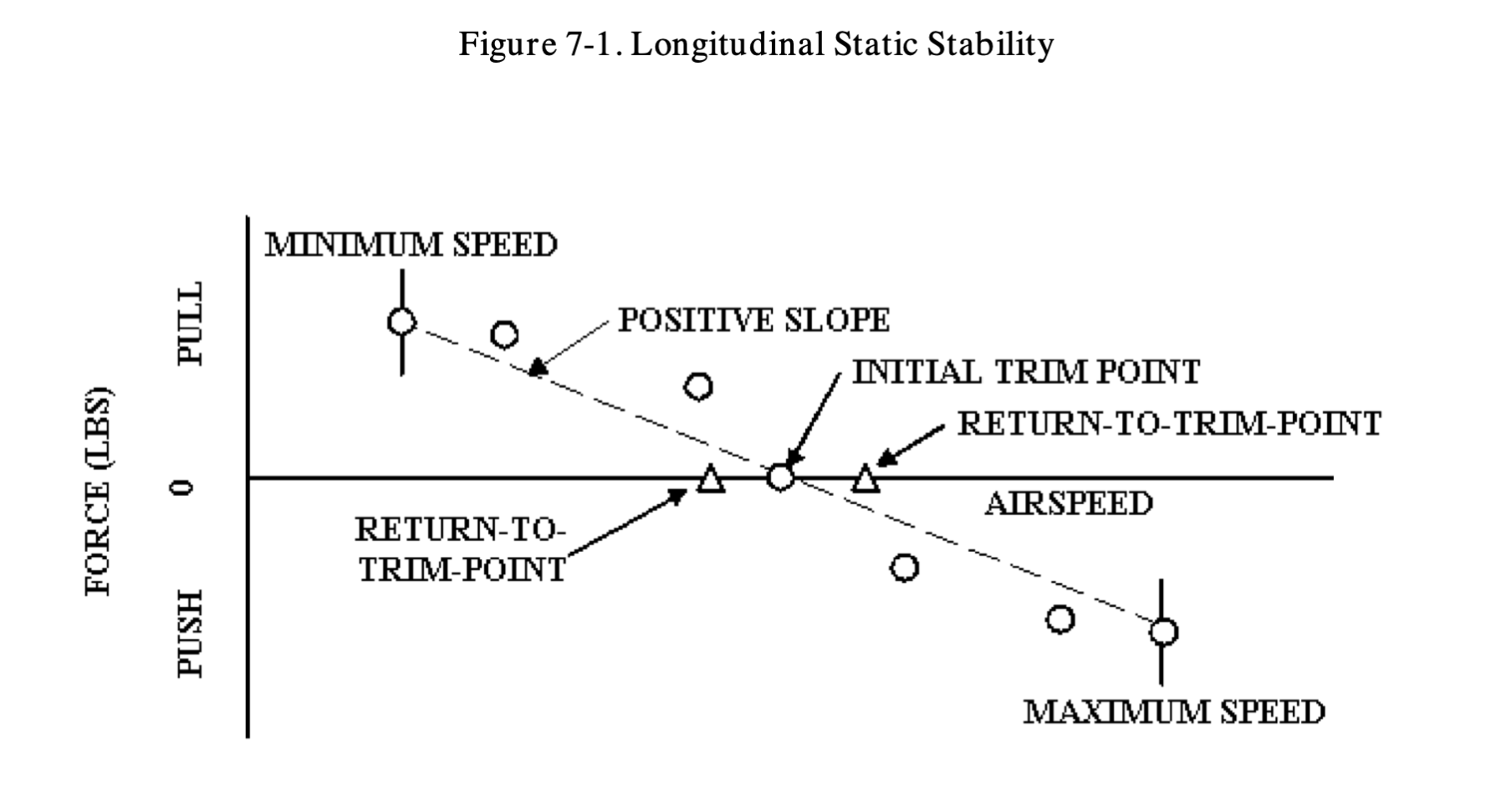
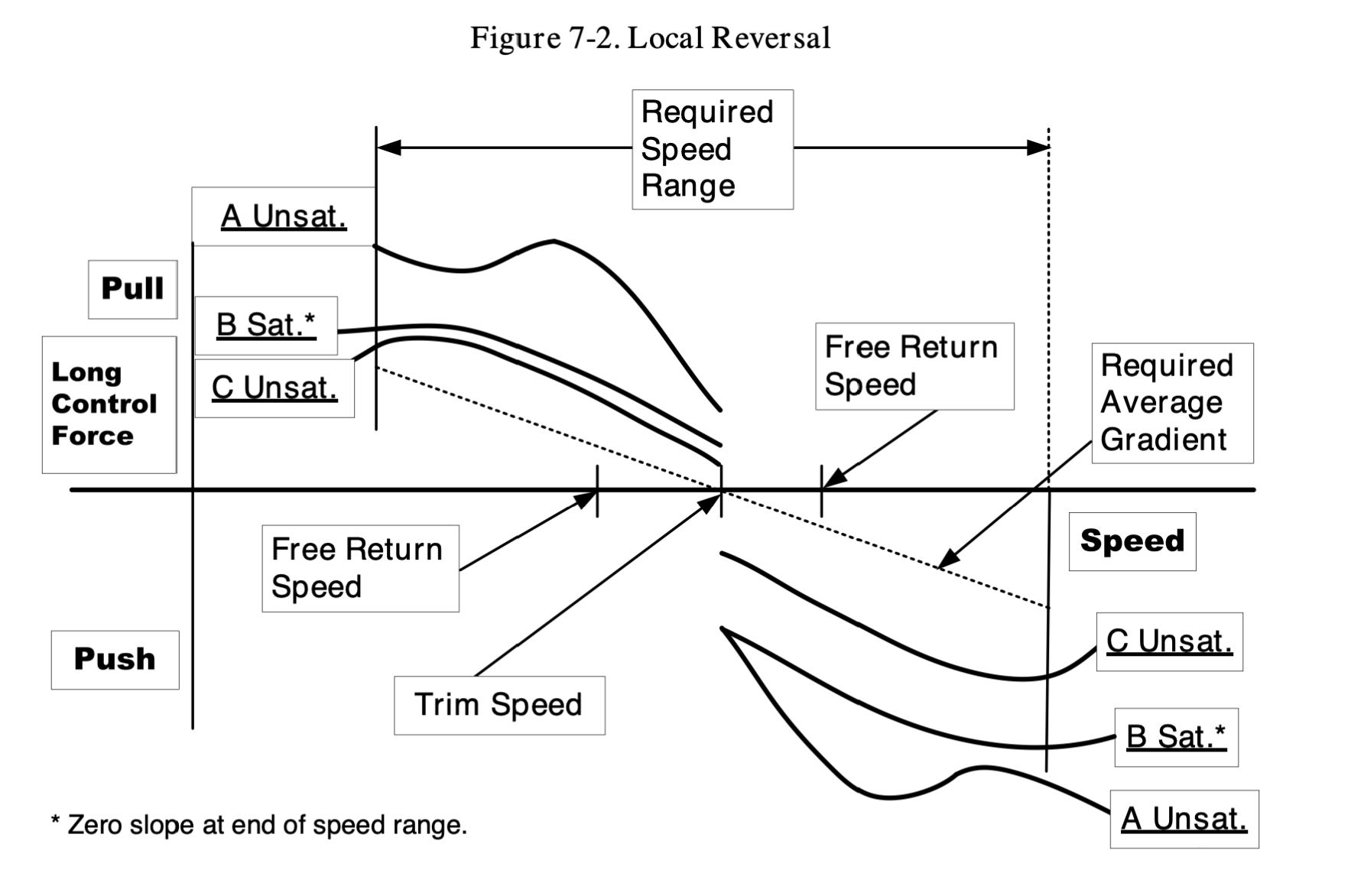
I think it links to your conclusion on the (lack of) other fixes apart from MCAS. They seem to have honestly chosen a solution that was readily available, required less R&D and cost as little as necessary, all that without penalizing performance As much as the internet likes to ridicule that decision, showboating and all [this thread is a great exception!!], what's being called clearly obvious in the laymen media sphere was for sure well known and thoroughly considered by the dedicated professionals yet AFTERWARDS they chose MCAS. No matter the pathetic killer gremlin MCAS 1.0 which was born later, the initial choice of picking the MCAS tool was a fair one. If it would be done again, there's absolutely no presentable evidence to deny that particular path. And as matter of fact that's what happened: The proper and agreed solution to control forces is MCAS 2.0 which is all that 1.0 wasn't and at the same time the exact thing they originally planned for.
