"NJK blew a jug today"
Thread Starter
"NJK blew a jug today"
Yesterday, our chief tow pilot sent out an email advising of a significant schedule change: "NJK blew a jug today". NJK is our long-time Scout tow-plane. I was at the field at the time, just preparing to do some circuits in our new C182 tow-plane, prior to getting checked out for towing in it.
The pilot of the Scout called me on the radio after landing, to say he was having a significant power loss. I suggested all the usual things - mags, mixture, carb heat, full-power run up, but he said he'd tried all that.
So I went off to do my circuits, while an investigation took place. When I had finished and shut down, the Scout was in the hangar, with the cowling off. I was told it had a cracked cylinder, so I went over to have a look.
The 180 HP Lycoming O-360 is a very reliable engine, but is prone to cylinder head cracking, particularly when subjected to shock-cooling. Our SOPs are designed to minimize shock-cooling, but cracking does occasionally happen. Normally a crack develops at the spark plug threads and propagates to the exhaust port.
This "crack" was completely different - the cylinder head had parted company with the barrel! This is a view looking downward on the left rear cylinder:
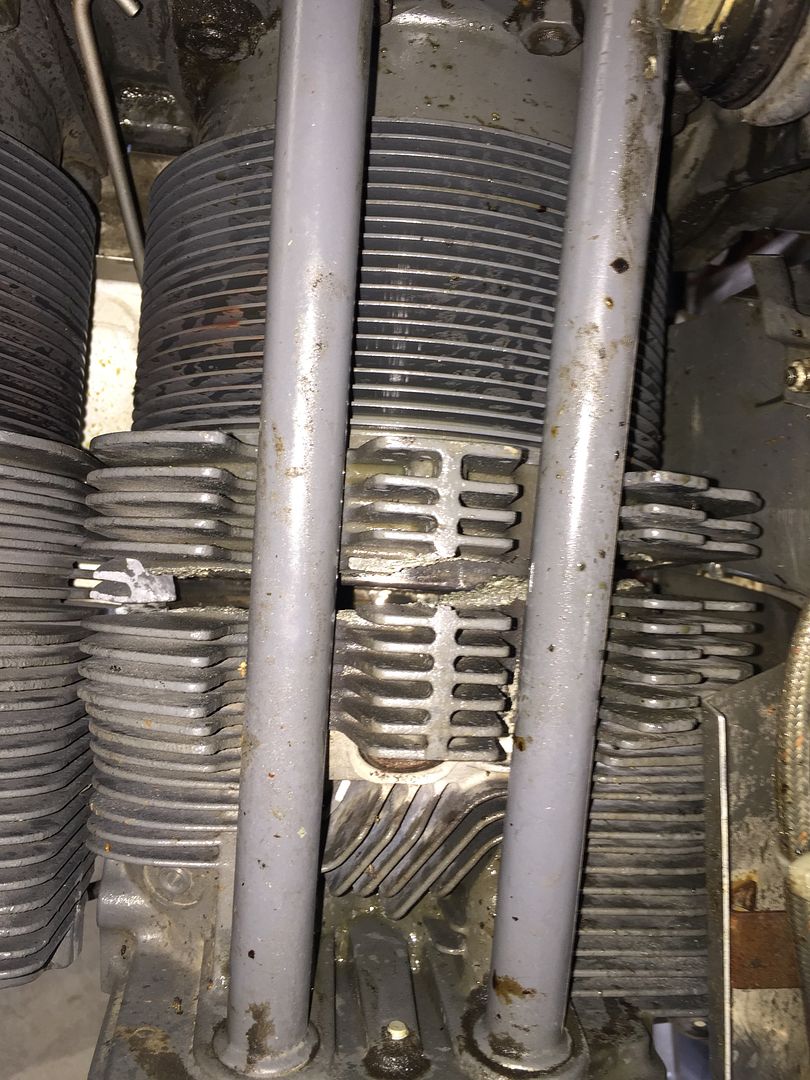
I could see the end of the liner through the gap and the cylinder head had moved outward nearly an inch. The failure happened while towing, but since there was not a total engine-failure, we are hoping that we can get away with just a new cylinder and piston and be back in the air in a week.
A (sort of) bonus for me was that it was the first time I had seen a "naked" O-360 and so I was able to have a good look at all the "bits and pieces", that are not normally visible:
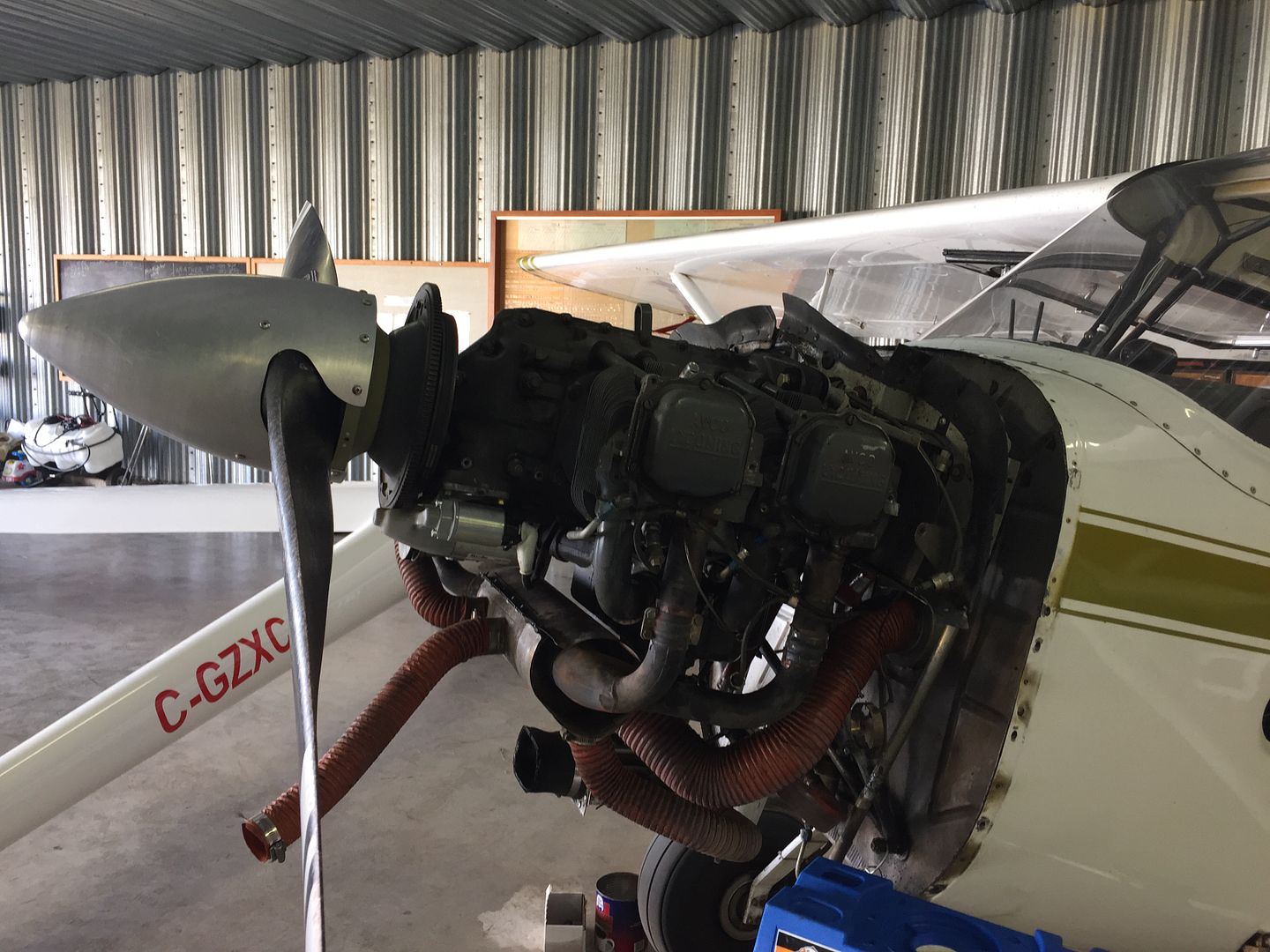
It's our Student Training Week this week, so with the Scout down, my training on the C182 was deemed finished and I immediately started towing.
Here's NJK in happier days:

and here's our new C182, PZE:
The pilot of the Scout called me on the radio after landing, to say he was having a significant power loss. I suggested all the usual things - mags, mixture, carb heat, full-power run up, but he said he'd tried all that.
So I went off to do my circuits, while an investigation took place. When I had finished and shut down, the Scout was in the hangar, with the cowling off. I was told it had a cracked cylinder, so I went over to have a look.
The 180 HP Lycoming O-360 is a very reliable engine, but is prone to cylinder head cracking, particularly when subjected to shock-cooling. Our SOPs are designed to minimize shock-cooling, but cracking does occasionally happen. Normally a crack develops at the spark plug threads and propagates to the exhaust port.
This "crack" was completely different - the cylinder head had parted company with the barrel! This is a view looking downward on the left rear cylinder:
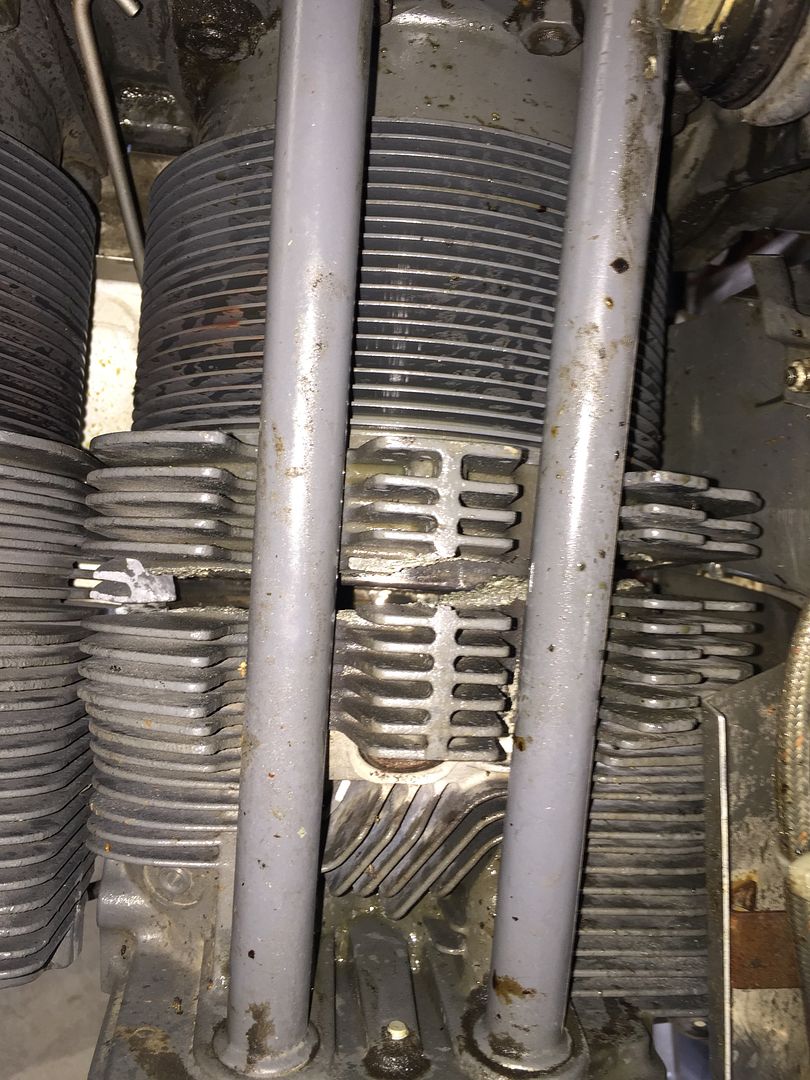
I could see the end of the liner through the gap and the cylinder head had moved outward nearly an inch. The failure happened while towing, but since there was not a total engine-failure, we are hoping that we can get away with just a new cylinder and piston and be back in the air in a week.
