If you build a Turbulent properly, and this goes for any wooden aircraft, you can expect that it will be still serviceable and flying in a hundred years time.
It might have been refurbished a few times along the way but there is no reason why it will not be flying.
As proof of this, two hangars from where I store my Tailwind, sits Bernie Pietenpol’s original Sky Scout. It is the actual aeroplane described in the Flying and Glider Manuals originally published in the 1930’s and reprinted by the EAA. It has been refurbished seven times now but sits immaculate in the hangar and is totally airworthy and is still flown.
it is 80 years old now.
Building a Turbulent is not as intimidating as it looks you know.
If you study the plans you will come to realise that the structure of a turbulent is glued up from a lot of small pieces of wood. most are probably less than a foot long.
The only long pieces of timber needed are the 4 longerons that form the corners of the fuselage and the spars in the wings and the tailfeathers.
The longerons can be spliced and can be made from pieces shorter than the fuselage.
The only pieces that need to be immaculate wood are the spars.
So what this means is that the task of finding suitable wood for most of the aeroplane is no where near as intimidating as it may first seem.
Spruce came into widespread use during the first world war because it had the best strength to weight ratio of all the woods and it could be obtained in long straight grained lengths that were clear of imperfections like knots. It isnt necessary to use spruce though. there are a lot of other suitable woods in the world.
Spruce that is suitable for building aeroplanes has a density of around 28 pounds per cubic foot.
Woods that have densities up to 35 pounds per cubic foot are still quite suitable for building aeroplanes.
Most people who pontificate about wood throw you a theoretical text on the structure of wood as though it will all be obvious. It took me ages of working with the wood to work out what was actually important. (you can still go and read a theoretical text if you want)
Wood as it is in the tree has a soft cellular structure full of moisture. to turn the green wood into a material suitable for use in the structures we build it must be dried out. This is called seasoning the wood. Once dried out the cellular structures become harder and becomes the engineering material we know as timber. Timber has about a 10% moisture content.
The cells are held together by lignins. I write lignins in the plural because lignin is not one molecule but is a whole family of related molecules. Some of those molecules soften when heated and some dont and this is one property of timber important to us in building aircraft.
Some of the pieces we build need fairly tight curves and we achieve this by heat softening the wood and shaping it while in the softened state. the upper curves of the wing ribs are formed this way. obviously a wood that does not soften with heat will make forming some of these parts nigh on impossible.
all things being equal the strength of a seasoned timber will vary pretty well according to its density. The timber used in the design work and the original builds of the Turbulent was spruce. How will we know if the wood we are looking at will be as strong? well its density will be a pretty simple guide.
Wood grows out in the open countryside. it is subjected to a never ending cycle of seasons. in warm conditions the wood grows fast and in colder seasons the wood grows slowly. The fast wood is less dense the cold weather wood is denser. so this means that wood does not have a uniform strength across the growth rings. What we do is select wood that has lots of growth rings close together to achieve a material with more uniform strength characteristics.
much of the wing rib trusses are just 5mm x 9mm wood so lots of growth rings will give us a more trustworthy structural material.
We are gluing the wood to build the structures so we need to avoid woods that will not allow us to achieve a strong glue bond. Resins and waxes occur naturally in some woods and these prevent good glue joints so it is pointless trying to use them.
A point to bear in mind here is that not all trees of a species grow the same so you may find some woods quite resinous and other woods of the same species will be quite acceptable.
Some woods turn out to be brittle, they break easily.
You can tell a lot about a wood by taking a long piece about 5mm x 9mm and bending it in your hands until it breaks. look at the break. if it broke on the outside of the curve the tensile strength is lower than the compressive strength. if it broke on the inside of the curve the compressive strength is lower than the tensile strength. if it pretty well broke evenly across the bend then both the compressive strength and tensile strength are the same. if it didnt bend far before it broke then it is a brash timber and will not be useful. could you twist the timber without it breaking? if it was a supple timber that bent and twisted a long way before breaking then it will probably be suitable.
Selecting a wood for aircraft building is a case of knowing what you want to achieve and selecting suitable examples of timber.
Stains, moulds and other discoloration are indications of bacterial and fungal problems in the timber. avoid these timbers and dont store such timber near your building stocks to prevent contamination.
Ok we think we have a timber that is suitable. We now need to check that we can achieve structurally sound glue joints using the timber. we need to saw up some timber into 5mm x 10mm strips. sand these so that they are smooth. we then cut them into lengths about 2 inches long, these are glued as in the photo and the glue is allowed to set completely before testing. (so 2 inch long pieces of wood glued with an inch overlap)
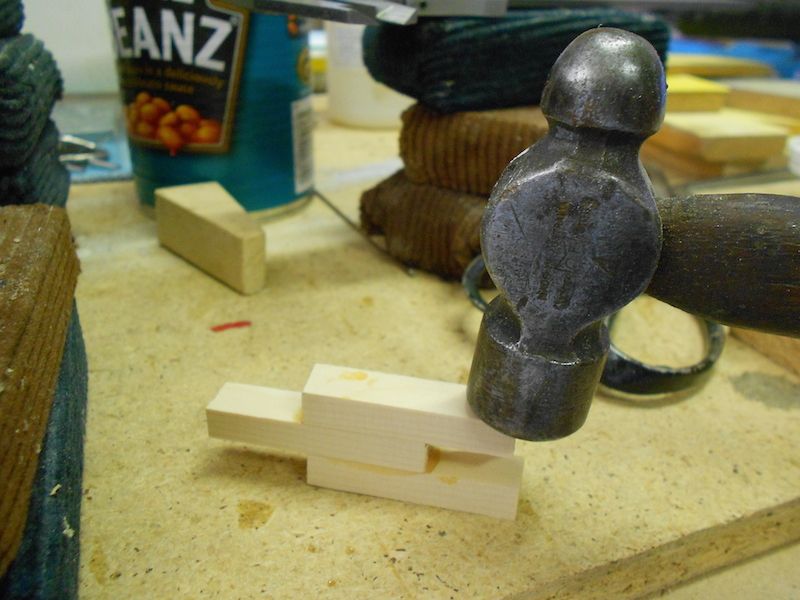
You can see the little ball pein hammer in the photo. to test the test piece we give it a hit with the hammer in the position of the hammer in the photo. we need to hit the test piece hard enough that we break it. our glue joints should be stronger than the wood that they join, achieving that strength consistently means that we can take the joints for granted and only be concerned by the strength of the wood. the reason that we hit the test piece with the hammer is to subject the glue joint to a sudden shock load.
should we ever find that the test piece breaks through the glue joint then that test has failed. if we have glue joints done in a similar manner in our aircraft then those joints must be seen as incompetent and they must be removed and done again.
what we should always see is that the glue joints survive the test and that the wood beaks.
Gluing will be the subject of another post. There are aspects of gluing that require a meticulous approach but once understood it isnt hard.
For much of the wood needed in the turbulent it is possible to saw it from planks that have knots. I used a plank 5” x 1” and about 8ft long for most of my wing ribs. the plank had 57 knots along it but about half an inch from the knot the grain was nice and straight again.
at the end of cutting the rib pieces from the straight grained sections I had two small hand fulls of knotted reject timber and over half the ribs made.