Without getting carried away too far: Imagine the trailing edge modification had been chosen resulting in all the super critical geeky cool effects fdr explains. BUT THEN during the actual design and implementation aviation reality would be abused same as with MCAS 1.0. Such as failing to do ice contamination test and the additional load stress calculations. Resulting in flaps detaching a few years down the road - with crew performance same as on the second crash day, the death toll would have been identical.
Trying to say that selecting what is now disclosed and known as MCAS as a tool cannot be faulted. With extreme probability, it was well-reviewed against all the other options and chosen maybe even as a win-win.
.
Mmmm’kay,
Nothing ever goes wrong with software changes.
- Like the PIO of the JAS 39 Gripen,
- Like the Mars climate orbiter,
- Like Ariane V,
- Bitcoins hack,
- Soviet Gas line explosion,
- The Patriot Missile in KSA,
- Airbus OEB 117
- Nissans airbags
- HSBC, and others customer lockouts.
And,
- just for stamps the near start of WW III on 26 SEP 1983, avoided by the actions of a single, fallible human, Stanislav Yevgrafovich Petrov. We can chat about software, facebook, twitter and the rest of the inane stuff of this century because one man was smart enough to avoid Armageddon. On that day, at that time, I was sitting above a Yankee I, in the middle of nowhere.