A (sort of) bonus for me was that it was the first time I had seen a "naked" O-360 and so I was able to have a good look at all the "bits and pieces", that are not normally visible:
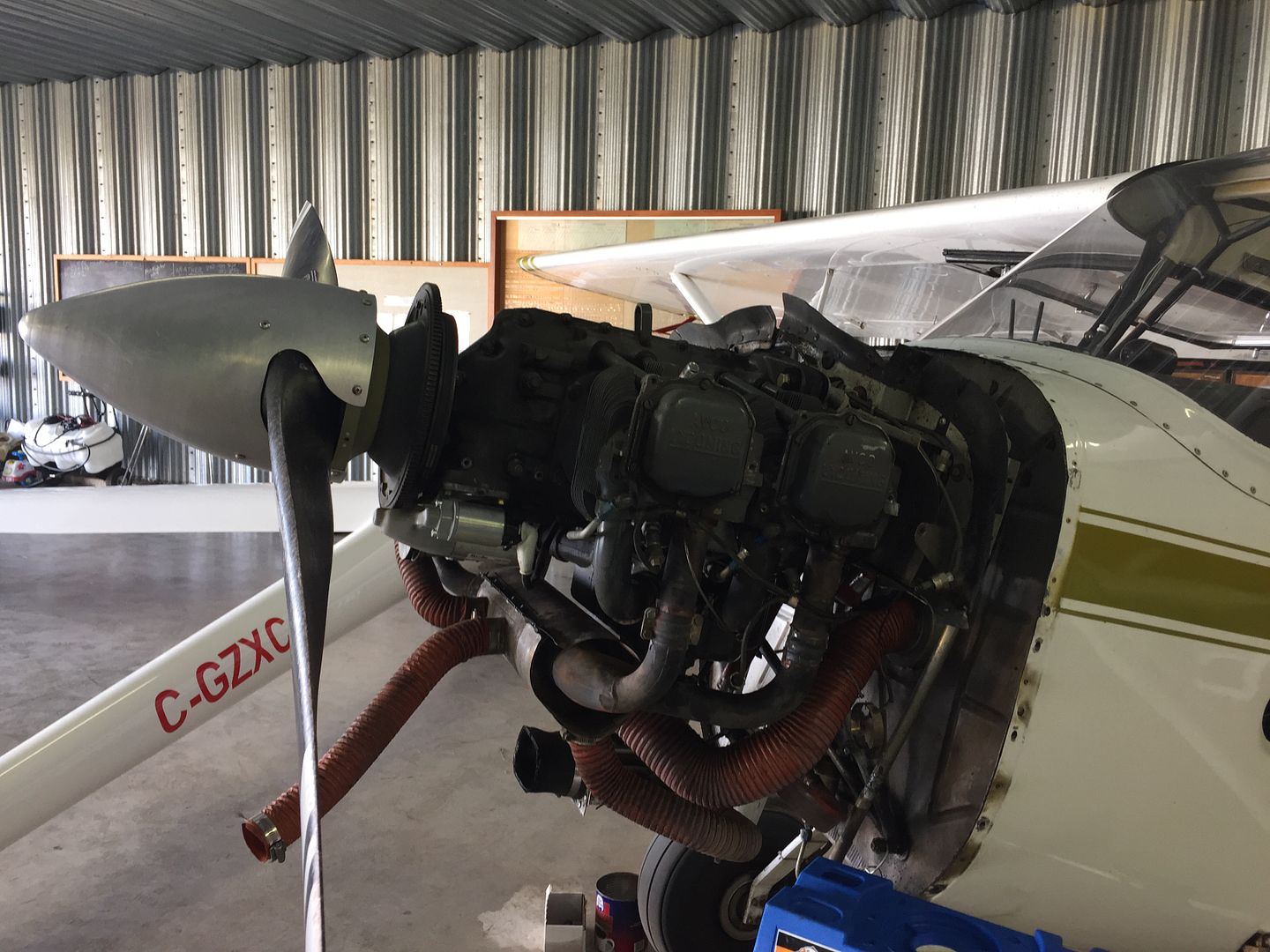
It's our Student Training Week this week, so with the Scout down, my training on the C182 was deemed finished and I immediately started towing.

Here's NJK in happier days:

and here's our new C182, PZE:
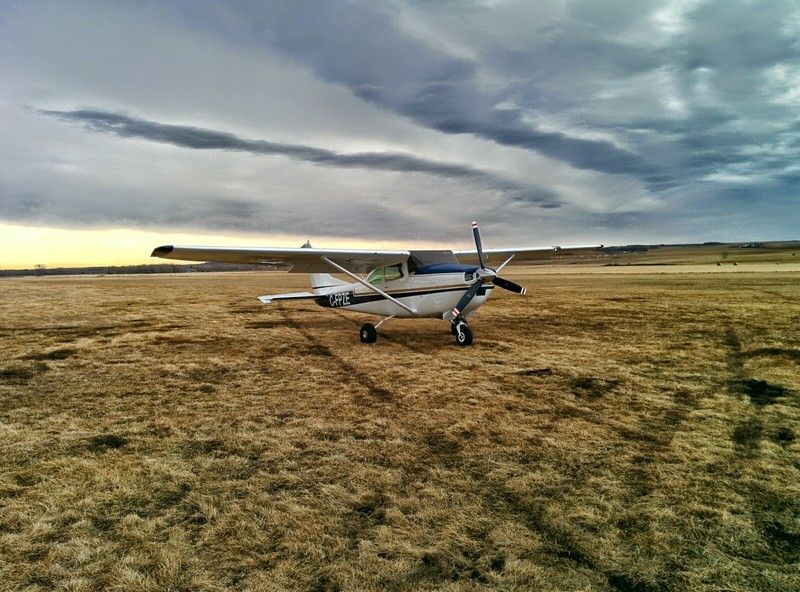
Last edited by India Four Two; 9th Jul 2015 at 01:10. Reason: Changed O-320 to O-360
Join Date: Jul 2013
Location: Medway towns
Age: 72
Posts: 40
Likes: 0
Received 0 Likes
on
0 Posts
squeeeek
When you consider the assembly method, I'm amazed that it doesn't happen more often.....
A red hot head is screwed onto an icy cold barrel, quickly....
Two seconds later, the dimensions are such that the thread is about to seize....
A last ditch attempt to get alignment right puts a lot of stress on the casting!
In service, there's a huge shear load across the top of the barrel, through the casting, and if any corrosion has started the casting is going to fail... so beware engines that have low hours and been in 'storage'....
It is also possible that the threads have been machined a little out... 'bottoming' will overload the alloy.
Veerry interesting....!
A red hot head is screwed onto an icy cold barrel, quickly....
Two seconds later, the dimensions are such that the thread is about to seize....
A last ditch attempt to get alignment right puts a lot of stress on the casting!
In service, there's a huge shear load across the top of the barrel, through the casting, and if any corrosion has started the casting is going to fail... so beware engines that have low hours and been in 'storage'....
It is also possible that the threads have been machined a little out... 'bottoming' will overload the alloy.
Veerry interesting....!
Thread Starter
PC and DOF,
I'll ask about the compression when I'm back at the field tomorrow. I'll also see if I can get a look at the cylinder once it is off the engine.
I'll ask about the compression when I'm back at the field tomorrow. I'll also see if I can get a look at the cylinder once it is off the engine.
Join Date: Jan 2011
Location: In an ever changing place
Posts: 1,039
Likes: 0
Received 0 Likes
on
0 Posts
I hope that I am wrong, but you will be very lucky indeed to get away with just a cylinder replacement. Probable causes, either severe detonation or a valve letting go and hitting the piston. How many hours are the engine ?
but is prone to cylinder head cracking, particularly when subjected to shock-cooling. Our SOPs are designed to minimize shock-cooling, but cracking does occasionally happen.
Lasham Gliding Society were getting through a lot of cylinders on their Lycomings until they rewrote their descent procedures.
https://cdn.shopify.com/s/files/1/01...ision_2013.pdf
Our club, just up the road, had a head crack on the 180hp Lycoming in our 'Supermunk' a few years ago. As I recall it was about £1000 for a new barrel & piston to fix it. It failed at a few hundred feet on a first solo aerotow, so the tug pilot carried on to the top of the launch so as to not cause the learner pilot further stress. Had it been an instructor on the back I expect he would have dumped him there and then.
I was surprised just how big the crack was; about 3/16" (5mm). As I recall it was between the two valves.
With regard to the stresses in the shrunk-on heads, its worth remembering that the aluminium alloy heads will expand more when hot than the steel barrels due to the differing expansion rates of the two materials, so the cylinder head screw thread may be less stressed when hot than when cold. The thermal gradient between the fuel cooled inlet valve and the exhaust heated exhaust valve will, however, be high.
https://cdn.shopify.com/s/files/1/01...ision_2013.pdf
Our club, just up the road, had a head crack on the 180hp Lycoming in our 'Supermunk' a few years ago. As I recall it was about £1000 for a new barrel & piston to fix it. It failed at a few hundred feet on a first solo aerotow, so the tug pilot carried on to the top of the launch so as to not cause the learner pilot further stress. Had it been an instructor on the back I expect he would have dumped him there and then.
I was surprised just how big the crack was; about 3/16" (5mm). As I recall it was between the two valves.
With regard to the stresses in the shrunk-on heads, its worth remembering that the aluminium alloy heads will expand more when hot than the steel barrels due to the differing expansion rates of the two materials, so the cylinder head screw thread may be less stressed when hot than when cold. The thermal gradient between the fuel cooled inlet valve and the exhaust heated exhaust valve will, however, be high.
Thread Starter
Please let us know what your SOPs are....
Climb out with full throttle and one notch of flap at 65-70 mph depending on the glider, keeping an eye on the CHT and oil temperature. Increase speed and/or richen the mixture, if temperature limits are approached.
After release, throttle back to 2200 rpm and go to full-flap to increase drag. Increase speed to 80 mph. When the CHT goes below 300° F or after one minute, throttle back to 1600 rpm, avoiding the yellow arc of 1700-2100 rpm.
Make a full-flap descent at no more than 90 mph, maintaining 1600 rpm until short final.
The Alberta clubs have been operating Citabrias and Scouts like this for over thirty years. Besides yesterday's failure, I'm only aware of one other cylinder failure due to cracking, although there may have been more.
*************
Whoops - I've realized I've been referring to an O-320 when I should have said O-360!