Yup, computers, to mess up spectacularly and end the world takes software code.
Last edited by fdr; 2nd Feb 2021 at 14:57.
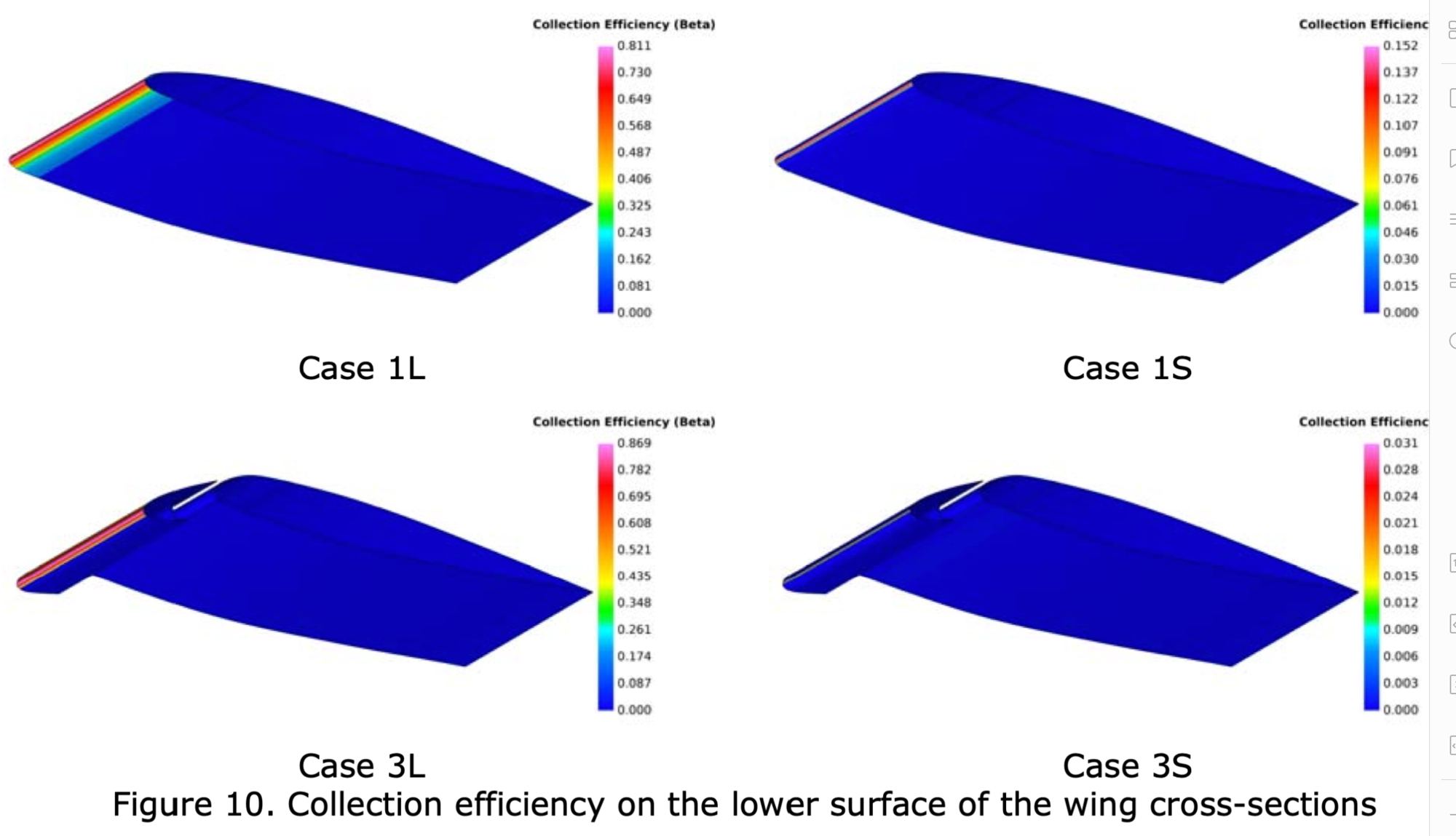
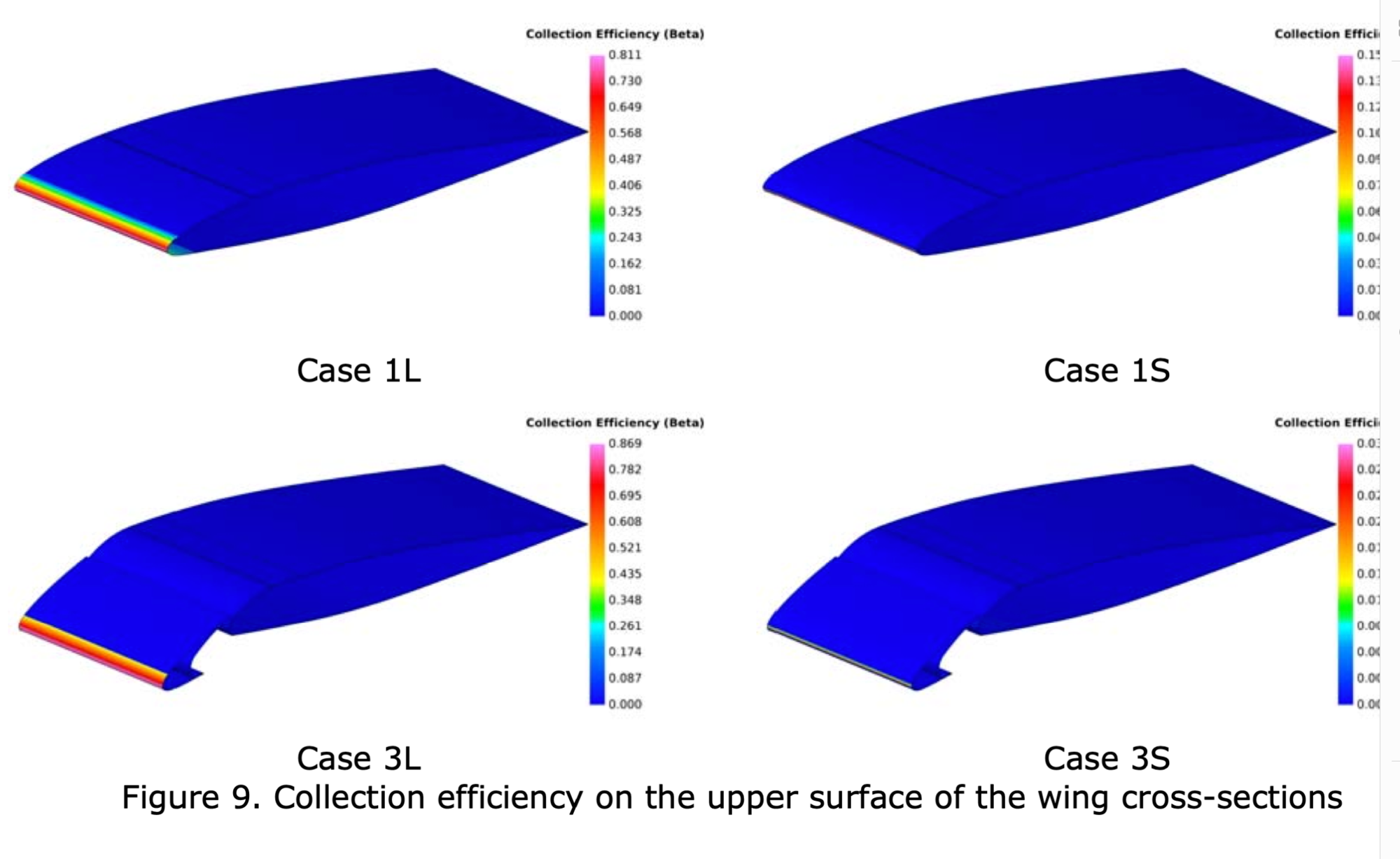
I think it links to your conclusion on the (lack of) other fixes apart from MCAS. They seem to have honestly chosen a solution that was readily available, required less R&D and cost as little as necessary, all that without penalizing performance As much as the internet likes to ridicule that decision, showboating and all [this thread is a great exception!!], what's being called clearly obvious in the laymen media sphere was for sure well known and thoroughly considered by the dedicated professionals yet AFTERWARDS they chose MCAS. No matter the pathetic killer gremlin MCAS 1.0 which was born later, the initial choice of picking the MCAS tool was a fair one. If it would be done again, there's absolutely no presentable evidence to deny that particular path. And as matter of fact that's what happened: The proper and agreed solution to control forces is MCAS 2.0 which is all that 1.0 wasn't and at the same time the exact thing they originally planned for.
Without getting carried away too far: Imagine the trailing edge modification had been chosen resulting in all the super critical geeky cool effects fdr explains. BUT THEN during the actual design and implementation aviation reality would be abused same as with MCAS 1.0. Such as failing to do ice contamination test and the additional load stress calculations. Resulting in flaps detaching a few years down the road - with crew performance same as on the second crash day, the death toll would have been identical.
Trying to say that selecting what is now disclosed and known as MCAS as a tool cannot be faulted. With extreme probability, it was well-reviewed against all the other options and chosen maybe even as a win-win.
.
As first envisaged, for the high-speed case, MCAS has some redundancy, and was not a bad option. The problem came when the concerns on low-speed stability resulted in a repurposing of the system by expediently removing what was the safety. That’s what humans do. We learn better from mistakes, and the systems that are employed to catch such errors are dependent on the individuals own characteristics to give assurance that the safeties work.
Without getting carried away too far: Imagine the trailing edge modification had been chosen resulting in all the super critical geeky cool effects fdr explains. BUT THEN during the actual design and implementation aviation reality would be abused same as with MCAS 1.0. Such as failing to do ice contamination test and the additional load stress calculations. Resulting in flaps detaching a few years down the road - with crew performance same as on the second crash day, the death toll would have been identical.
Trying to say that selecting what is now disclosed and known as MCAS as a tool cannot be faulted. With extreme probability, it was well-reviewed against all the other options and chosen maybe even as a win-win.
.
The strakes on the nacelles mitigate the reduction of section CL at higher AOA, by controlling the flow over the LE of the wing, and they do that well, They sit happily on the MAX, an aircraft that has a problem exactly from the fact that there is a surfeit of CL, coming off the surface in front of the wing, so that happy characteristic is able to be amended by reducing the size and effectiveness of the VG strakes on the nacelle. The downside is that would result in flight test increase of VS1G, and that gives a runway/payload penalty. Putting a trailing edge tab on the elevator is something that you do when you want more CL per angle of deflection, the same effect comes from having a thicker TE, which is nice enough, but it is not the problem that the MAX has, authority is not the issue, non -linear response is the issue. And to linearise that, either get rid of the offending force, nacelle dCL + vs nacelle/LE CL – from reducing the strake size. Nothing magical in that. To offset the runway performance, add a tab to the TE of the flaps, either inboard (improves wing bending moment, or both inboard and outboard to balance wing bending moment. Tabs increase CL/AOA, total, by a bucket load, but do add to a suppression of the stall AOA, which is oddly exactly what the doctor is ordering here… inboard reduction in CL at high AOA gives a nose down pitching moment on the swept wing, and makes the stall much nicer, and… happens at a lower speed, as total CL of the wing is higher, and that is for flaps down, flaps up and in fact at all times of the day or night. The additional benefits of tabbing a section is, you move the Cp aft on the associated section, so that is good too, it ensures that there is a solid moment to counter at all times. On Flaps, having paid for the recurrent AD on the maggots flap tracks, they are less than stellar in their design, per Peter Rudolphs comprehensive review of Transport Aircraft high lift devices, (High-Lift Systems on Commercial Subsonic Airliners, NASA Contractor Report 4746, contract A46374D(LAS) September 1996)
“This mechanism had its drawbacks because of the complexity in manufacturing and inherent problems with track and roller wear and reliability. Roller and track wear is caused by the load magnification that results from the flap loads that create a fairly short roller couple on the flap carriage”.
If you model the track system, the manner by which the track and carriages function can be seen, and that shows a system that is not going to like vibration, and that is what comes from all of the conventional flap systems that exist as the flow is separated at the TE, and so oscillatory loads are applied. Steady loads are easy, alternating loads mess stuff up. Stopping oscillation is a good thing, and that comes within the load capability of the flap tracks without mods.
To ascertain the wing bending moment changes on the aircraft in real time takes 2 flights, been there, done that, got the photos. That provides both bending and torsion changes for comparison. Calibration takes some rat cunning but is simple to accomplish. Someone wrote a nice paper on that technique; they were from the right side of the pond. TE modification was done on the MD11, as Divergent Trailing Edge, DTE. Airbus also flight trialled the same on the A330. TBC did a quiet trial on the B742, and that was an interesting outcome, Joe Sutter was a force behind doing that test, may he rest in peace.
Ice testing. The best software for doing that is out of Canada, and is approved by TC, as well as EASA. Lewice had its day, but as soon as computation went past as Tandy Trash-80, it went out of being that ground-breaking. Last I heard, it was no longer being supported, but the FAA still was cautious about a software that had a French flavor. A former national icing SME for the FAA did some spectacular work for us with that particular software, so, apart from the amount of drink vouchers that it cost to get the CFD imagery and the forces, I remain ardently supportive of the capability that the Canucks developed. As to whether the competency of analysis exists, the following is an excerpt of the relevant DERs background: Project Manager for natural icing testing of Chinese ARJ21-700 in Canada during March and April 2014. DER in icing for 14 CFR Part 23 & 25. Constructed 3D CAD models of airplanes for CFD analysis using laser and photogrammetry. Consultant to Accident Investigation Board of Norway for takeoff icing incident of CRJ-200. Managed icing certification and noise testing project of C-26B STC. Lecturer on use of CFD in icing certification for airplanes, rotorcraft and engines. Icing consultant for transport airplane ice protection systems and rotorcraft engine inlet icing testing and other STC projects. Expert witness in FAA certification and icing issues. Author of technical articles and SAE papers. 2007 to present
The most recent resource for icing for the FAA, Tom Bond is also highly competent, and anyone doing certification in EASA or the FAA would have their concerns assuaged by the skill and competency of the people in the offices, and for my money, of the capabilities of the north of the border approved icing software. FWIW, we did validations of the software up at Bethpage, and also in-flight natural icing conditions. Amazing how hard it is to get icing when you want it.