I've gone back and edited my mistakes!
Thread Starter
An update
Following the cylinder head failure on Tuesday, new parts were ordered on Wednesday (cylinder and piston). On Thursday morning, I was out at the field for my towing shift in the C182.
About 9am, an ancient C150 (with a 150 HP engine) arrived with two mechanics, some tools and a white, cylinder-sized box. They promptly started removing the broken cylinder on the Scout.
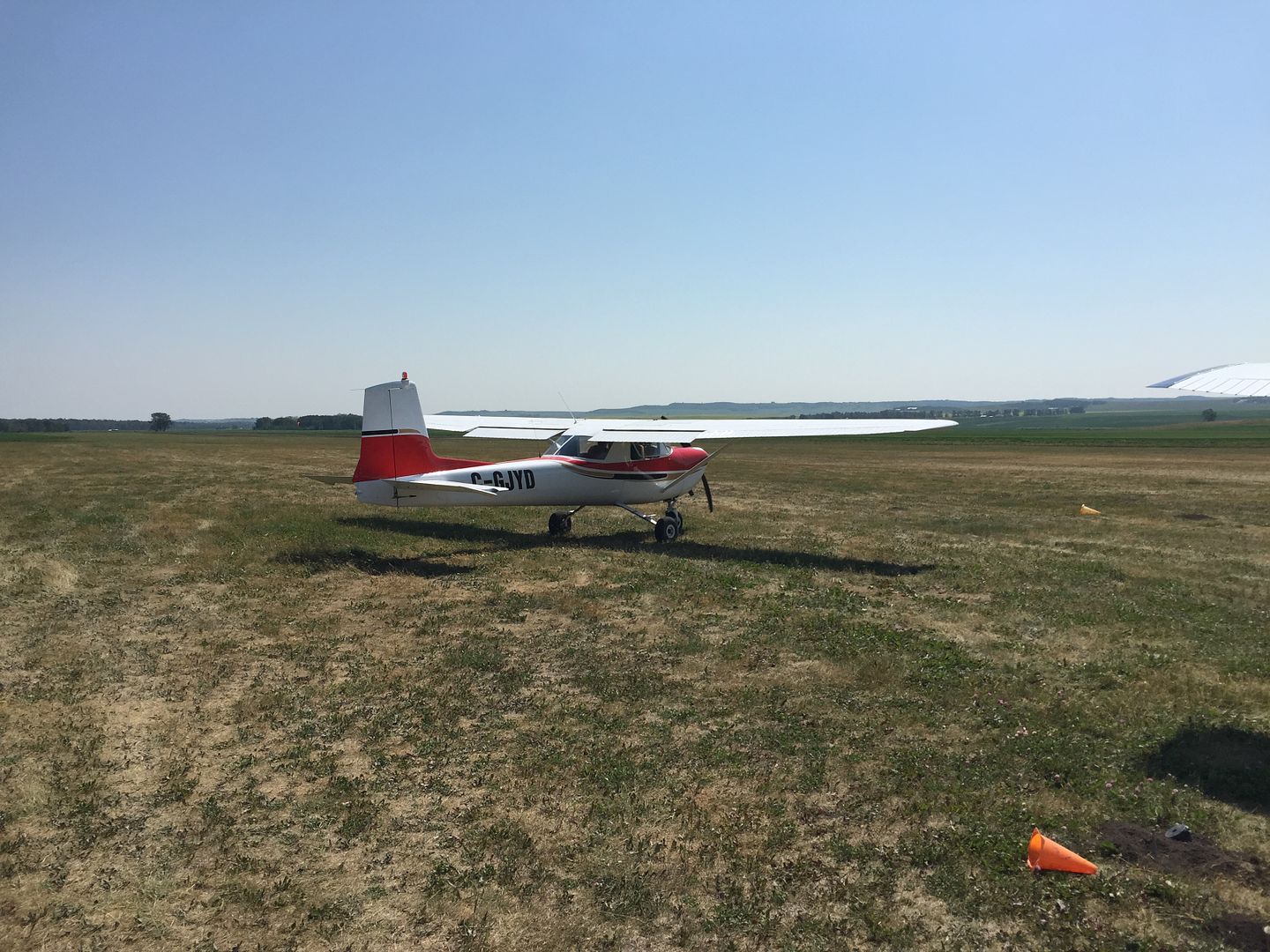
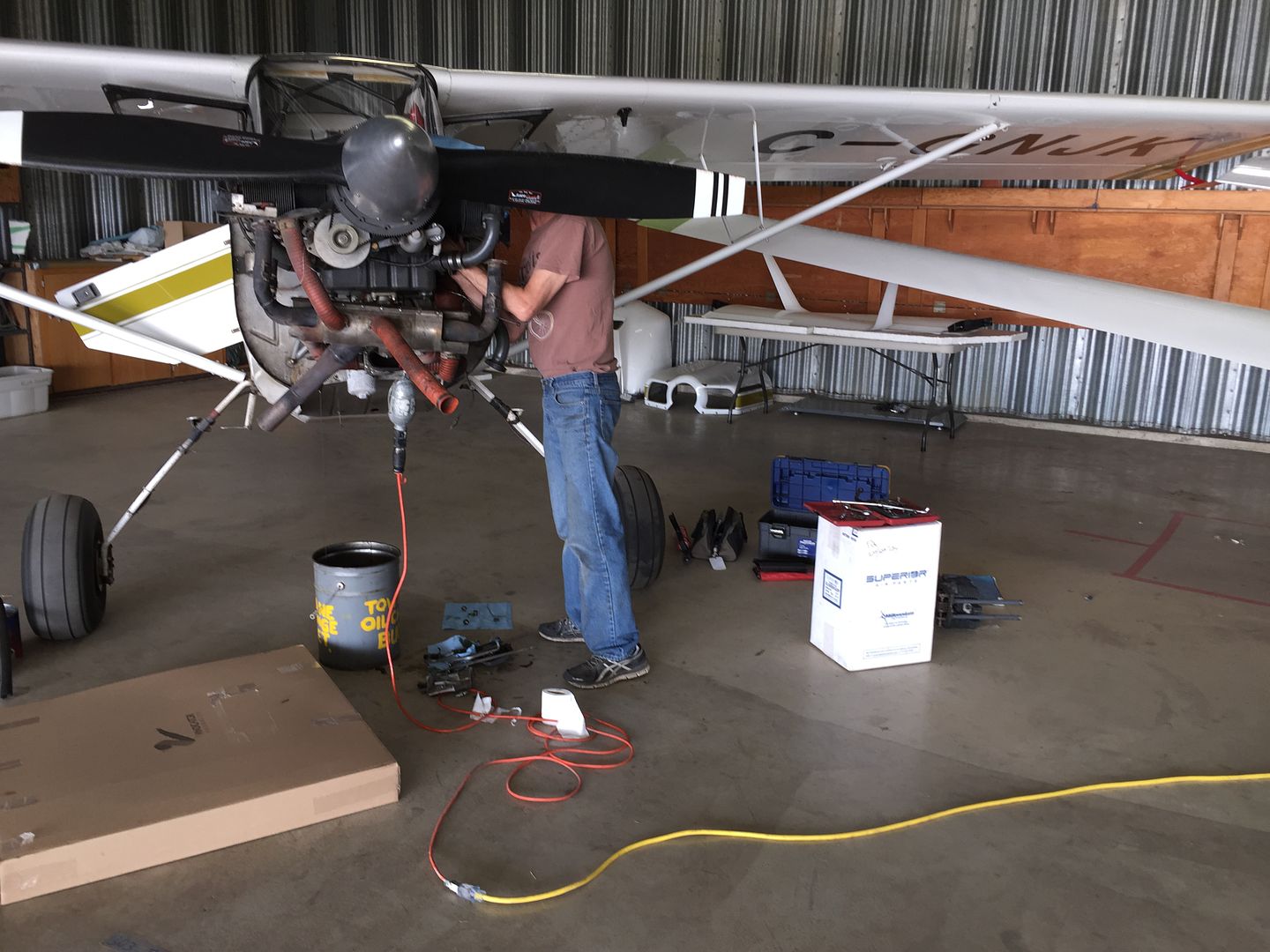
During discussions with the mechanics, we discovered that we didn't have a new oil filter, so another tow-pilot and I abandoned the students waiting to be towed and we flew the 182 for twenty minutes to High River, our maintenance base, to pick one up. Getting ready to go again, we discovered the battery was flat, so there was a one hour delay while the battery was charged and the problem diagnosed. It turned out that the ground wires for the alternator had become disconnected. Somewhat embarrassing that neither of us had noticed the discharge on the flight over.
With the fuel cost and the maintenance bill, we must have the world's most expensive oil filter!
Because of the delay, by the time we arrived back, the new piston and cylinder had been installed. I went off to tow in the 182 and when I had a break about 12:30, my colleague was getting ready for a test flight in the Scout! Less than four hours for the repair and less than two days since the failure. Amazing!
After the test flight, my colleague flew the Scout to High River to check the compressions, which were OK. He told me that he flew very high, looking for good fields all the way!