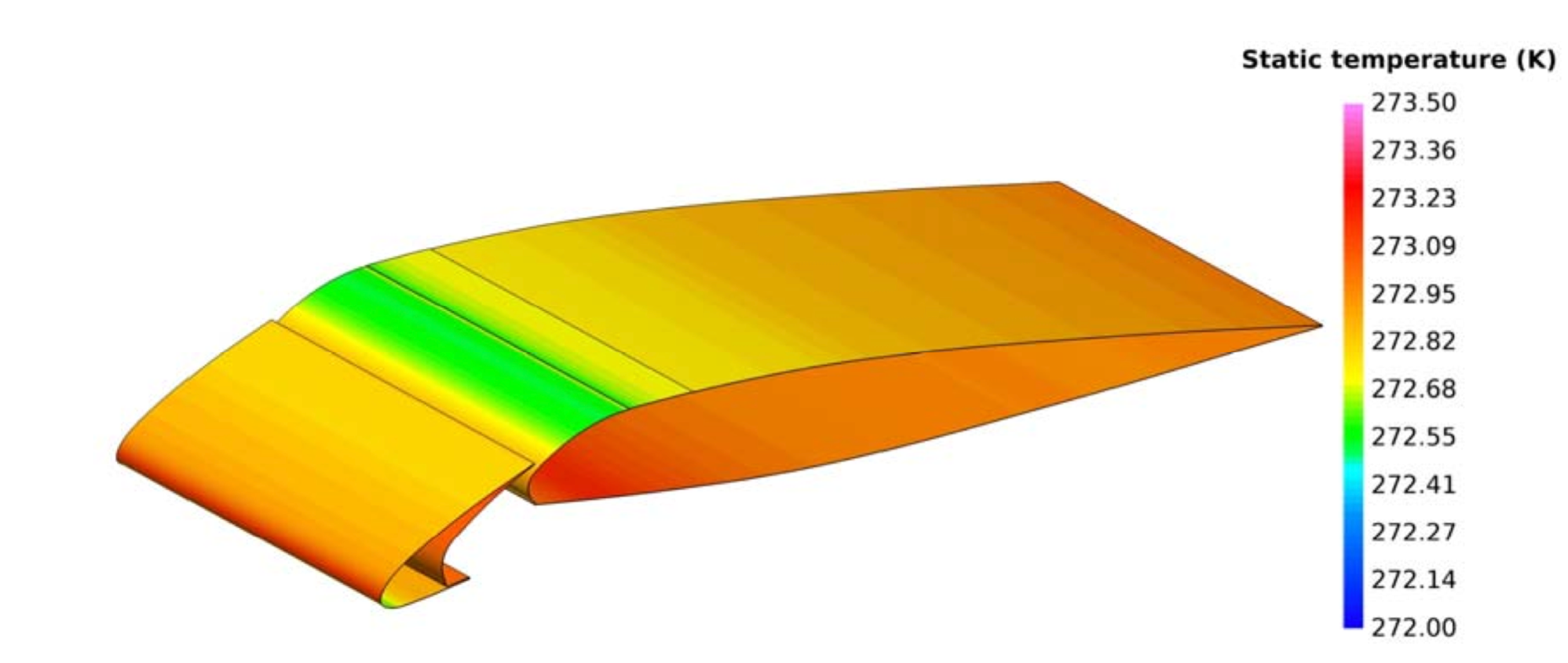
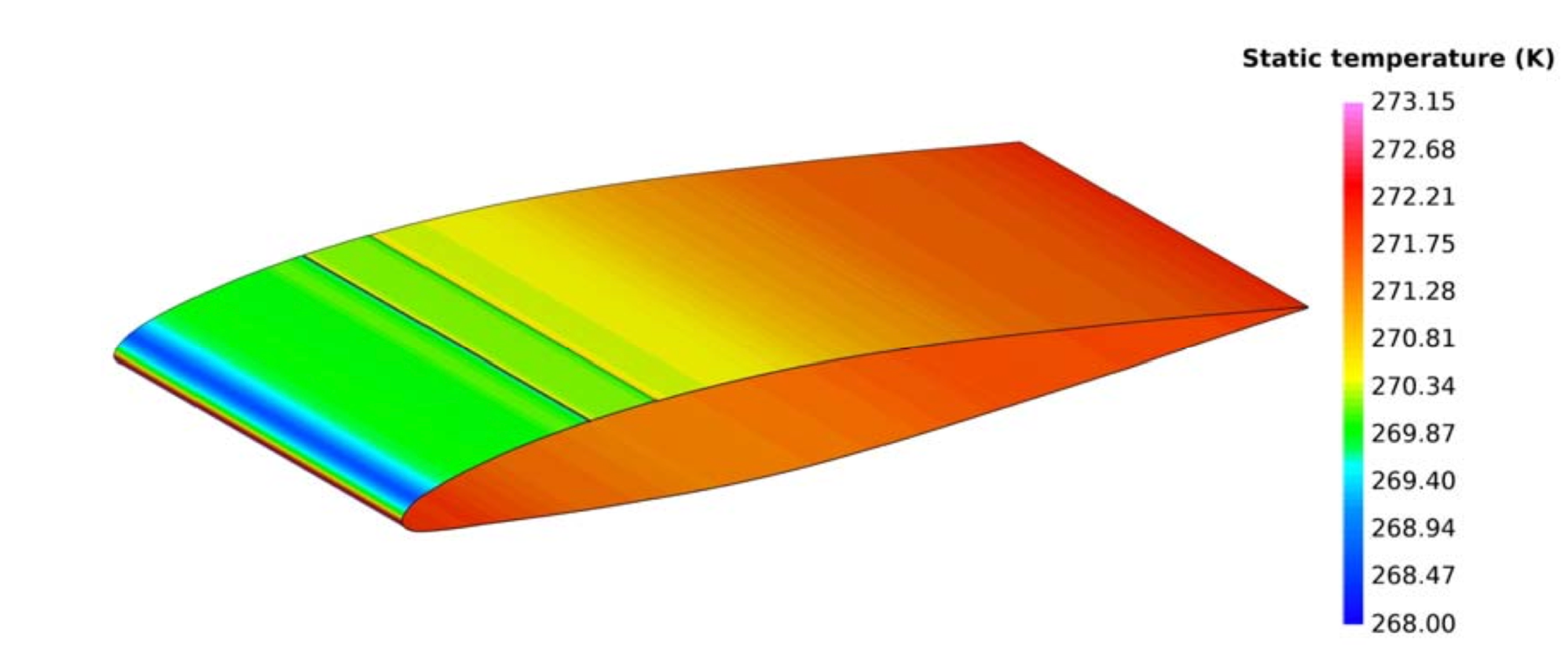
Last edited by fdr; 2nd Feb 2021 at 14:59.
Cons of the other suggestions, as picked up over the forums here1:
strakes
- Very badly predictable in the design stage. You do not know what it does unless you flight test it. Single engine, side slipped flight at high AoA with ice on them and only one gets a hot air blast the exhaust,? A/C departs controlled flight to the side. Unpredictable risk on the development scope and amount of effort. fdr's stories on fast jet nose section design speak volumes.
- Adding weight and drag penalties, no matter how small amounts, does count (for some). The largest customers do care, rightfully or not their Excels are sharp and furious.
- Extra maintenance requirement for inspections over the lifetime of the airframe. Cost, costs, costs... customer choice, customer choice, customer choice
- Increased risk of ramp collisions. IDK but any object with mass has its own gravity and on the ramp EVERYTHING gets hit eventually. New repair schedule, new DDG items... oh.
.
The drag of a single TBC VG is by recollection 0.0002 units, so, yes, they do add drag. They also can reduce drag by about 100 times their own drag count where there is a flow control benefit, so, not sure I concur.
Funny thing about aero mods, apparently it is assumed that they need to be of iron or steel or at least aluminium. That is in spite of the certain knowledge that an air jet with modify a flow field, and oddly for the last 30 odd years, I worked with elastomeric materials and other soft structures as I was both cheap, and having a desire to play with blades, didn’t have a death wish. In 2007 I flew elastomeric materials as a tab on a helicopter rotor, having done the same on propellers for 13 years previously. The