Here are some pictures of the failed cylinder head:
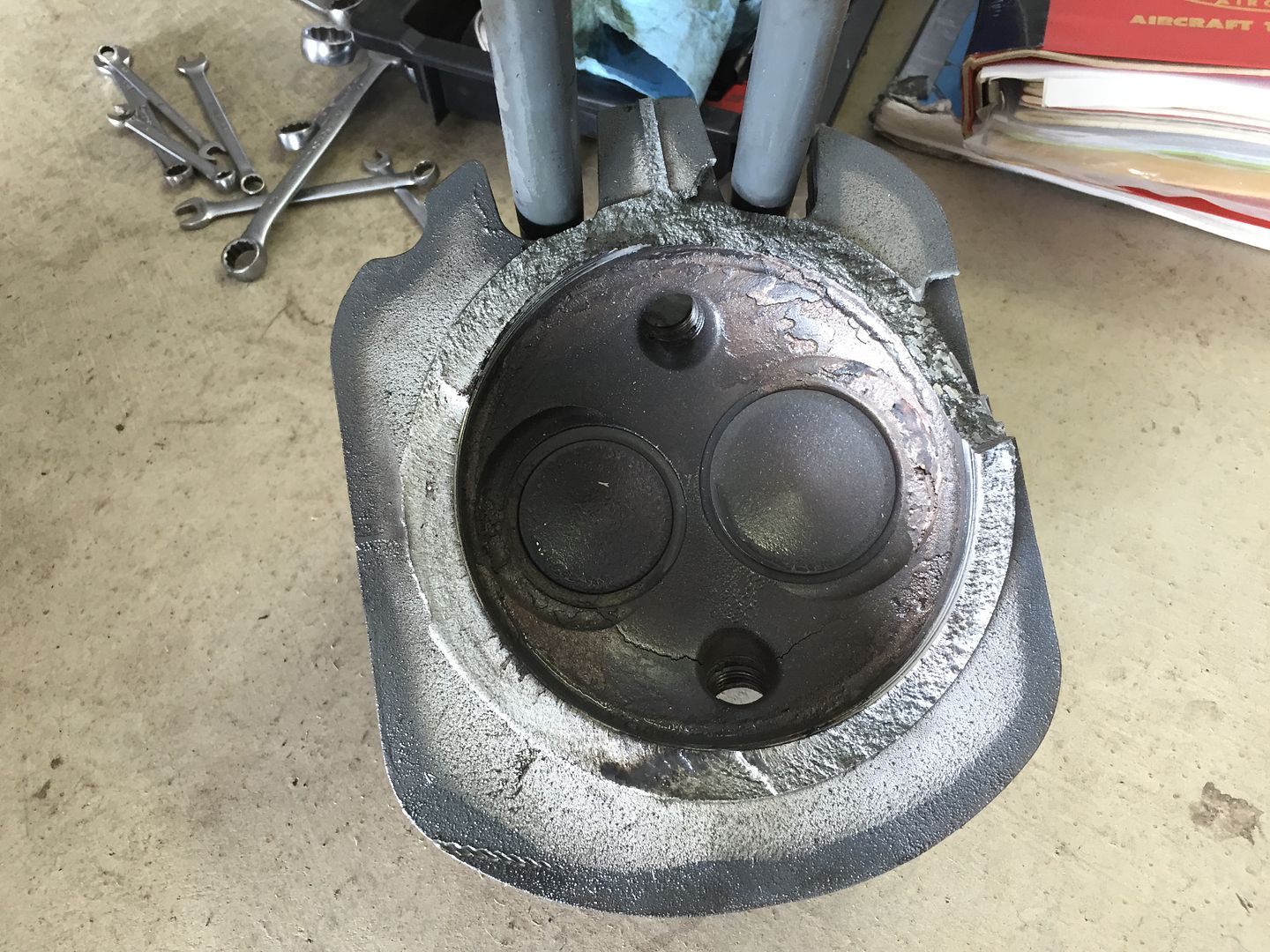
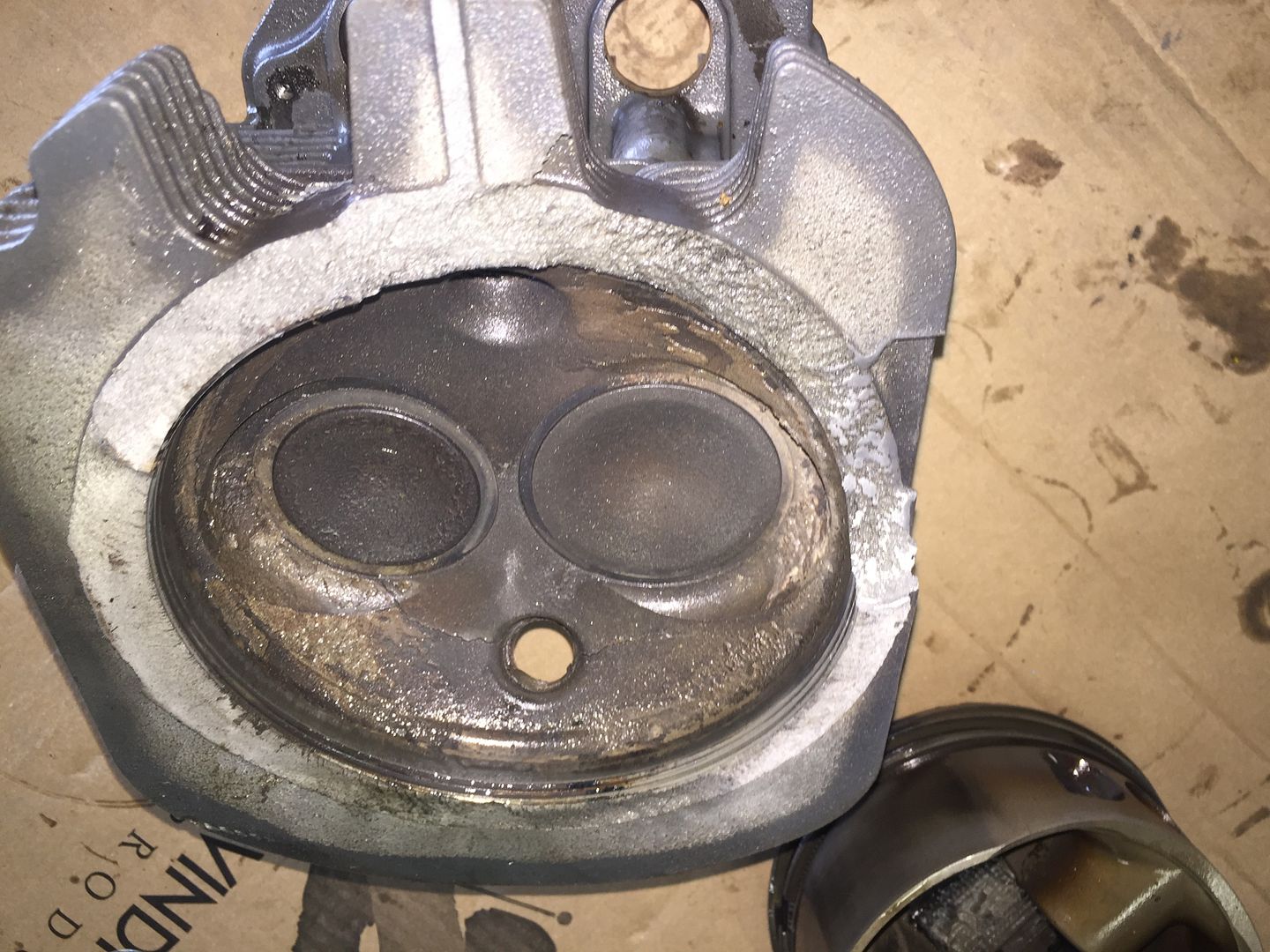
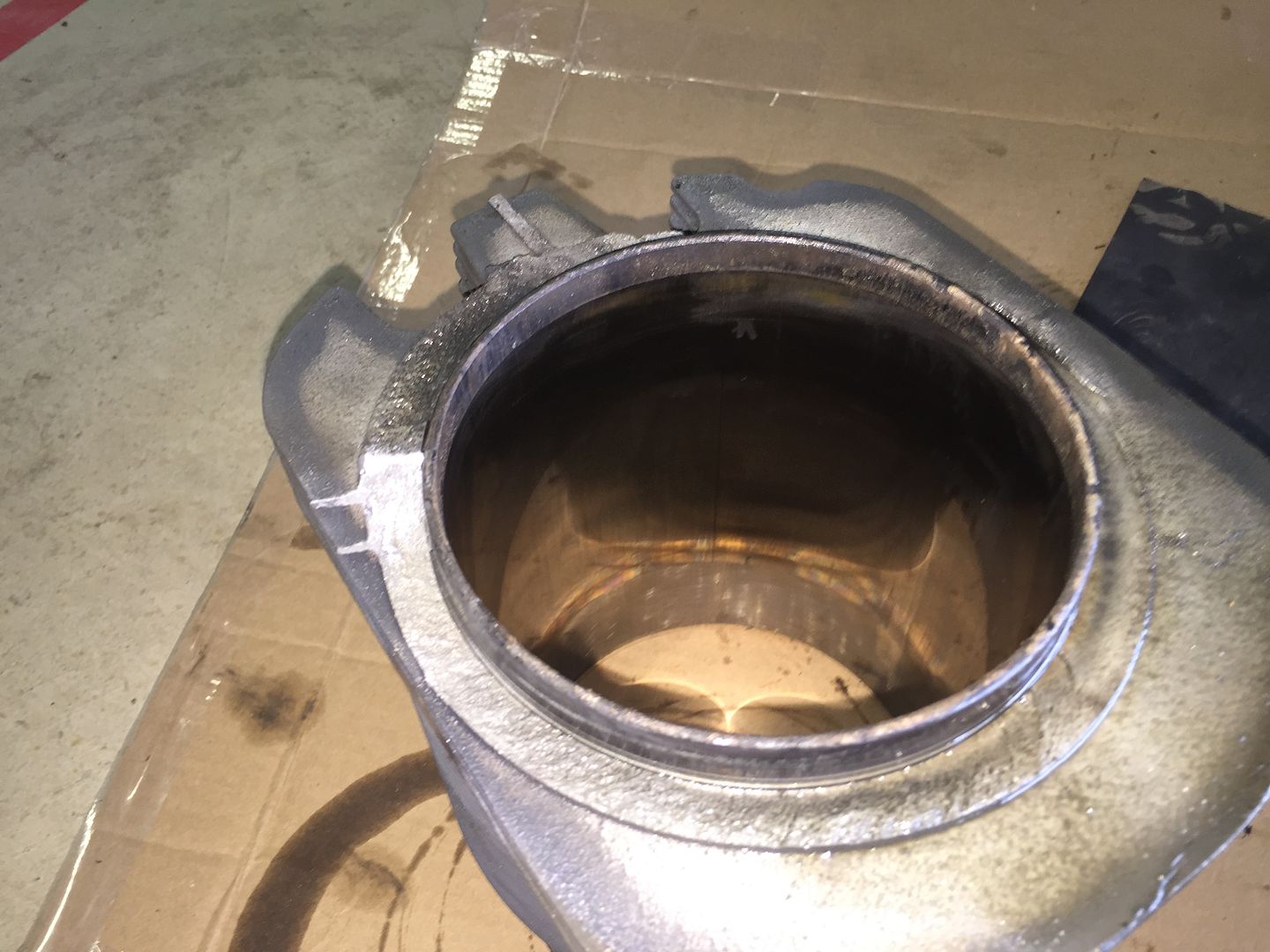
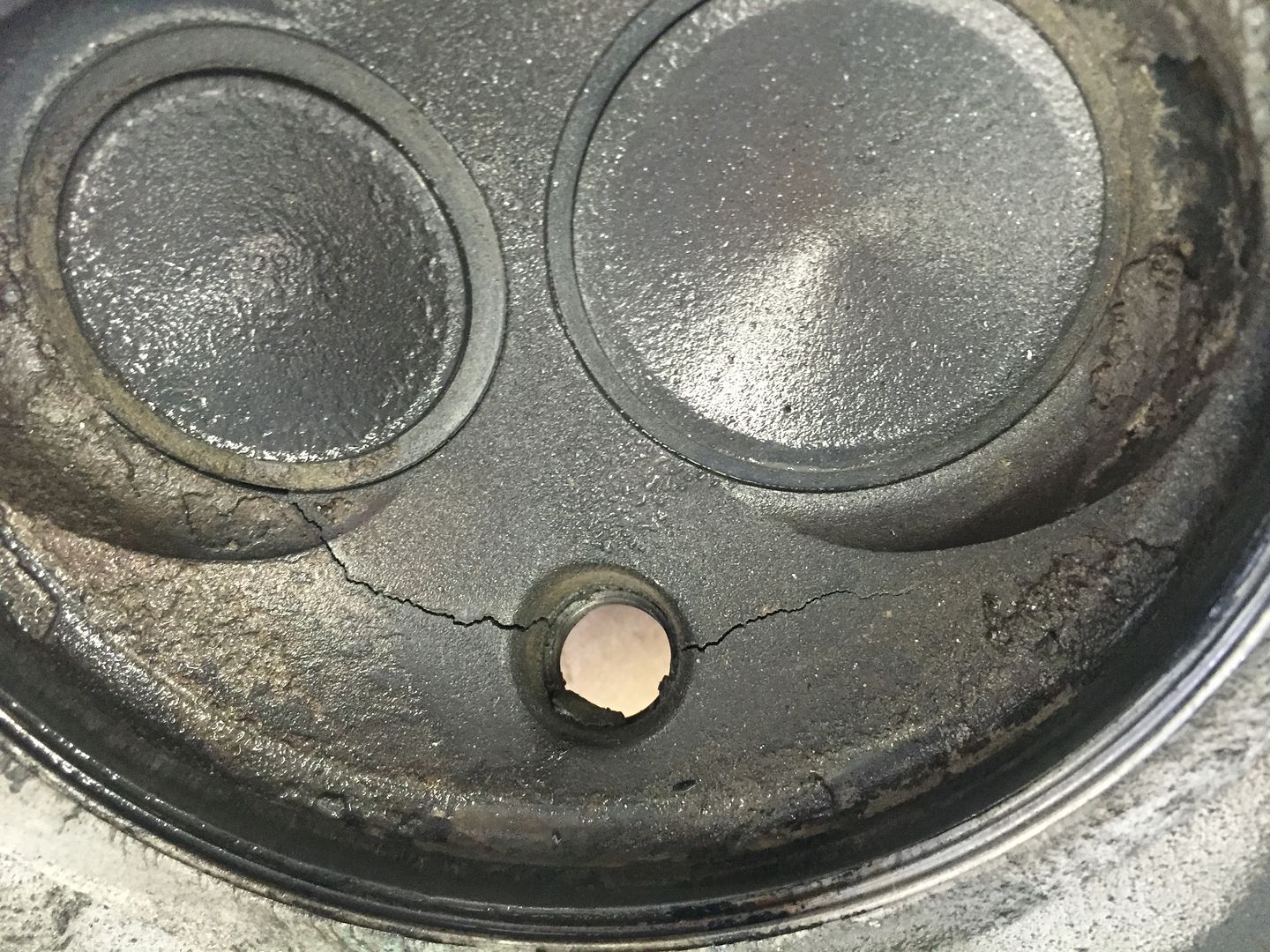
Apparently this complete failure of the head casting is very rare, but note that there are pre-existing cracks that propagated from the spark plug threads. This is the more usual cracking failure.
About 9am, an ancient C150 (with a 150 HP engine) arrived with two mechanics, some tools and a white, cylinder-sized box. They promptly started removing the broken cylinder on the Scout.
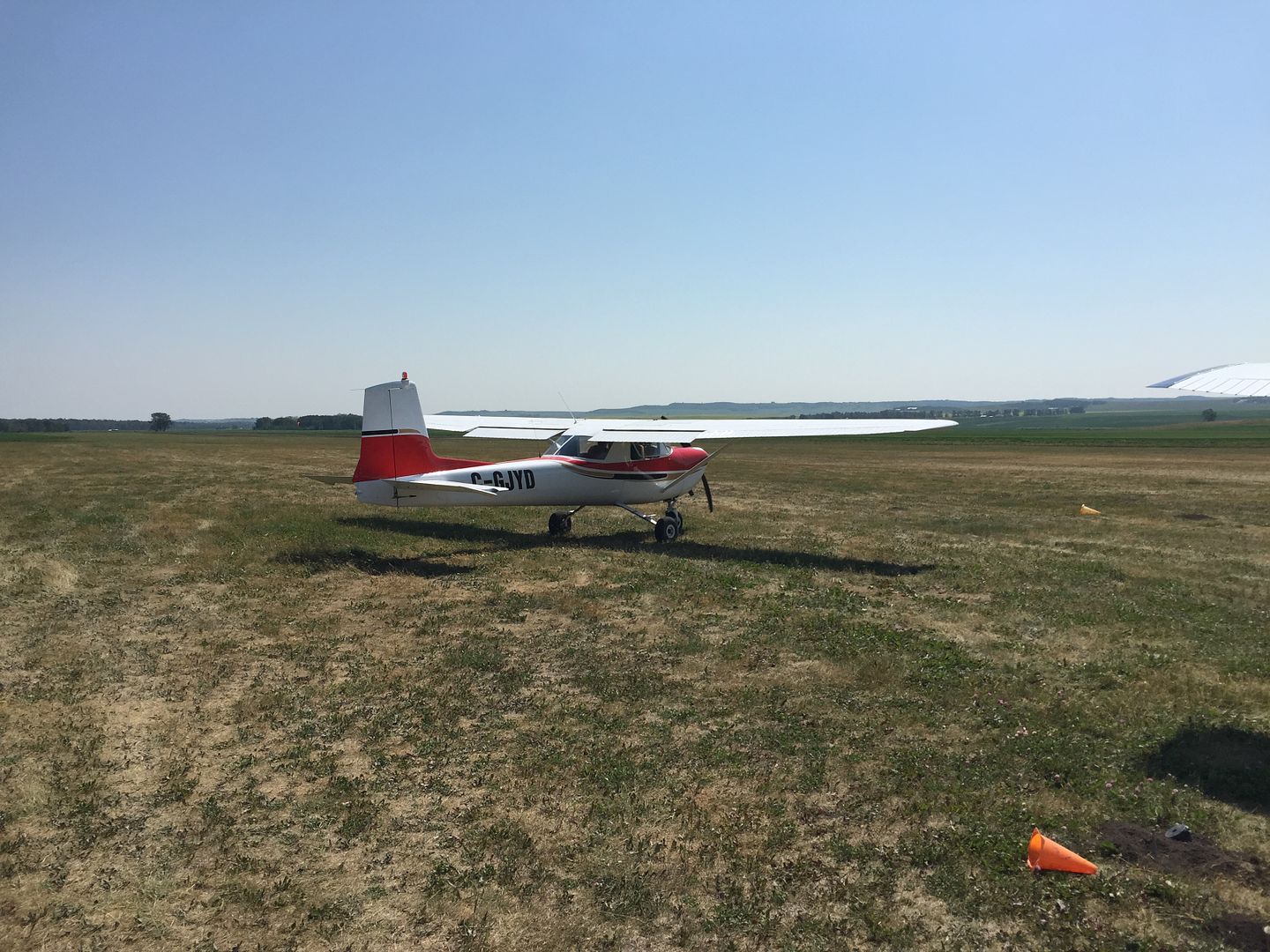
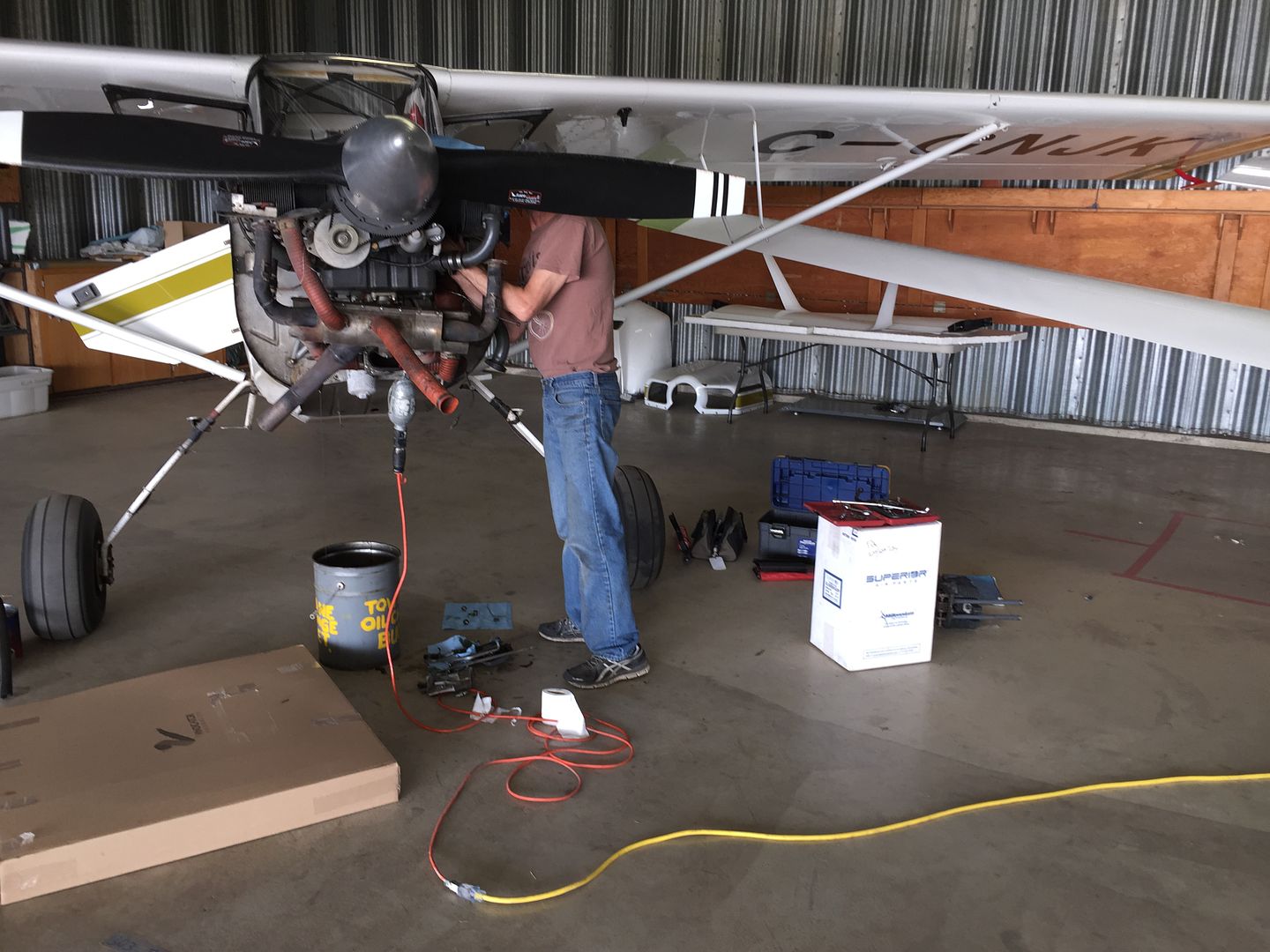
During discussions with the mechanics, we discovered that we didn't have a new oil filter, so another tow-pilot and I abandoned the students waiting to be towed and we flew the 182 for twenty minutes to High River, our maintenance base, to pick one up. Getting ready to go again, we discovered the battery was flat, so there was a one hour delay while the battery was charged and the problem diagnosed. It turned out that the ground wires for the alternator had become disconnected. Somewhat embarrassing that neither of us had noticed the discharge on the flight over.

Because of the delay, by the time we arrived back, the new piston and cylinder had been installed. I went off to tow in the 182 and when I had a break about 12:30, my colleague was getting ready for a test flight in the Scout! Less than four hours for the repair and less than two days since the failure. Amazing!
After the test flight, my colleague flew the Scout to High River to check the compressions, which were OK. He told me that he flew very high, looking for good fields all the way!