argument on ramp rash doesn’t end up having validity when the devices are able to be squishy stuff. Just my opinion though. The materials required are high tech, you have to be able to find an Ace Hardware at least, or an Auto One, so, yes, there are technical hurdles.
trailing edge mod on the wing or elevators
- Completely out of scope, design frozen, signed and dusted for. The simple little issue needs a simple little solution. Constant re-tweaking kills projects like nothing else. And why touch the wing unless you absolutely have to? You don't. Sure, for the MAX+ at 2028 it will be done.
.
stick pusher AS WELL AS artificial feel unit mod
- certification review of the F/CTL system
- training required, commonality tanked
- extra weight
- messing with what works never goes without problems. Probably best they did not - geez these guys failed to connect the AoA light and could not see MCAS acting on the sole most powerful aerodynamic control is class A critical item like no other.
.
The stick pusher is actually not a cure for the issue, it avoids one of the undesirable states, but does not affect the stick force gradient that is the underlying irritant. If one was employed, refer to the bean counters lament re runway/payload loss. The B747 never required a stick pusher, putting an extraneous safety device on an aircraft due to ignorance is not the hallmark of excellence. 747s stall very nicely.
MCAS
- a software routine, simple to model and dry test
- easy to update and change later across the global fleet
- does what needs to be done
- does not involve touching any of the existing systems that have been time-tested to perfection
- no extra hardware
- no additional training as it really is just an additional spinning mode for what the STS actually is - an autonomous THS compensator.