Here are some pictures of the failed cylinder head:
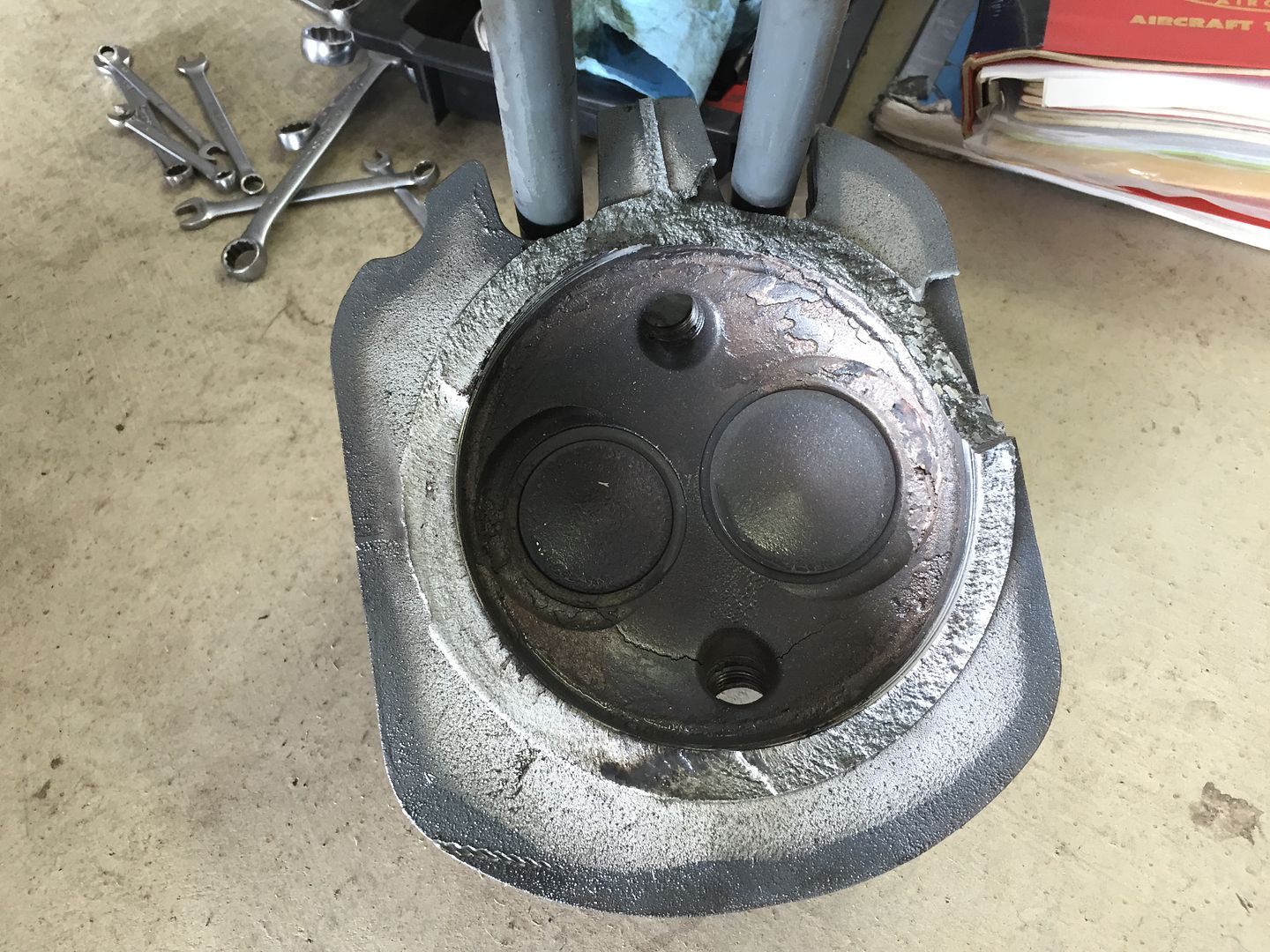
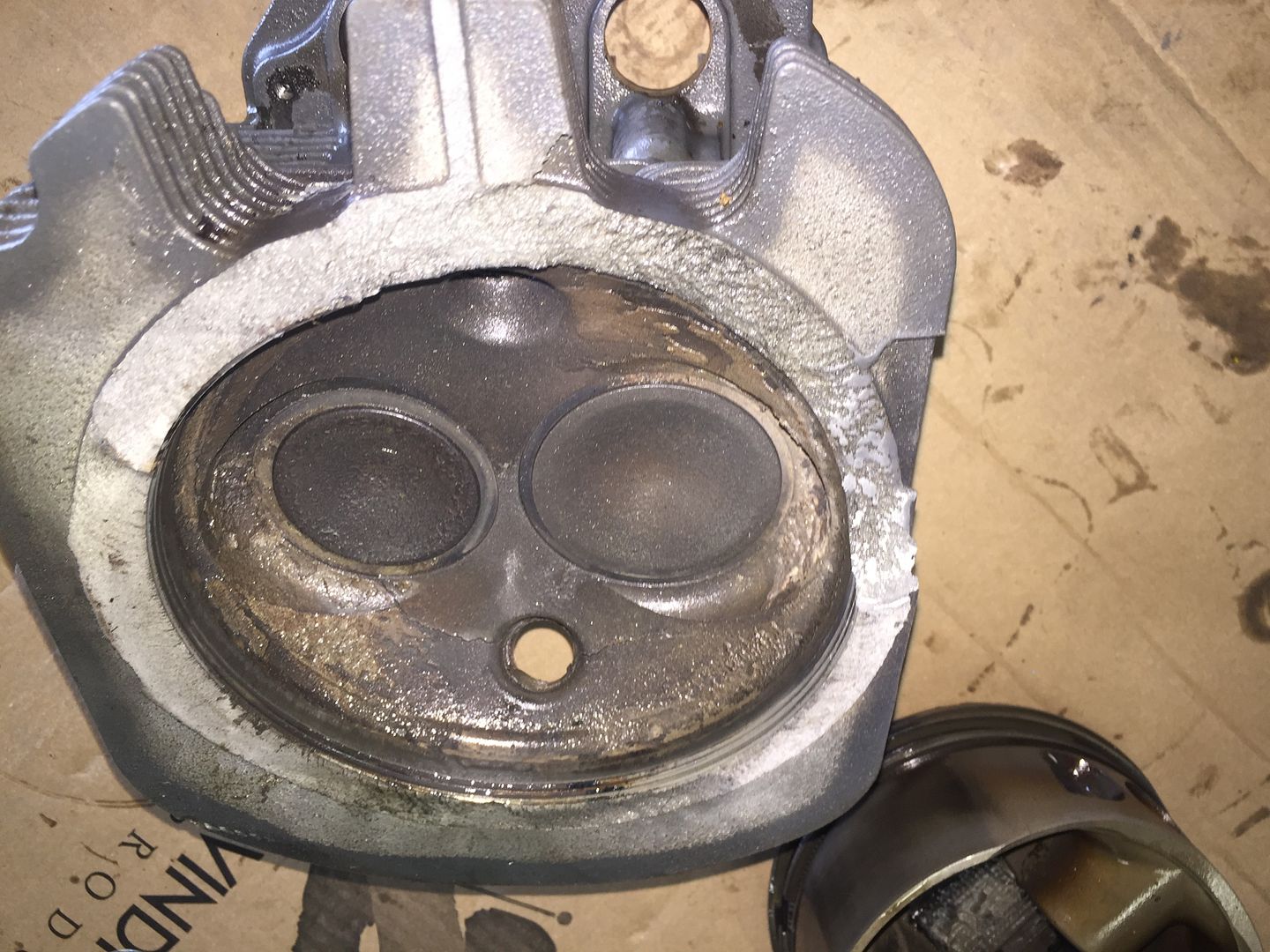
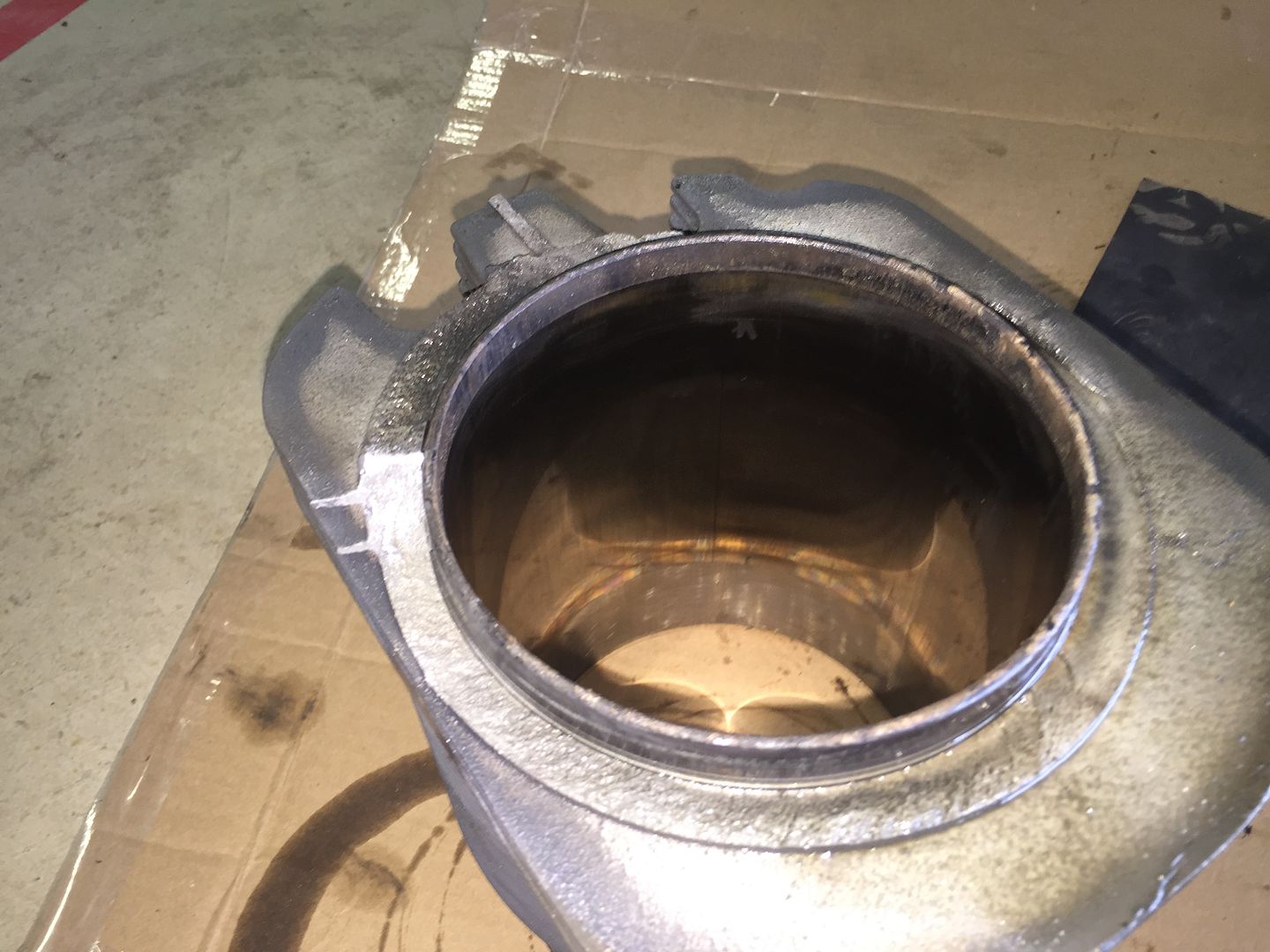
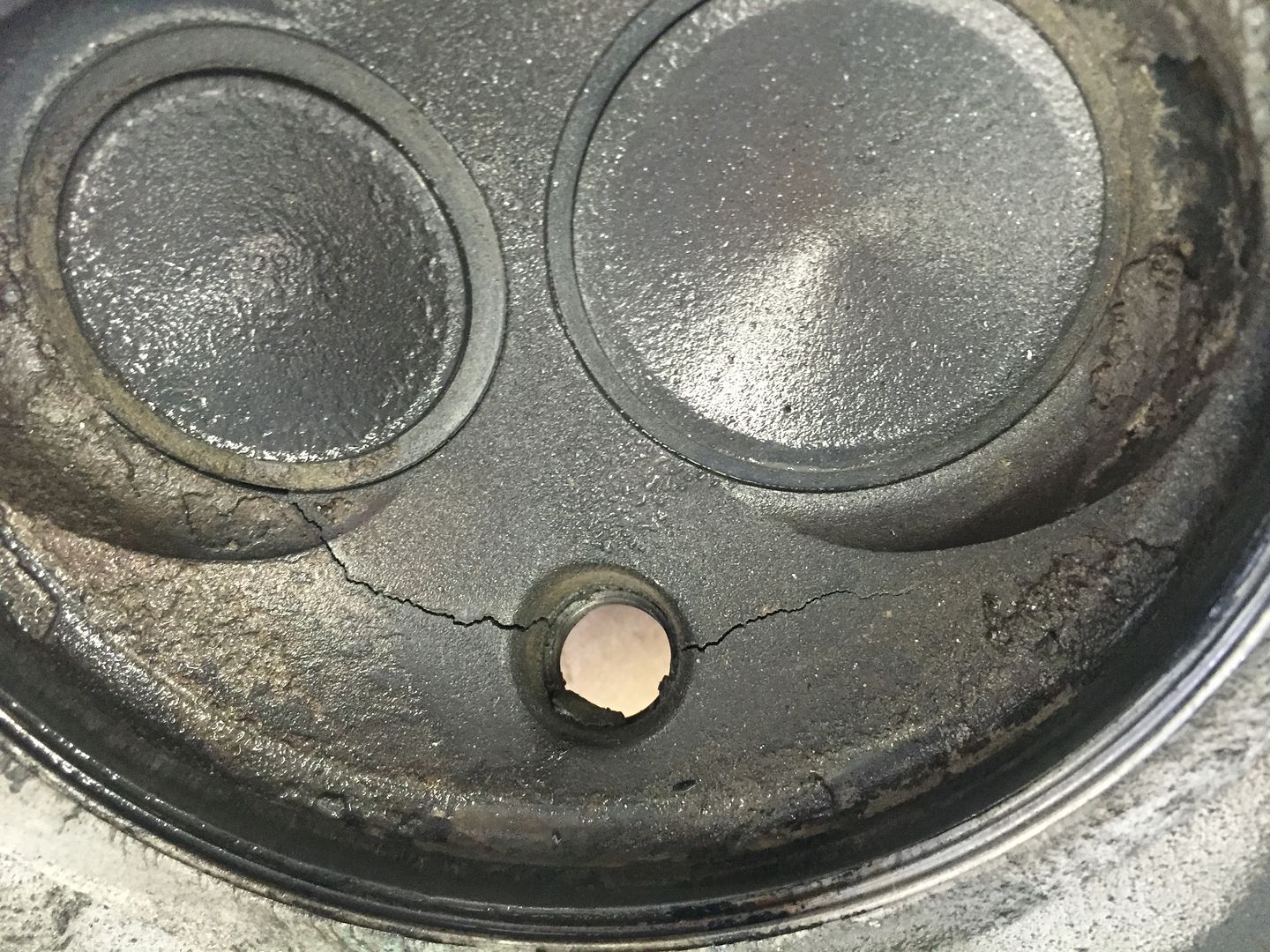
Apparently this complete failure of the head casting is very rare, but note that there are pre-existing cracks that propagated from the spark plug threads. This is the more usual cracking failure.
Join Date: Jan 2011
Location: In an ever changing place
Posts: 1,039
Likes: 0
Received 0 Likes
on
0 Posts
Any metal found in the oil filter ?
If one cylinder has a crack around the spark plug hole it would wise to borescope the other cylinders soon just in case, or just pull them and have a look, how many hours are on those cylinders ?
If one cylinder has a crack around the spark plug hole it would wise to borescope the other cylinders soon just in case, or just pull them and have a look, how many hours are on those cylinders ?
Join Date: Jan 2008
Location: Canada
Posts: 631
Likes: 0
Received 0 Likes
on
0 Posts
The pre-exisitng cracks at the spark plug hole are cause for investigation of the other cylinders, and evidence that at some point, the cylinders experienced some heat extremes. The danger with this kind of spark plug hole cylinder head crack is that a valve seat drop out, and jam the valve open. All kinds of bad things happen then, and the damage is instantly spread throughout the whole engine, rather than hopefully being contained to just one cylinder.
It does sound that the present SOP is best practice, all things considered.
The important things is that several pilots mentioned in this discussion have done the right thing, they kept flying the plane! This is a perfect example of a partial engine failure. Though you want the plane back on the ground ASAP, it is still flying under power, and can be flown to a safe landing. Too many times, the big shaking has begun, and the pilot has panicked, and crashed needlessly. Use what you have, and fly the plane to a safe landing, don't give up, just 'cause it's shaking!
It does sound that the present SOP is best practice, all things considered.
The important things is that several pilots mentioned in this discussion have done the right thing, they kept flying the plane! This is a perfect example of a partial engine failure. Though you want the plane back on the ground ASAP, it is still flying under power, and can be flown to a safe landing. Too many times, the big shaking has begun, and the pilot has panicked, and crashed needlessly. Use what you have, and fly the plane to a safe landing, don't give up, just 'cause it's shaking!
Join Date: Jan 2011
Location: In an ever changing place
Posts: 1,039
Likes: 0
Received 0 Likes
on
0 Posts
I have also just noticed in your second picture of the valves, when you zoom in there seems to be large cracks around the valve seats as well, opposite to the crack in the lower spark plug hole area.
Thread Starter
DP,
About 1700 hours. Interestingly, the cylinder that failed was a replacement for a previous cylinder failure, a few years ago.
ATC,
No metal in the filter. The annual is due soon and the cylinders will be bore-scoped then. Our AME felt that the satisfactory compression check was a sufficient test.
The "cracks around the valve" seats are just combustion deposit that have flaked, giving the appearance of cracks.
I turned the head over and saw that the long crack from the spark plug to the exhaust valve has propagated all the way through to the outer surface of the head.
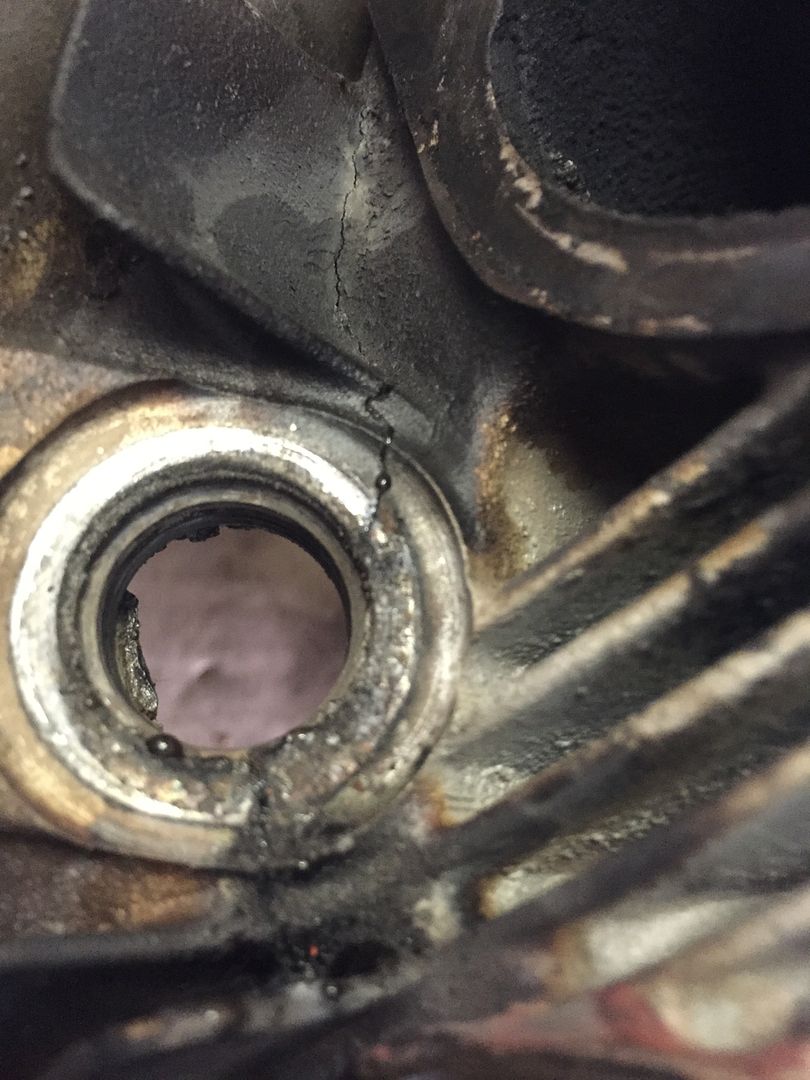
I think we were very lucky with this incident. The head didn't fly off and cause any further damage, the tow-pilot had enough power to maneuver to a safe location to wave-off the glider and if the head hadn't failed, in the future, the existing crack could have caused valve-seat failure and subsequent catastrophic engine failure.
About 1700 hours. Interestingly, the cylinder that failed was a replacement for a previous cylinder failure, a few years ago.
ATC,
No metal in the filter. The annual is due soon and the cylinders will be bore-scoped then. Our AME felt that the satisfactory compression check was a sufficient test.
The "cracks around the valve" seats are just combustion deposit that have flaked, giving the appearance of cracks.
I turned the head over and saw that the long crack from the spark plug to the exhaust valve has propagated all the way through to the outer surface of the head.