Yet, after all, the very same teams who understandably chose the proper way out is with MCAS against the hard options, could not avail themselves to just doing anything but simply admit a less than perfect force characteristics on the control column. The EASA boss statement is inconclusive. Various otherwise dangerous aeroplanes (not the case of MAX) can be flown safely if you know how to do it.
I think Peter Ladkin and the gang at the RVS Group (AG RVS - Arbeitsgruppe Rechnernetze und Verteilte Systeme) at U Bielefeld may disagree. Would be an interesting conversation though.
A thought in passing: We live in a world that we establish heuristics that are functionally linear as that is what we can comprehend as analogs of complexity. The world however is stochastic, and we are set up by our very nature to have bad days as a consequence. Our own behavior is anywhere from logical to emotional, and the complete spectrum in between. We do not think linearly at all, yet we attempt to model the world in that way. The variability and non-linear manner that the human conducts cognitive functions gives the ability to achieve creativity, which helps when we get situations that give divide by zero outcomes. More often than not, it is the human's ability to cognitively function in conditions of uncertainty, using our innate fuzzy logic, that permits a solution, a save, or creativity to occur. It was the human variability in September 83 that saved the planet from a , man-made destruction, Stanislav Yevgrafovich Petrov (Станисла́в Евгра́фович Петро́в) saved the whole damn planet, and he passed away in near anonymity in 2017, "I was made a scapegoat". He stands alongside Captain Vasily Arkhipov (Василий Александрович Архипов) who refused to fire a nuke torpedo during the Cuban missile crisis. Arkhipov had been on the Hotel I K-19 previously during the reactor casualty event, under the command of Captain Nikolai Zateyev (Николай Владимирович Затеев). A couple of years later, on a Foxtrot DE SS, B-59.
Arkhipov and Zateyev both died of cancer, 10 days apart; the Hiroshima class was an apt name for the Hotel, Echo, and November boats of the USSR.
Perfect systems... like Chernobyl, 3 Mile Island, Fukushima...
Last edited by fdr; 2nd Feb 2021 at 15:38. Reason: a thought....
Thread Starter
fdr,
Thank you (and all you other knowledgeable posters here too). As you say fdr, the 747 stalls very nicely, I did many on the -100s and -200s during CofA check flights. When the 747 was put on the British register, D. P Davies required a stick nudger (not a pusher) to restore longitudinal stability shortly before the clean stall at aft CG. I quote his words from his book, Handlng the Big Jets:-
"With trim speed of 1.3Vs, after a small elevator force to start the speed reduction, the stick force falls to zero while the aeroplane quietly progresses all the way to the stall on its own .... It is common knowledge that the UK attitude to stalling is quite firm and this degree of instability, although slight, was declared unacceptable. The fix was the nudger. This is a gentle stick force augmentor of about 16lbs in the nose down sense which operates when the stick shaker starts to operate and remains effective until the stick shake cancels. In a fairly rough and rudimentary manner it restores pre-stall longitudinal stability and satisfies the requirement at little cost and with no snags. It is similar to the nudger fitted to 707-320B/C aircraft certificated in the UK which, while not taking out all the pre-stall pitch up at full flap aft CG, at least restores a positive stick force gradient down to a point very close to the stall."
Here was a simple cheap and reliable fix which had already been used on Boeing aircraft. It would have required no training with only a mention in the manuals. Would this not have been a better solution?
Thank you (and all you other knowledgeable posters here too). As you say fdr, the 747 stalls very nicely, I did many on the -100s and -200s during CofA check flights. When the 747 was put on the British register, D. P Davies required a stick nudger (not a pusher) to restore longitudinal stability shortly before the clean stall at aft CG. I quote his words from his book, Handlng the Big Jets:-
"With trim speed of 1.3Vs, after a small elevator force to start the speed reduction, the stick force falls to zero while the aeroplane quietly progresses all the way to the stall on its own .... It is common knowledge that the UK attitude to stalling is quite firm and this degree of instability, although slight, was declared unacceptable. The fix was the nudger. This is a gentle stick force augmentor of about 16lbs in the nose down sense which operates when the stick shaker starts to operate and remains effective until the stick shake cancels. In a fairly rough and rudimentary manner it restores pre-stall longitudinal stability and satisfies the requirement at little cost and with no snags. It is similar to the nudger fitted to 707-320B/C aircraft certificated in the UK which, while not taking out all the pre-stall pitch up at full flap aft CG, at least restores a positive stick force gradient down to a point very close to the stall."
Here was a simple cheap and reliable fix which had already been used on Boeing aircraft. It would have required no training with only a mention in the manuals. Would this not have been a better solution?
Only half a speed-brake
Guess all left here is saying thanks for setting me straight? I do, appreciated. Happy and excited to read your contributions, fdr.
Last edited by FlightDetent; 2nd Feb 2021 at 21:29.