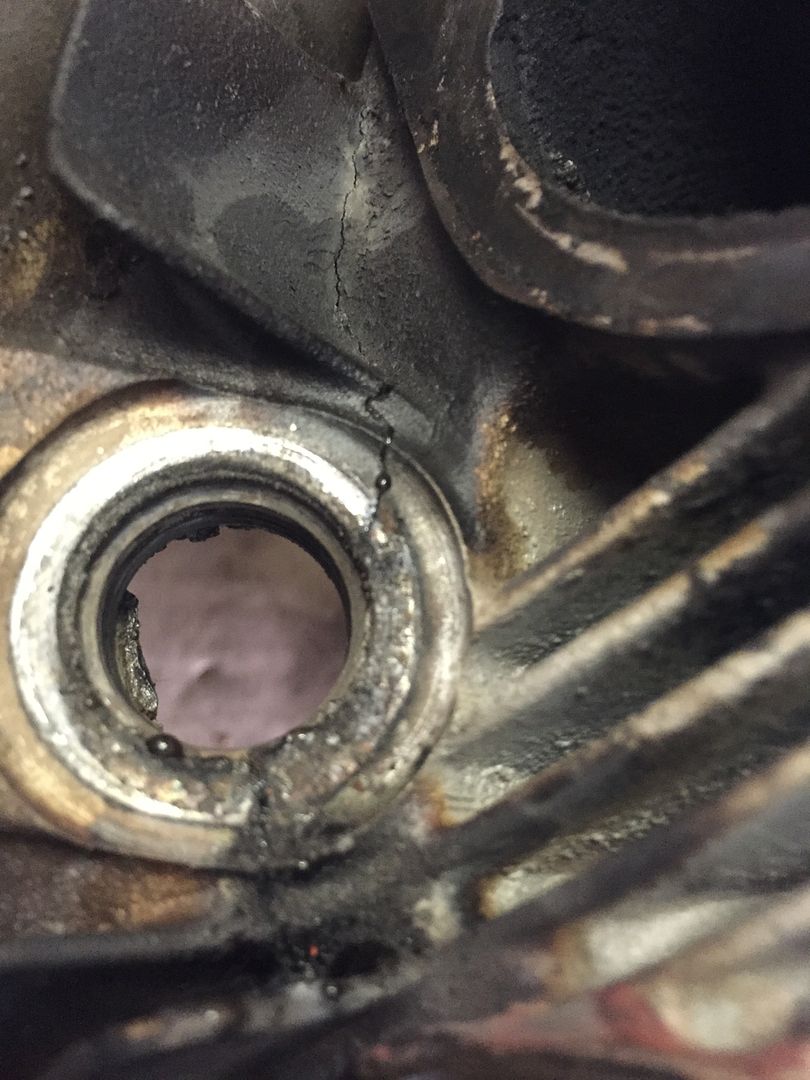
I think we were very lucky with this incident. The head didn't fly off and cause any further damage, the tow-pilot had enough power to maneuver to a safe location to wave-off the glider and if the head hadn't failed, in the future, the existing crack could have caused valve-seat failure and subsequent catastrophic engine failure.
Last edited by India Four Two; 12th Jul 2015 at 22:37. Reason: Added photo
Join Date: Jan 2008
Location: Canada
Posts: 631
Likes: 0
Received 0 Likes
on
0 Posts
From another thread, but on topic here. The topic is glide landings, and practice:
Shock cooling is a very real risk, however, the risk is at the first closing of the throttle, and perhaps accompanying dive, during which air cooling is plentiful, and internal heating minute. Once the throttle has been rapidly closed, any damage has been done. Further operation of the throttle will no longer affect shock cooling risk, other than a complete repeat of the cruise power to idle cycle.
As the engines continues to idle, while you glide down, checking that it will still develop power is a good habit, but you don't have to open the throttle far to determine that. If it's a cold winter day, then yes, simply warming the engine is a good idea, in anticipation of opening the throttle again at the bottom of the glide. That is about the same as allowing the engine to warm up after start, before takeoff. Conducting forced approach practice on very cold days is perhaps necessary, but far from ideal. Otherwise, just operate the throttle gently, and regularly satisfy yourself that the engine is still ready to provide power when needed.
I've picked the field, it's doable, the glide is shaping up nicely then the instructor opens the throttle 'to avoid shock cooling the engine' thus blowing the approach right there. Thanks a bunch, Dick.
What is it with this shock cooling sh*t anyway? We weren't at full bore when you pulled the mixture.
What is it with this shock cooling sh*t anyway? We weren't at full bore when you pulled the mixture.
As the engines continues to idle, while you glide down, checking that it will still develop power is a good habit, but you don't have to open the throttle far to determine that. If it's a cold winter day, then yes, simply warming the engine is a good idea, in anticipation of opening the throttle again at the bottom of the glide. That is about the same as allowing the engine to warm up after start, before takeoff. Conducting forced approach practice on very cold days is perhaps necessary, but far from ideal. Otherwise, just operate the throttle gently, and regularly satisfy yourself that the engine is still ready to provide power when needed.
Join Date: Nov 2005
Location: UK
Age: 78
Posts: 249
Likes: 0
Received 0 Likes
on
0 Posts
The first error in the operation is NOT closing the cooling flap at top of climb when throttling back, this and throttling back and speeding up is cooling the cylinders to fast. Only one cooling operation should be carried out at a time.
The Lasham Gliding Society operation procedure should be followed to the letter or cylinders will crack.
What is the cylinder head temperature limit being used because, Lycomings 475f limit is far to high. For long Life no head should go past 380f. If above take care, once below 380f research by Lasham shows shock cooling is no longer a problem.
The statement the Lycoming 360 range of engines is reliable is a joke.
These engines are a collection of design faults, from the under cooled valve gear, the high wear cam that rusts when all the oil drains off it, the shaving of the cooling fins on one side that causes the cylinder to expand oval may be the reason they crack like this one. The aluminium wrist pin blanks which keep it centred in the piston breaking up and rolling over scoring the cylinder walls. Running the cylinder up at the 475f temp limit anneals the oil control ring, which loses spring tension and rolls over, oil use goes very high and oil triggers detonation.
Then there are the flexing crank cases oil leaks and centre bearing problems.
If you have to operate a Lycoming 360, if it can be fitted, use a roller cam follower version to reduce cam wear and get a bit more power. IF possible fit the highest bleed down rate lifters to push as much oil into the valve gear for cooling as possible, make shore the valve guides are the new hardened type and reamed to the correct clearance to reduce valve sticking.
The crank case has the groves machined across the centre bearing support web so high pressure oil is not squirted out of the case seam.
All cooling ducting is in good condition and in place. If the shaved of cooling fin side of a cylinder has ducting flush with the side of the cylinder, it will bloke off cooling and it will have high temp problems, open up a gap for some air will help, a small stripe of high temp silicon glued to the ducting in line with air flow can help. This a big problem on cyl 3 in Cessna Cardinals.
I believe a recording 4 cylinder engine monitor is a must on 360s or you have no idea how its breaking up.
As you can guess I am not a fan of the 360 to many bad and expensive failures. Last twist is Lycoming say it should be operated 40 hours a month to make TBO and all failures are caused by the pilot, YA
Forgot one thing on the new cylinder check there is no casting flash between the fins on the head Lycomings wonderful quality control procedures some time misses this, if not cleared head will run hot.
The Lasham Gliding Society operation procedure should be followed to the letter or cylinders will crack.
What is the cylinder head temperature limit being used because, Lycomings 475f limit is far to high. For long Life no head should go past 380f. If above take care, once below 380f research by Lasham shows shock cooling is no longer a problem.
The statement the Lycoming 360 range of engines is reliable is a joke.
These engines are a collection of design faults, from the under cooled valve gear, the high wear cam that rusts when all the oil drains off it, the shaving of the cooling fins on one side that causes the cylinder to expand oval may be the reason they crack like this one. The aluminium wrist pin blanks which keep it centred in the piston breaking up and rolling over scoring the cylinder walls. Running the cylinder up at the 475f temp limit anneals the oil control ring, which loses spring tension and rolls over, oil use goes very high and oil triggers detonation.
Then there are the flexing crank cases oil leaks and centre bearing problems.
If you have to operate a Lycoming 360, if it can be fitted, use a roller cam follower version to reduce cam wear and get a bit more power. IF possible fit the highest bleed down rate lifters to push as much oil into the valve gear for cooling as possible, make shore the valve guides are the new hardened type and reamed to the correct clearance to reduce valve sticking.
The crank case has the groves machined across the centre bearing support web so high pressure oil is not squirted out of the case seam.
All cooling ducting is in good condition and in place. If the shaved of cooling fin side of a cylinder has ducting flush with the side of the cylinder, it will bloke off cooling and it will have high temp problems, open up a gap for some air will help, a small stripe of high temp silicon glued to the ducting in line with air flow can help. This a big problem on cyl 3 in Cessna Cardinals.
I believe a recording 4 cylinder engine monitor is a must on 360s or you have no idea how its breaking up.
As you can guess I am not a fan of the 360 to many bad and expensive failures. Last twist is Lycoming say it should be operated 40 hours a month to make TBO and all failures are caused by the pilot, YA
Forgot one thing on the new cylinder check there is no casting flash between the fins on the head Lycomings wonderful quality control procedures some time misses this, if not cleared head will run hot.
Last edited by horizon flyer; 12th Jul 2015 at 21:07.
Thread Starter
The first error in the operation is NOT closing the cooling flap at top of climb when throttling back
As I mentioned earlier, the Scout has a ground-adjustable cowl-flap, so we can't close it at the top of climb.
The statement the Lycoming 360 range of engines is reliable is a joke.
As far as the other issues go, I'm not a mechanic, just a pilot, so my concern is not so much with the maintenance and design problems, but more "Will it keep running while I'm airborne?"

Thanks for the suggestions. I'll pass them on.
Join Date: Jan 1999
Location: north of barlu
Posts: 6,207
Likes: 0
Received 0 Likes
on
0 Posts
PMA Cylinder ?
Was the cylinder a Lycoming part or was it a PMA cylinder ?
There is an AD on one of the PMA manufacturers cylinders to check for this very defect.
I am going to guess from the big white box that the cylinder n Question was a PMA item.
There is an AD on one of the PMA manufacturers cylinders to check for this very defect.
I am going to guess from the big white box that the cylinder n Question was a PMA item.
Last edited by A and C; 13th Jul 2015 at 08:28.
I42,
does the plane have a CHT gauge? I think for ops like towing and such it should be almost mandatory equipment.
Esp. considering that the same failure happened before.
does the plane have a CHT gauge? I think for ops like towing and such it should be almost mandatory equipment.
Esp. considering that the same failure happened before.
Thread Starter
DP,
Yes, it has a conventional CHT gauge, connected to one cylinder. Every tow plane I've ever flown has had one. Towing without one would be a recipe for cooking an engine. Our new C182 has an EDM-700 engine monitor, which is much more informative. In particular it has a mode which shows the rate of cooling during descent.
The previous failure was the more common cracking of the head between the spark plug and the exhaust valve. This failure is very rare. Our AME is submitting an SDR.
A and C,
Sorry I missed your post. Yes, it is a PMA cylinder. I'll check the manufacturer next time I'm at the field. Can you send me a PM with AD details?
Yes, it has a conventional CHT gauge, connected to one cylinder. Every tow plane I've ever flown has had one. Towing without one would be a recipe for cooking an engine. Our new C182 has an EDM-700 engine monitor, which is much more informative. In particular it has a mode which shows the rate of cooling during descent.
The previous failure was the more common cracking of the head between the spark plug and the exhaust valve. This failure is very rare. Our AME is submitting an SDR.
A and C,
Sorry I missed your post. Yes, it is a PMA cylinder. I'll check the manufacturer next time I'm at the field. Can you send me a PM with AD details?
Last edited by India Four Two; 14th Jul 2015 at 02:02.